Understanding Foundry Sand Its Importance and Applications
Foundry sand is a crucial material used in the metal casting industry, comprising more than 90% of the total sand used in foundries. It plays a significant role in the production of metal parts and components by creating molds and cores that define the shape of the final product. This article will explore what foundry sand is, its properties, and its various applications in the casting process.
What is Foundry Sand?
Foundry sand, typically made from silica, is specifically processed for metal casting purposes. It is known for its excellent grain strength, thermal stability, and ability to retain its shape under high temperatures, making it ideal for producing intricate molds. The most common types of foundry sand include silica sand, olivine sand, and zircon sand. Each type has unique properties that make it suitable for different casting processes and materials.
Key Properties of Foundry Sand
1. Grain Shape and Size Foundry sand grains are generally round and smooth, which helps them pack well when forming molds. The size of the grains can vary, typically ranging from fine to coarse, impacting the mold's strength and surface finish.
2. Thermal Stability One of the most critical properties of foundry sand is its ability to withstand the high temperatures produced during metal casting without breaking down. This thermal stability is essential for producing molds that accurately preserve the desired shape and details of the casting.
3. Chemical Composition Foundry sand is predominantly composed of silica (SiO2), which provides its strength and thermal resistance. Additional minerals can be included to enhance specific properties, such as improving permeability for gas escape during the casting process.
4. Permeability Foundry sand must allow gases generated during the melting and pouring of metal to escape. High permeability ensures that air bubbles do not form within the mold, which could compromise the final product.
5. Reusability Foundry sand can often be reused multiple times, making it a cost-effective option for foundries. After casting, the sand can be reprocessed and combined with new sand to maintain its performance characteristics.
what is foundry sand
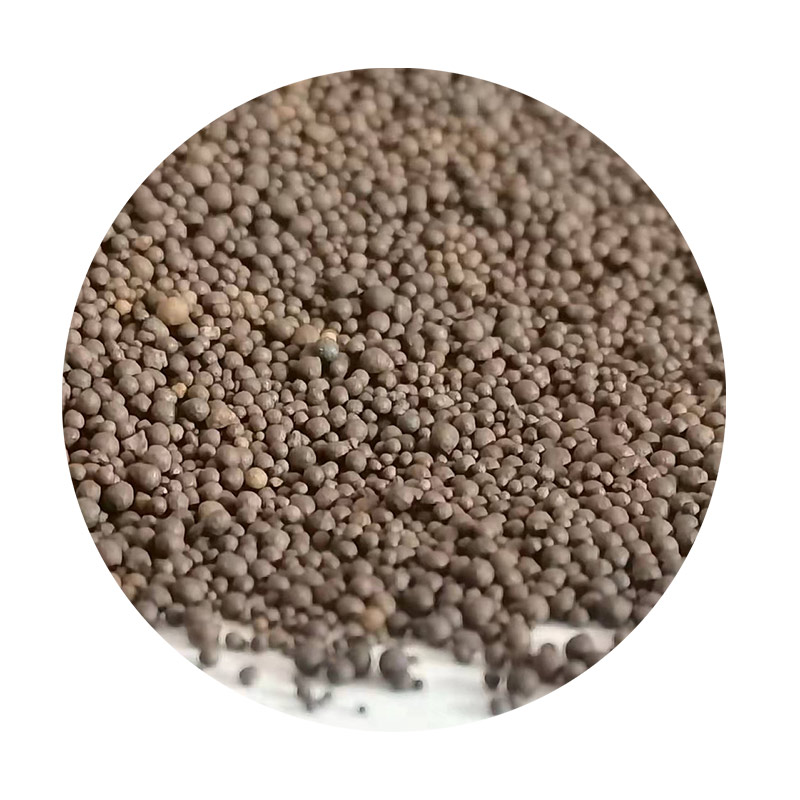
Applications of Foundry Sand
Foundry sand is primarily used in various metal casting processes, including
1. Sand Casting This is the most common casting method where foundry sand is used to create molds for metals such as aluminum, iron, and steel. The sand mold is formed around a pattern of the object to be cast, allowing for the production of complex shapes.
2. Investment Casting In this process, foundry sand can be utilized for creating cores and support structures. Investment casting is particularly known for producing high-precision components.
3. Cold Box and Hot Box Processes These methods involve using foundry sand bonded with a resin or other binding agents at room temperature or elevated temperatures to create strong, durable molds.
4. Core Making Foundry sand is essential for producing cores, which are used to create internal cavities in castings. Cores allow for more intricate designs and reduce the need for additional machining processes.
Environmental Considerations
With growing concerns about environmental sustainability, the foundry industry is adopting practices to recycle and reuse foundry sand. This process not only reduces waste but also minimizes the need for virgin materials. Additionally, innovations in binders and additives can help make casting processes more eco-friendly.
In conclusion, foundry sand is an indispensable material in the metal casting industry, known for its strength, thermal stability, and versatility. Understanding its properties and applications is vital for anyone involved in the manufacturing and engineering fields. As the industry continues to evolve, so too will the methods of utilizing foundry sand, paving the way for more efficient and sustainable casting practices.
Post time:നവം . 15, 2024 06:31
Next:wet sanding resin