Materials Used for Sand Casting
Sand casting is a versatile and widely used manufacturing process that facilitates the production of complex metal parts. Unlike other casting methods, sand casting employs a mold made of sand, which allows for excellent detail and intricate shapes. The choice of materials is crucial in this process, encompassing the mold, core, and the metal being cast. In this article, we will explore the primary materials used in sand casting and their respective roles.
Sand
The primary material used in sand casting is silica sand, known for its high melting point and ability to withstand the intense heat generated during the casting process. Silica sand is mixed with a binding agent, typically clay, to enhance its cohesion. The most commonly used clay in sand casting is bentonite, which helps the sand retains shape and improves the mold’s quality. Other additives, such as water and various chemical binders, can also be included to obtain the desired consistency and strength in the mold.
Mold Materials
The sand mold itself is a mixture of silica sand, clay, and water, known as green sand when used in its natural state. However, synthetic sands are also gaining popularity due to their more uniform grain size and shape, which can lead to improved mold accuracy and better surface finishes. These synthetic sands often consist of various materials such as resin-coated sand. This type of sand is treated with a resin that hardens when exposed to heat, allowing for greater detail and lower permeability.
Core Materials
what materials are used for sand casting
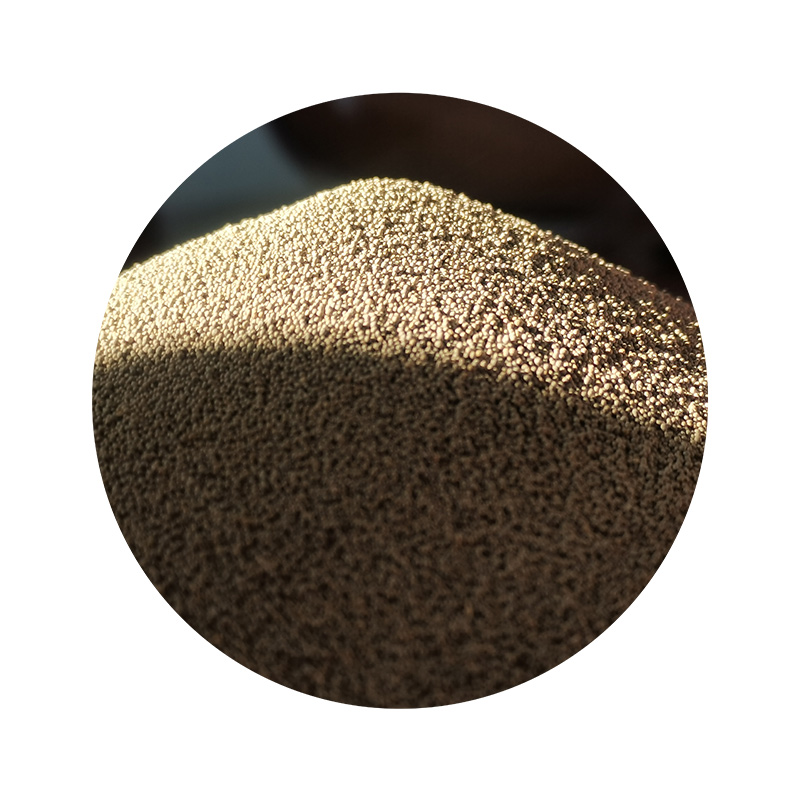
Cores are utilized in sand casting to create hollow sections within the cast part, and they are often made from the same sand mixture as the mold. However, core sands typically have different properties to withstand the heat during metal pouring. Common materials for cores include oil-bonded sands, which utilize oil in conjunction with sand, and sodium silicate-bonded sands, which harden when exposed to CO2 gas. Core materials must be designed to endure high temperatures while maintaining structural integrity.
Metal Alloys
The choice of metal for casting can vary widely, impacting the properties of the final product. Common metals used in sand casting include aluminum, iron, and bronze. Aluminum alloys, known for their lightweight and corrosion resistance, are often chosen for automotive parts and consumer products. Cast iron is favored for its wear resistance and strength, making it ideal for engine components and heavy machinery. Bronze, known for its excellent casting characteristics and aesthetic appeal, is frequently used for decorative items and marine applications.
Additional Materials
Beyond sand and metals, several other materials play vital roles in the sand casting process. This includes coatings, which are applied to the mold surfaces to improve surface finish and prevent metal adhesion. Common coatings include graphite and water-based ceramic materials. Additionally, the sand casting process may integrate recovery systems for recycling used sand, contributing to environmental sustainability.
Conclusion
In conclusion, the materials used in sand casting are diverse and integral to the effectiveness of the process. From the selection of silica sand and binding agents to the choice of metals and additional coatings, each material must be carefully chosen to optimize the casting process. As technology continues to advance, the development of new materials will likely enhance the efficiency and quality of sand casting in various industries, making it an enduring choice for manufacturing complex metal components.
Post time:സെപ് . 19, 2024 17:21
Next:sand casting cost