Understanding Unique Sand Casting in Modern Manufacturing
Sand casting, one of the oldest and most versatile metal-forming techniques, continues to be a pivotal method in modern manufacturing. Unique sand casting bridges traditional techniques with contemporary demands for precision and customization, making it an invaluable process in various industries, including automotive, aerospace, and artistic applications.
The unique aspect of sand casting lies in its ability to produce intricate shapes and large components. It involves creating a mold from sand, which holds the shape of the desired item. This method enables manufacturers to fabricate objects in complex forms that might be challenging to achieve through other methods, such as die casting or forging. The sand used in this process can be easily shaped, making it possible to create molds that preserve fine details and intricate designs.
The Process of Unique Sand Casting
The sand casting process starts with preparing a pattern of the object to be cast. Patterns can be made from various materials, including wood, metal, or plastic, and are used to form the sand mold. The sand is typically mixed with a binding agent, such as clay, which helps it hold its shape during the casting process. This mixture is then packed around the pattern, and once the mold is formed, the pattern is removed to leave a cavity in the shape of the intended item.
Next, molten metal is poured into the mold cavity. The choice of metal depends on the application's requirements, including strength, weight, and heat resistance. Common metals used in sand casting include aluminum, bronze, and iron. Once the metal cools and solidifies, the mold is broken away to reveal the final product.
Advantages of Unique Sand Casting
unique sand casting
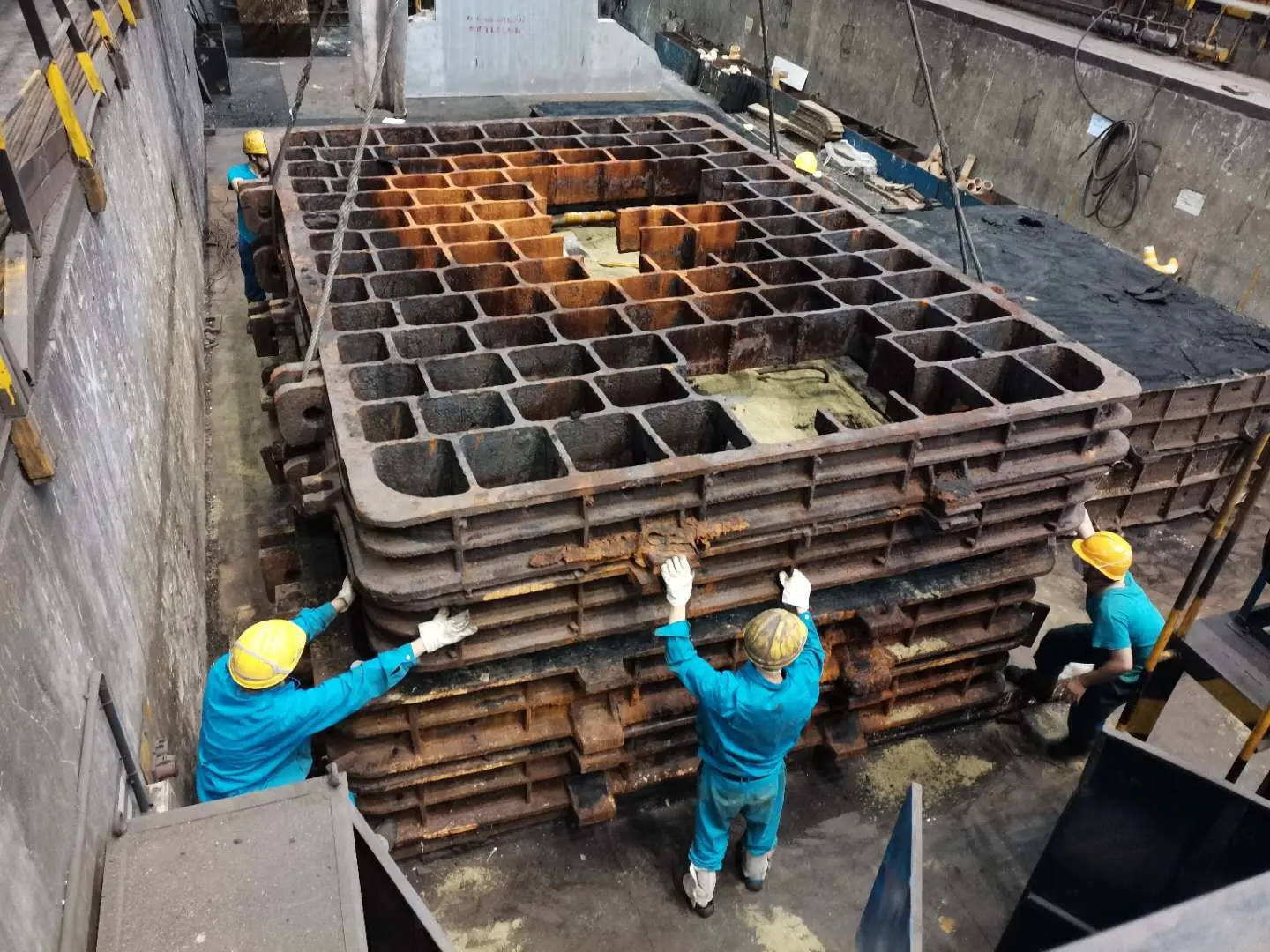
One of the most significant advantages of unique sand casting is its flexibility. Unlike other methods, the sand casting process allows for the production of small to medium-sized batches, making it ideal for custom pieces and prototypes. This is particularly beneficial for industries where specialized components are required, allowing for quick turnaround times without the need for expensive tooling.
Moreover, sand casting is cost-effective for larger parts. The materials used for sand molds are relatively inexpensive, and the processes involved require less specialized equipment compared to other casting methods. This makes sand casting an attractive option for small businesses and artisans looking to create unique, one-of-a-kind items without excessive financial investment.
Applications of Unique Sand Casting
The applications of unique sand casting span a wide range. In the automotive industry, it’s used to manufacture engine blocks, transmission cases, and various other components that benefit from the process’s flexibility and cost-effectiveness. In aerospace, the method can produce lightweight yet strong components that meet rigorous specifications.
Additionally, artists and sculptors often utilize sand casting to create unique sculptures and artworks. The ability to produce detailed and complex designs makes it an appealing choice for artistic endeavors.
Conclusion
As industries continue to evolve, unique sand casting remains a vital method in manufacturing, adept at adapting to new challenges and requirements. Its flexibility, cost-effectiveness, and suitability for producing customized and intricate parts ensure its relevance in a modern context. Whether in mass production or artisanal creations, unique sand casting continues to shape the future of manufacturing, proving that traditional methods still have a place in cutting-edge industry practices.
Post time:നവം . 06, 2024 04:29
Next:sand resin