Types of Sand Used in Foundry
The foundry industry is a pivotal sector that plays a critical role in manufacturing by producing metal castings via the sand casting process. One of the primary materials involved in this process is sand, which acts as a mold to shape molten metal into desired forms. The specific characteristics of sand can significantly affect the quality of the final product. Thus, understanding the types of sand used in foundries is essential for any foundry professional or enthusiast.
1. Silica Sand
Silica sand is the most common type of sand used in foundries due to its availability and excellent properties. Comprised primarily of quartz (SiO2), silica sand boasts a high melting point and good thermal stability, which makes it ideal for withstanding the temperatures encountered during metal pouring. Moreover, silica sand possesses a granular structure that provides good strength and permeability to the molds, allowing gases to escape as molten metal fills the cavity.
Despite its benefits, silica sand has some downsides, particularly concerning health. Prolonged inhalation of silica dust can lead to serious health issues such as silicosis. As a result, many foundries have begun implementing dust control measures and exploring alternative materials.
2. Green Sand
Green sand is a mixture of silica sand, clay, water, and various additives. The term green refers to the moisture content in the sand, not the color. Clay acts as a binder, helping the sand grains adhere to one another, which contributes to the strength of the mold. Green sand molds are often used for ferrous and non-ferrous metal castings due to their excellent dimensional accuracy and surface finish.
One of the advantages of green sand is its capacity for reclamation. After use, green sand can be processed and reused for future casts, making it an environmentally friendly option. Additionally, the moisture content in green sand helps to reduce the risk of sand collapse during the pouring of molten metal.
3. Dry Sand
In contrast to green sand, dry sand does not contain water and is typically used in applications requiring precision and durability. This type of sand provides high resistance to deformation and is less prone to changes in moisture content. In operations where detailed and intricate shapes are essential, dry sand is often preferred, particularly for thin-walled castings.
types of sand used in foundry
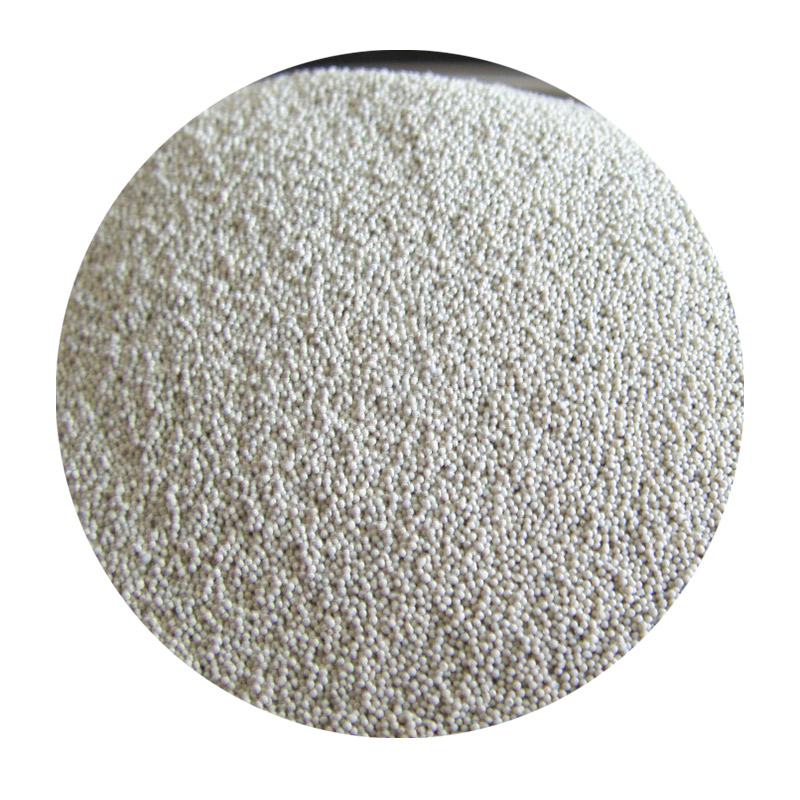
However, dry sand molds require additional bonding agents, such as resins or chemicals, to maintain mold strength and integrity during the casting process. These additives can increase production costs and necessitate careful handling and operational practices.
4. Shell Sand
Shell sand, also known as shell molding sand, is a mixture of fine sand and thermosetting resins. The sand is heated to a high temperature, causing the resin to harden and form a thin shell around the mold. This creates a highly durable cast that can withstand the intense heat from molten metal, producing high-quality and precise castings.
Shell sand is particularly useful for producing intricate designs and complex geometries. The molding process is faster than traditional methods, thereby reducing overall production time. However, the cost of materials and the need for specialized equipment can be a drawback for some foundries.
5. Investment Sand
Investment sand is a highly refined silica sand used in investment casting, which involves creating a wax model covered with a ceramic shell. Once the shell is formed, the wax is melted away, leaving a cavity that can be filled with molten metal. The fine grain size of investment sand enables the production of smooth and highly detailed castings, making it suitable for intricate designs commonly found in the aerospace and medical industries.
Investment sand does have a higher cost compared to other types of sand due to the additional processing required to achieve its fine texture and properties.
Conclusion
In conclusion, the selection of sand in foundries is a critical factor that directly influences the quality, durability, and precision of cast metal products. Silica sand, green sand, dry sand, shell sand, and investment sand each offer unique properties that cater to different casting needs. As the industry evolves, ongoing research and development of alternative materials and improvement in sand reclamation techniques will likely continue to shape the foundry landscape, ensuring that it remains a vital component of modern manufacturing.
Post time:ഡിസം . 10, 2024 21:58
Next:الرمال وتلميع الراتنج