The Role of Sand in Sand Casting A Comprehensive Overview
Sand casting is one of the oldest and most versatile manufacturing processes, widely used to create complex metal shapes and components. The fundamental element that makes sand casting possible is sand itself. Sand serves as the main mold material, crucial for creating the intricate forms required for various industrial applications. In this article, we will explore the different types of sand used in sand casting, the properties that make it suitable for this process, and its environmental impact.
Types of Sand Used in Sand Casting
The most commonly used sand in sand casting is silica sand, primarily composed of silicon dioxide (SiO₂). Silica sand is favored due to its high melting point, which allows it to withstand the heat generated during metal melting. It is also known for its durability and ability to maintain shape under high temperatures.
Another notable type of sand used in sand casting is olivine sand. Olivine is a naturally occurring mineral that provides excellent thermal stability and is less prone to expansion than silica. This property reduces the risk of defects like sand inclusion, which can occur in castings. Additionally, olivine sand is less reactive with molten metal, making it advantageous for certain alloy castings.
There is also a variety of synthetic sand composites made from recycled materials, such as resin-coated sand. This type of sand enhances mold strength and improves surface finish on cast parts. The resin coating binds the sand particles together, allowing manufacturers to create more precise and detailed molds that can improve the final product’s quality.
Properties of Sand in Casting
The essential properties of sand that make it ideal for casting include grain size, shape, permeability, and bonding characteristics. The grain size affects the mold's surface finish and resolution of the features on the final casting. For instance, finer sand can create smoother surfaces but may have lower strength compared to coarser sands.
sand used in sand casting
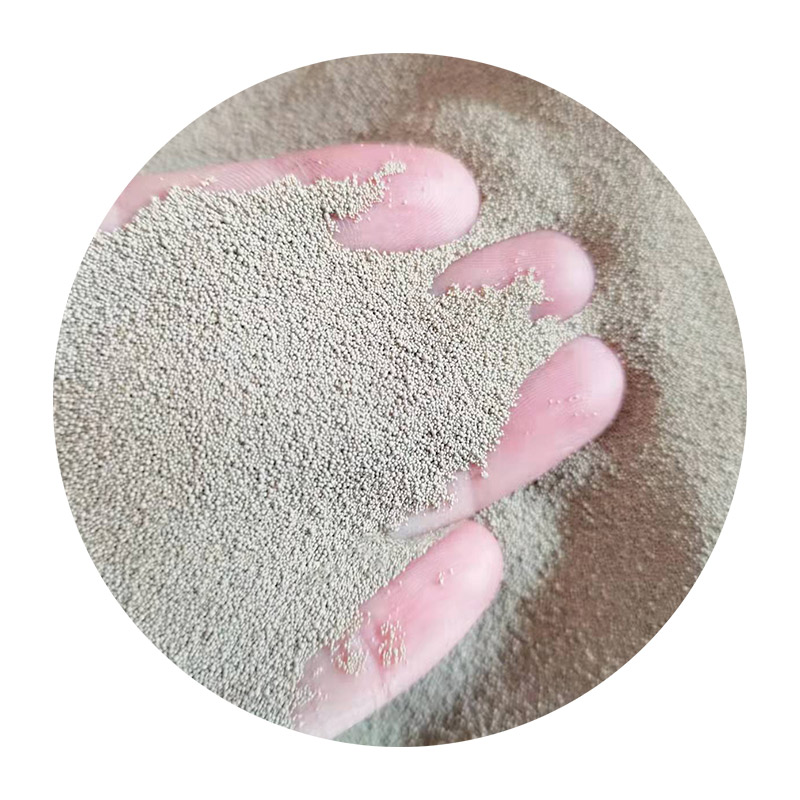
The shape of the sand grains also plays a critical role. Angular sand grains provide better interlocking characteristics, which contributes to the strength of the mold. Rounded grains, while easier to handle, often yield weaker molds due to less mechanical interlocking.
Permeability refers to the sand’s ability to allow gases to escape during the pouring of molten metal. High permeability is essential to prevent defects like blowholes in the castings. A proper balance of permeability and strength needs to be achieved to ensure the successful casting of high-quality parts.
Moreover, the bonding properties of the sand are crucial. Natural sands are often mixed with binders to improve their adhesive characteristics. These binders might be chemical (like sodium silicate or phenolic resins) or natural (like clay), which help the sand retain its shape when subjected to the weight of molten metal.
Environmental Considerations
While sand is abundant and generally regarded as a sustainable resource, environmental concerns about its extraction and usage cannot be overlooked. The mining of sand, especially from riverbeds and beaches, can lead to ecological damage, including habitat destruction and increased erosion.
To mitigate these issues, many manufacturers are increasingly turning to recycled sand, which not only reduces waste but also lessens the impact of mining activities. Additionally, advances in technology are leading to the development of more environmentally friendly binders and additives that help minimize the ecological footprint of sand casting.
Conclusion
In summary, sand is a vital component of the sand casting process, with various types and properties that influence the quality and characteristics of the final metal parts produced. Understanding the role of sand, from its selection to its environmental impacts, allows manufacturers to optimize their casting processes and contribute to more sustainable practices within the industry. Sand casting remains a cornerstone of metal processing, driven by the essential properties and versatility of sand itself, ensuring its continued relevance in modern manufacturing.
Post time:ഡിസം . 23, 2024 04:32
Next:super sand bond g2