The Sand Foundry Process A Comprehensive Overview
The sand foundry process remains one of the most cherished techniques in metal casting, dating back thousands of years. Its prominence in the manufacturing industry is attributed to its versatility, cost-effectiveness, and capability of producing complex shapes. This article delves into the intricacies of the sand foundry process, exploring its methodology, advantages, applications, and future trends.
Understanding the Sand Foundry Process
The sand foundry process involves creating metal castings by pouring molten metal into a sand mold. The sand, usually mixed with a binding agent, forms a mold that can withstand the heat of molten metal. This method can be broken down into several key steps
1. Pattern Making The first stage involves creating a pattern, which is a replica of the final product. Patterns can be made from various materials such as wood, metal, or plastic and are designed to be slightly larger than the finished piece to account for shrinkage during cooling.
2. Mold Creation Once the pattern is ready, it is used to form the mold. This is done by packing sand around the pattern, creating two halves of the mold (cope and drag). Each half is then removed carefully after the sand has set.
3. Core Making For more complex shapes, cores made from sand are also needed. These cores are placed inside the mold to create cavities within the final casting. Cores enhance the versatility of the sand foundry process by allowing for intricate internal geometries.
4. Mold Assembly After the molds (and cores) are prepared, they are assembled precisely, ensuring that the alignment prevents any metal leakage during pouring.
5. Pouring The molds are then heated to prepare them for the molten metal. The metal, often aluminum, iron, or bronze, is melted at high temperatures and poured into the mold through a sprue system.
6. Cooling Once the molds are filled, the metal is allowed to cool and solidify. The cooling time depends on the metal type and the thickness of the casting.
7. Shakeout and Finishing After the metal has solidified, the mold is broken apart to retrieve the casting. This is called shakeout. The casting then undergoes finishing processes, including trimming, grinding, and surface treatment to prepare it for use.
Advantages of the Sand Foundry Process
sand foundry process
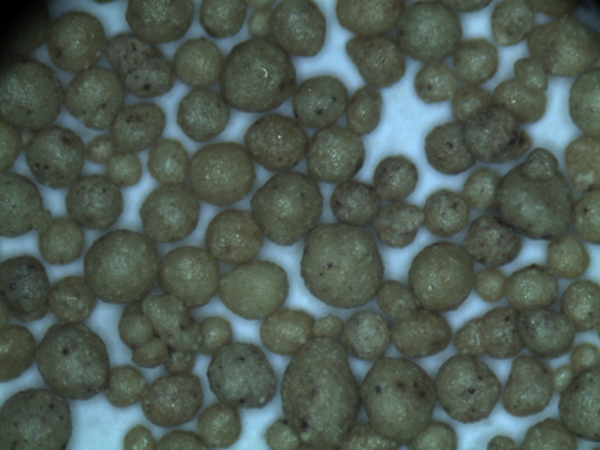
The sand foundry process offers numerous advantages
- Cost-Effectiveness The materials used, particularly sand, are relatively inexpensive. This makes the process suitable for both small and large production runs.
- Flexibility Sand molds can be easily altered or replaced, allowing for rapid changes in design without the need for extensive retooling.
- Good Surface Finish While sand casting does require finishing work, it is capable of achieving a good surface finish for most applications.
- Capability for Complex Geometries The process can handle intricate shapes and features that may be challenging for other casting methods.
Applications of Sand Casting
Sand casting is employed across various industries. For instance, in automotive manufacturing, it is used to produce engine blocks, cylinder heads, and transmission cases. In aerospace, lighter metals are cast to enhance fuel efficiency. Additionally, sand casting contributes significantly to the construction, marine, and artistic sectors by crafting everything from decorative elements to heavy machinery parts.
Future Trends and Innovations
As technology advances, the sand foundry process is evolving. The integration of automation and robotics in pattern making and mold production is streamlining operations and improving efficiency.
Furthermore, advancements in additive manufacturing, or 3D printing, are revolutionizing pattern production, allowing for faster prototyping and more intricate designs. Sustainability is also becoming a focal point, with foundries exploring the use of recycled sand and ways to minimize waste.
Conclusion
The sand foundry process has stood the test of time, proving itself as a cornerstone of manufacturing. Its ability to produce complex shapes at a reasonable cost makes it invaluable in various industries. With ongoing innovations and a focus on sustainability, the future of sand casting looks promising, continuing to adapt to the evolving needs of modern manufacturing. As industries push toward greater efficiency and environmental responsibility, the sand foundry process is set to play a critical role in shaping tomorrow's products.
Post time:ഡിസം . 25, 2024 15:57
Next:how to sand 3d print