The Art and Science of Sand Casting in Metalworking
Sand casting, one of the oldest and most versatile metalworking processes, combines artistry with engineering to create a range of metal components and products. This method, dating back thousands of years, utilizes sand as a primary material to form molds that can withstand high temperatures. This article explores the intricacies of sand casting, its applications, advantages, and the future of this timeless technique.
At its core, sand casting involves creating a mold from sand, into which molten metal is poured. The basic process begins with the creation of a pattern, usually made from a material like wood or metal, which represents the final product. This pattern is placed into a mixture of sand and a binding agent, forming a mold cavity. Once the sand has solidified around the pattern, the mold is separated, and the pattern is removed, leaving a hollow form that mirrors the desired object.
The Art and Science of Sand Casting in Metalworking
The porosity of sand molds allows for excellent heat dissipation, enabling intricate designs and complex shapes to be produced without the risk of damaging the final product. Furthermore, sand casting is especially advantageous for producing large components, as it can handle sizable pieces that other methods may struggle with. This characteristic is vital, for instance, in the manufacturing of engine blocks and large valve bodies in the automotive sector.
sand cast metal
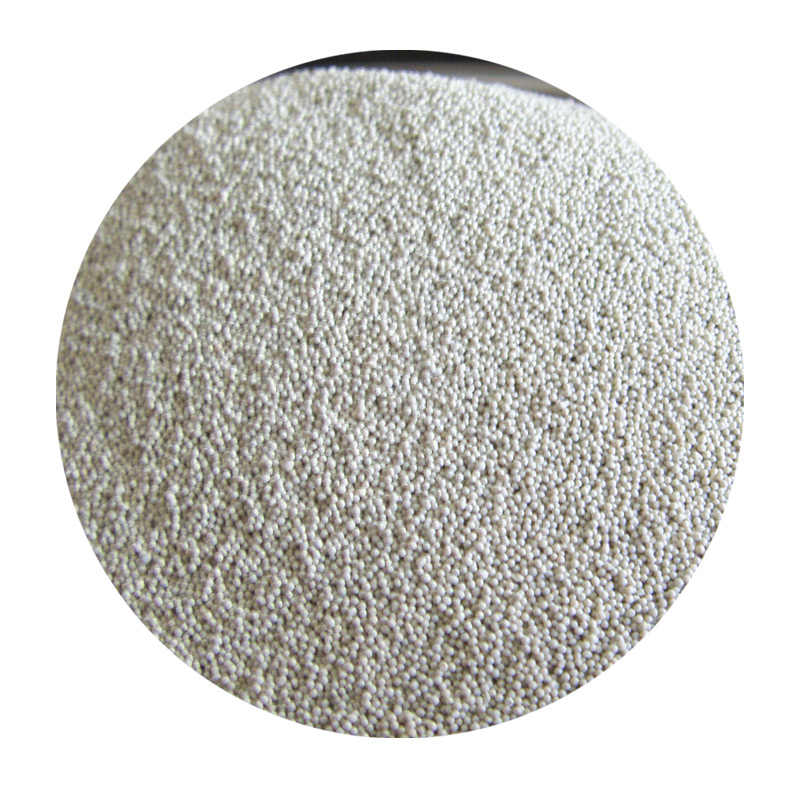
However, sand casting is not without its challenges. Surface finish, dimensional accuracy, and the potential for defects, such as sand inclusion or porosity within the cast part, can present issues. These factors necessitate a high level of precision in both the mold design and the casting process. Nevertheless, advancements in technology, including the use of computer-aided design (CAD) and computer-aided manufacturing (CAM), have significantly improved the precision and efficiency of sand casting operations.
In recent years, the environmental impact of casting processes has come under scrutiny. Fortunately, innovations in sand recycling and green sand casting techniques have emerged. These methods minimize waste by reusing sand from previous molds, thereby reducing the need for new materials and lessening the environmental footprint of the operation.
Looking towards the future, the combination of sand casting with modern technologies is paving the way for new possibilities. Additive manufacturing, or 3D printing, is beginning to merge with traditional sand casting methods. 3D-printed sand molds can be created rapidly, allowing for shorter lead times and the ability to make rapid prototyping cost-effective and efficient. This synergy between old and new techniques suggests a promising future for sand casting.
In conclusion, sand casting remains a vital technique in metalworking, balancing the demands of modern manufacturing with the time-tested principles of craftsmanship. As industries continue to seek innovative solutions, the adaptability and efficiency of sand casting will play a crucial role in shaping the future of metal fabrication. From artistic sculptures to essential machinery components, the legacy of sand casting endures, proving essential in both traditional and contemporary settings.
Post time:ഡിസം . 12, 2024 19:18
Next:importance of sand casting