Sand Casting Foundry An Overview
Sand casting, one of the most versatile and widely used metal casting processes, has been an integral part of the manufacturing industry for centuries. This technique allows for the production of complex shapes and large components, making it an invaluable method in various sectors including automotive, aerospace, and machinery.
What is Sand Casting?
At its core, sand casting involves creating a mold from a sand mixture in which molten metal is poured to create a desired shape. The primary materials used in sand casting are sand, a binder (usually clay), water, and the metal to be cast. The sand provides the mold's structure, while the binder helps the sand grains stick together.
The Process of Sand Casting
The sand casting process consists of several steps. The first step is pattern making, where a replica of the final product is created, typically from wood, metal, or plastic. This pattern is then used to create a mold in the sand. The mold is formed by compressing sand around the pattern, and once set, the pattern is removed, leaving a cavity for the molten metal.
Next comes the assembly of the mold. This often involves two halves that will be clamped together to form a complete mold cavity. In addition, risers and pour holes are incorporated to facilitate the flow of molten metal and allow for the escape of gases.
Once the mold is prepared, molten metal is poured into the cavity. The metal, typically heated to temperatures exceeding 1,500 degrees Fahrenheit (800 degrees Celsius), fills the mold and takes on the shape of the cavity. After cooling and solidification, the mold is broken apart, revealing the cast part.
Finally, the casting undergoes finishing processes such as grinding, machining, and cleaning to achieve the desired surface quality and dimensional accuracy.
sand casting foundry
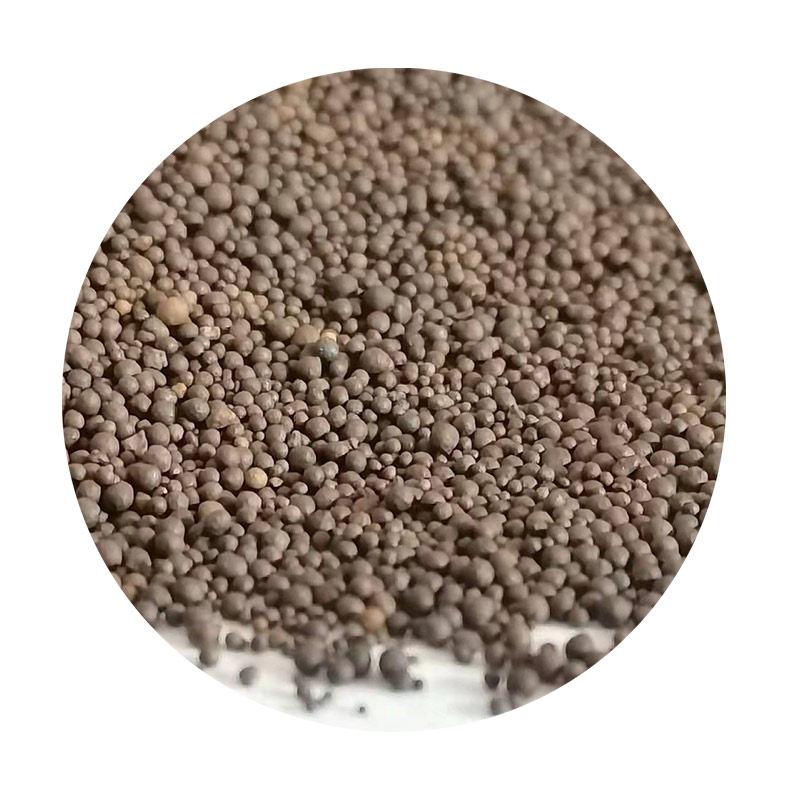
Advantages of Sand Casting
Sand casting offers numerous advantages. One of the most significant is its ability to create complex shapes. The flexibility of sand molds allows for intricate designs that would be difficult or impossible to achieve with other casting methods. Furthermore, this process is highly cost-effective for both small and large production runs, making it ideal for a wide variety of applications.
Additionally, sand casting can accommodate almost any metal, including ferrous and non-ferrous alloys. This provides foundries with great versatility in material selection, allowing them to meet specific performance requirements for different applications.
Challenges in Sand Casting
Despite its advantages, sand casting has its challenges. The quality of the final product can be affected by various factors, including the quality of the sand, the skill of the operator, and environmental conditions. Defects such as porosity, misalignment, and surface imperfections can occur if the process is not carefully controlled.
Moreover, the manual nature of many steps in sand casting can lead to variability in production. Automation and advanced technologies are increasingly being integrated to mitigate these issues, improving consistency and efficiency.
Conclusion
Sand casting foundry remains a cornerstone of the manufacturing landscape. With its ability to produce intricate, high-quality components at a relatively low cost, it continues to thrive even in an era of advanced manufacturing technologies. As industries evolve and the demand for complex parts grows, the sand casting process will likely adapt, incorporating new materials and methods to enhance its capabilities.
In conclusion, understanding the fundamentals and intricacies of sand casting not only highlights its importance in modern manufacturing but also showcases its potential for future advancements, cementing its place in both industry and technology. As foundries explore innovations and efficiencies, sand casting will undoubtedly remain a vital process for producing components that meet the ever-increasing demands of today’s industries.
Post time:നവം . 19, 2024 13:18
Next:ceramic sand