Understanding Sand Casting Costs Factors and Considerations
Sand casting is one of the oldest and most versatile metal casting processes used in manufacturing. It involves pouring molten metal into a mold made of sand, which is then removed once the metal has cooled and solidified. While sand casting is favored for its ability to produce complex shapes and accommodate various metals, understanding its costs is crucial for manufacturers, especially when aiming for efficiency and profitability.
Factors Influencing Sand Casting Costs
1. Material Selection The choice of metal significantly affects casting costs. Common materials like aluminum, iron, and bronze have varying price points, and their properties influence the casting process's complexity and duration. For instance, aluminum typically costs less compared to high-performance alloys, leading to lower overall casting expenses.
2. Pattern Costs Patterns are replicas of the final product and are essential for creating the mold. The complexity and size of the pattern play a critical role in determining costs. Simple patterns can be made from wood or inexpensive materials, while intricate patterns may require investment in more durable materials like metal or advanced manufacturing techniques.
3. Mold Production The creation of sand molds involves labor, materials, and time. The process can be labor-intensive, especially for complex designs requiring multiple parts. The use of mechanized equipment can reduce costs but requires an initial investment. Reusable molds can also drive down costs over time as they can be used for multiple casting cycles.
4. Labor Costs Skilled labor is essential in sand casting, from mold preparation to pouring and finishing. The complexity of the task at hand often dictates labor costs. Regions with a higher cost of living or stricter labor regulations may face increased labor expenses, impacting the overall cost of the casting process.
5. Production Volume Scale plays a pivotal role in casting costs. Smaller production runs often incur higher per-unit costs due to setup times and pattern creation expenses. Conversely, larger production volumes can benefit from economies of scale, spreading fixed costs over a greater number of units, thereby reducing the per-unit cost.
sand casting cost
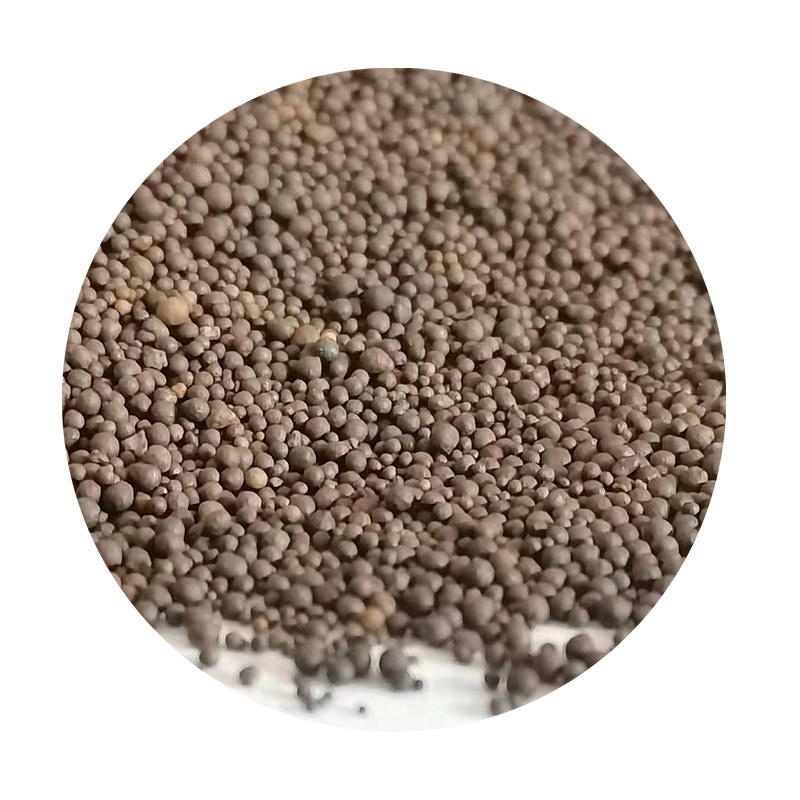
6. Post-Casting Processing Once the casting is complete, secondary processes such as machining, surface treatment, or assembly may be required. These added processes increase the overall cost. Companies must evaluate their post-processing needs based on the final product requirements to gauge total expenditure accurately.
7. Quality Control Ensuring high-quality castings necessitates rigorous quality control measures. Implementing testing and inspection processes to mitigate defects can increase costs. However, this investment is vital to maintain product integrity and prevent costly rework or failures.
8. Environmental Considerations With growing awareness and regulations regarding environmental impact, additional costs may arise from implementing eco-friendly practices in the sand casting process. This includes waste management, emissions control, and the use of sustainable materials. Companies that prioritize sustainability must factor in these costs as part of their production budget.
Cost-Benefit Analysis
While the initial costs related to sand casting may appear challenging, manufacturers must conduct a thorough cost-benefit analysis to understand its value. The ability to produce complex shapes efficiently, the flexibility to work with different metals, and the potential for low tooling costs in small production runs can make sand casting an advantageous choice.
Adopting advanced technologies, such as computer-aided design (CAD) and computer numerical control (CNC) machining, can also enhance precision and reduce waste, making the process more cost-effective over time. Automation in certain areas of the casting process can further drive down labor costs and improve the speed of production.
Conclusion
In conclusion, while sand casting presents various cost factors to consider, its benefits in terms of flexibility and capability cannot be overlooked. Manufacturers need to evaluate each aspect of the sand casting process, from material selection and pattern production to labor and post-processing costs, to understand the full spectrum of expenses involved. By doing so, they can make informed decisions, optimize their operations, and ultimately maximize profitability in their sand casting endeavors. As the industry evolves, embracing technological advancements and sustainable practices will become increasingly essential in managing costs and driving future success in sand casting.
Post time:നവം . 05, 2024 06:21
Next:what is sand casting in engineering