The Advantages of Sand Casting
Sand casting, also known as sand mold casting, is a popular manufacturing process that involves creating metal parts by pouring molten metal into a sand mold. This versatile technique is widely utilized in various industries, including automotive, aerospace, and art, due to its numerous advantages. Here, we will explore some of the key benefits of sand casting that contribute to its enduring popularity.
1. Cost-Effectiveness
One of the most significant advantages of sand casting is its cost-effectiveness. The materials used in the process, primarily sand, are inexpensive and readily available. Unlike other casting methods that may require specialized equipment or materials, sand casting can be performed using basic tools and setup, reducing the overall production costs. This makes it an ideal choice for both small-scale production and large-scale manufacturing.
2. Flexibility and Versatility
Sand casting offers remarkable flexibility in terms of design and product variation. The sand molds can be easily shaped into intricate and complex geometries, which allows for the creation of a wide range of components, from simple shapes to highly detailed designs. This adaptability opens the door for customized solutions, enabling manufacturers to cater to specific client requirements and specifications.
3. Large-Scale Production Capability
Unlike some casting methods that may be limited in size or scale, sand casting can accommodate large components. It is suitable for creating heavy and oversized parts, which makes it applicable for industries that require large machinery or automotive components. The ability to produce sizable items efficiently is a crucial advantage for manufacturers looking to optimize their production capabilities.
4. High Tolerance for Different Metals
sand casting advantages
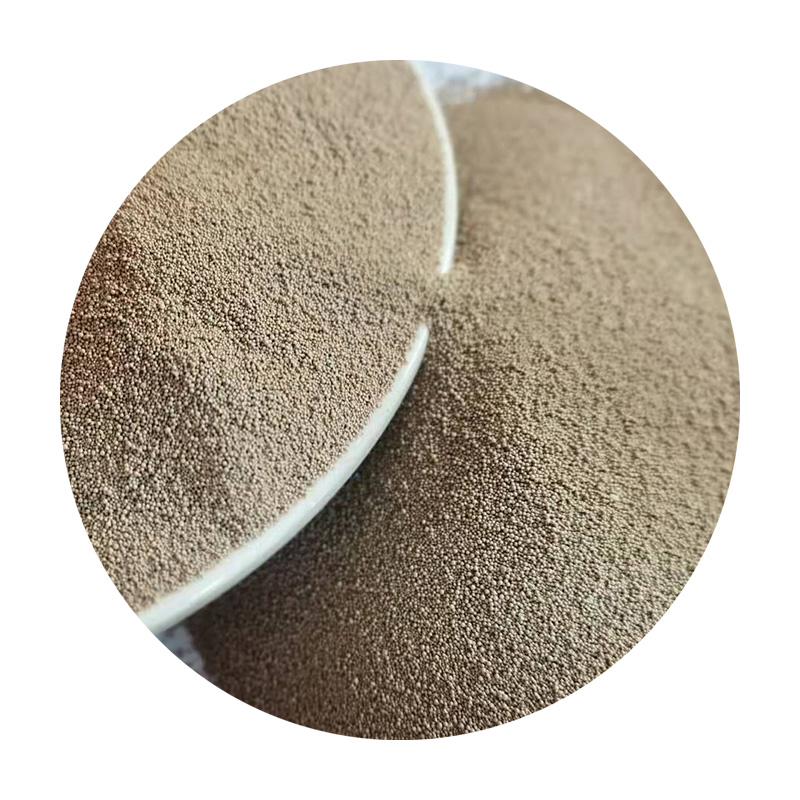
Sand casting is compatible with a variety of metals, including iron, aluminum, bronze, and magnesium. This broad compatibility allows manufacturers to choose the best metal for their specific application, based on factors such as strength, weight, and corrosion resistance. The ability to work with different materials further enhances the versatility of sand casting and expands its range of applications.
5. Minimal Waste Generation
The sand used in the casting process can often be reused. After a casting is completed, the sand can be reclaimed, processed, and used again for subsequent molds. This not only reduces waste but also lowers material costs, making the process more sustainable. Furthermore, sand casting generates less waste compared to other methods, contributing to more environmentally friendly manufacturing practices.
6. Simplicity of the Process
The sand casting process is relatively simple, which allows for easier training of operators and reduced labor costs. The steps involved in creating sand molds and pouring molten metal are straightforward, making the process accessible even to those with limited experience. Additionally, the simplicity of the process means that production can be ramped up quickly in response to demand.
7. Quality Surface Finish
One of the common misconceptions about sand casting is that it results in rough surface finishes. However, with the right techniques and practices, sand casting can achieve a high-quality surface finish that meets the requirements of many applications. Surface treatments, coatings, and machining can further enhance the finish, making it suitable for aesthetic and functional components.
Conclusion
In summary, sand casting is a highly advantageous manufacturing process that provides cost savings, flexibility, and versatility. Its ability to handle various metals, accommodate large components, and generate minimal waste makes it an attractive option for many industries. As technology continues to evolve, sand casting remains a reliable and effective choice for producing high-quality parts, ensuring its relevance in the modern manufacturing landscape. Whether for one-off custom components or mass production, the benefits of sand casting position it as a cornerstone of metal fabrication.
Post time:ഡിസം . 15, 2024 09:31
Next:Exploring Various Types of Foundry Sand for Metal Casting Applications