Resin Coated Sand Process A Key Innovation in Metal Casting
The resin coated sand process has emerged as a pivotal innovation in the metal casting industry, revolutionizing the way molds and cores are produced. This advanced method involves the application of a thermosetting resin to silica sand, which enhances the properties of the sand and improves the overall efficiency and quality of the casting process. In this article, we will explore the intricacies of the resin coated sand process, its advantages, applications, and the future it holds in metal casting.
At its core, the resin coated sand process begins with traditional silica sand, which is a common material used in the production of molds and cores. The silica sand is first dried to remove any moisture and then mixed with a resin binder, typically a phenolic resin, along with a catalyst. The mixture is thoroughly blended to ensure a uniform coating of resin on the sand particles. Once coated, the sand is typically cooled, allowing the resin to harden and bond the individual sand grains together.
One of the primary advantages of the resin coated sand process is the enhanced strength and durability it provides to molds and cores. The resin coating allows for better dimensional accuracy and surface finish, which are crucial factors for high-quality castings. The improved strength of the sand mix also facilitates the production of intricate designs and complex shapes that may be challenging to achieve using traditional sand casting methods.
Moreover, the resin coated sand process reduces the likelihood of defects such as blow holes, shrinkage, and surface imperfections that can negatively impact the final product. This is particularly important in industries where precision is paramount, such as automotive and aerospace manufacturing. Additionally, this process allows for faster mold curing times, resulting in shorter lead times for production. As a result, manufacturers can respond more quickly to market demands and improve overall productivity.
resin coated sand process
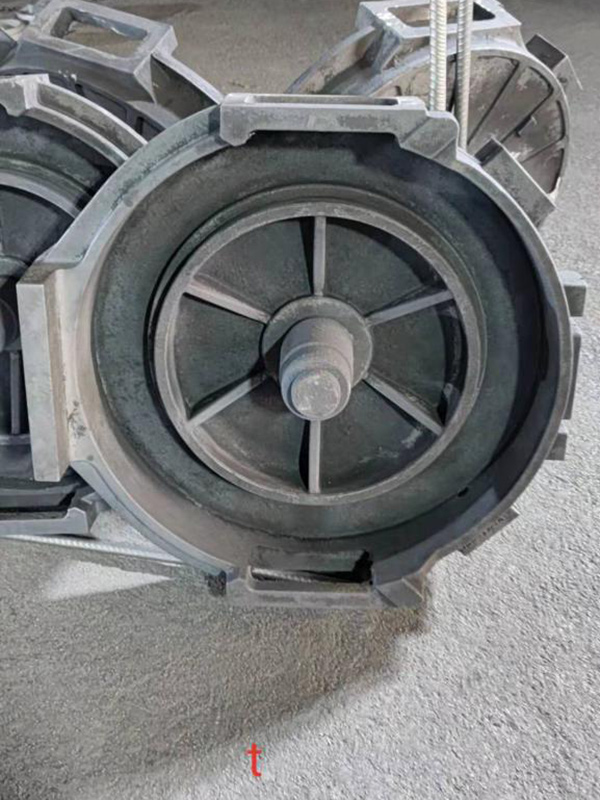
Another noteworthy aspect of the resin coated sand process is its versatility. It can be adapted to various types of metal casting, including ferrous and non-ferrous materials. This flexibility allows foundries to use the same sand mixture for different applications, which streamlines their operations and reduces material costs. Furthermore, the process can be customized to achieve specific strength, permeability, and thermal properties based on the casting requirements.
While the resin coated sand process offers many benefits, it is essential to consider the environmental implications. The use of chemical resins in the casting process has raised concerns regarding emissions and waste disposal. However, continuous advancements in resin technology are leading to more eco-friendly alternatives that minimize environmental impact. Additionally, many foundries are investing in advanced ventilation and filtration systems to mitigate any potential hazards associated with resin fumes.
As industries continue to innovate, the resin coated sand process is expected to evolve further. New research and development efforts are focused on improving the performance and sustainability of resin binders, as well as exploring the use of alternative materials. The integration of digital technologies, such as additive manufacturing and machine learning, is also being investigated to enhance the efficiency and accuracy of the resin coated sand casting process.
In conclusion, the resin coated sand process has significantly transformed the landscape of metal casting, offering superior strength, precision, and versatility compared to traditional methods. Its ability to produce high-quality castings for a wide range of applications makes it an invaluable asset for manufacturers. As the industry moves towards more sustainable practices and embraces technological advancements, the resin coated sand process is poised to play a crucial role in shaping the future of metal casting.
Post time:നവം . 10, 2024 17:15
Next:Advantages of Sand Casting in Manufacturing Processes