Parts of Sand Casting
Sand casting, one of the oldest and most versatile metal casting processes, is widely used in various industries for the production of metal components. The process involves several key parts and stages, each playing a critical role in achieving the desired quality and efficiency of the final product. This article will explore the different components involved in sand casting, including patterns, molds, sand, cores, and finishing processes.
1. Patterns
Patterns are replicas of the desired production part and are typically made from materials such as wood, plastic, or metal. The pattern is created slightly larger than the final component to account for shrinkage that occurs during the cooling process. There are different types of patterns, such as solid patterns, split patterns, and match-plate patterns, each serving different functional requirements based on the complexity of the part being cast.
2. Molds
The mold is the cavity into which molten metal is poured. In sand casting, molds are made from a mixture of sand and a binding agent, which could be clay or a synthetic resin. The mold consists of two halves the cope (upper half) and the drag (lower half). The pattern is placed inside this sand mixture, and once the sand is compacted around it, the pattern is removed, leaving a hollow cavity in the shape of the component. The quality of the sand and the compaction process significantly affects the surface finish and dimensional accuracy of the cast part.
3
. Sandparts of sand casting
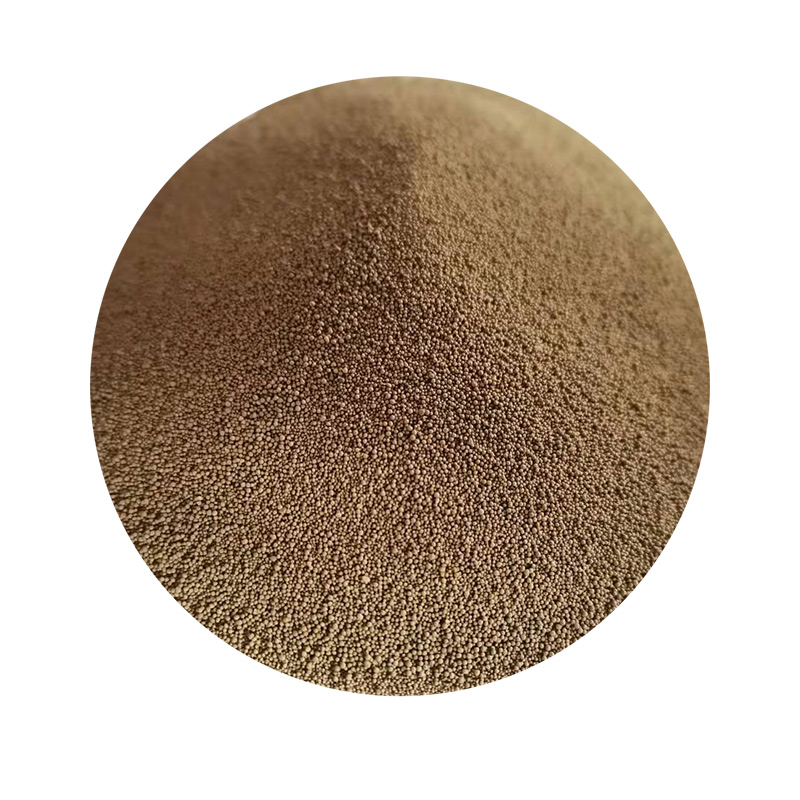
The type of sand used in sand casting plays a crucial role in the overall casting quality. The most common type is green sand, which is a mixture of silica sand, clay, and water. This mixture allows for a good balance of strength and flexibility, enabling it to retain the shape of the mold. Other types of sand, such as resin-bonded sand and zircon sand, are also used depending on the specific requirements of the casting, such as resistance to high temperatures or the need for superior surface finish.
4. Cores
Cores are additional components used to create internal cavities or complex geometries within the cast part. They are usually made from a mixture of sand and a binder, similar to the mold, and are placed inside the mold before pouring the metal. The cores must be designed to withstand the high temperatures of molten metal and to maintain their shape during the pouring process. Proper core design and placement are essential to ensure the finished part meets the required specifications.
5. Finishing Processes
Once the casting has cooled and solidified, it must undergo various finishing processes to achieve the desired quality. This may include sandblasting to remove residual sand, machining to achieve precise dimensions, and surface treatments to enhance corrosion resistance. Each of these processes helps improve the function and aesthetics of the final product.
Conclusion
In summary, the parts of sand casting—from patterns and molds to cores and finishing processes—work together to produce high-quality metal components. Understanding each component’s role and how they interact is essential for optimizing the sand casting process. As technology advances, innovations in materials and techniques continue to enhance the efficiency and capabilities of sand casting, making it an integral part of modern manufacturing.
Post time:നവം . 08, 2024 07:04
Next:Innovative Techniques in Lost Foam Sand Casting for Enhanced Precision and Efficiency