Molding Sand for Metal Casting An Essential Component in Foundry Processes
Molding sand is a crucial material in the foundry industry, serving as a medium for shaping molten metal into desired forms during the casting process. The properties and composition of molding sand significantly influence the quality of the final cast product, making it essential for foundries to select the right type of sand tailored to their specific casting needs.
Composition of Molding Sand
Molding sand is predominantly composed of three key components silica sand, clay, and water. Silica sand, the primary constituent, provides the necessary strength and structure to the mold. The most commonly used type of silica sand is quartz sand, which boasts high melting points and excellent thermal stability. The clay component, usually bentonite, acts as a binding agent, helping the sand particles stick together while maintaining the mold's integrity. Water is added to create a moist mixture, promoting cohesion among sand grains and enhancing workability.
Variations in the composition of molding sand can lead to diverse properties. For instance, the percentage of clay in the mixture can affect the sand's plasticity and how well it can retain its shape under the pressure of pouring molten metal. Consequently, foundries often experiment with different ratios to meet the specific requirements of a given casting operation.
Types of Molding Sand
There are several types of molding sand, each suited for different casting methods and metal products. The most common types include
1. Green Sand This sand contains a mixture of silica sand, clay, and water. Green sand molds are formed with the sand in its moist state, allowing for high strength and excellent compaction. Green sand is widely used in the production of ferrous castings due to its cost-effectiveness and ease of use.
molding sand for metal casting
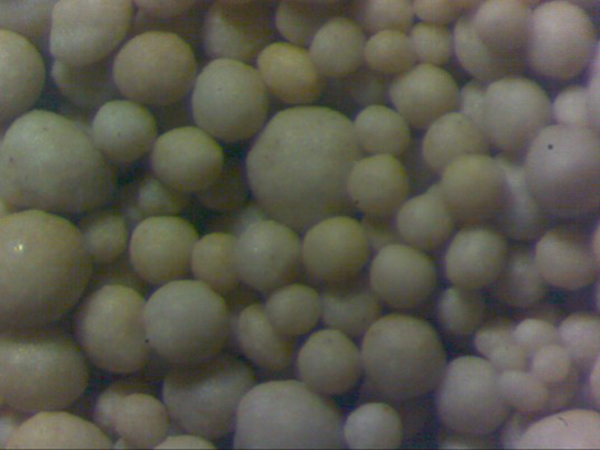
2. Dry Sand In contrast to green sand, dry sand molds are baked to eliminate moisture before pouring molten metal. This type of sand offers greater dimensional accuracy and surface finish, making it ideal for intricate designs and non-ferrous casting applications.
3. No-Bake Sand No-bake molding sands utilize a chemical binder instead of moisture to form molds. This allows for quicker production times as the molds can set at room temperature. No-bake sand is often used in industries requiring high precision and complex geometries.
4. Shell Molding Sand This type of sand consists of fine sand coated with a thermosetting resin. Shell molding is characterized by its ability to produce molds with outstanding surface finishes and dimensional accuracy, which is why it's commonly used for high-volume production of intricate castings.
Importance of Molding Sand Properties
The performance of molding sand is influenced by various properties, including permeability, cohesiveness, and thermal stability. Permeability refers to the sand's ability to allow gases to escape during the pouring of molten metal. Proper permeability is crucial to prevent defects like blowholes and inclusions in the final product. Cohesiveness determines how well the sand holds together under pressure, ensuring that the mold maintains its shape. Thermal stability is vital as the sand must withstand extreme temperatures without breaking down or collapsing.
Moreover, the ability of molding sand to support intricate designs without deforming is paramount in enhancing the quality of cast components. The right choice of sand can lead to improved surface finishes and reduced post-casting machining requirements, saving time and resources.
Conclusion
In summary, molding sand is an indispensable material in the metal casting industry, directly affecting the efficiency and quality of the casting process. Understanding the various types of molding sand and their specific properties allows foundries to optimize their operations and meet the diverse requirements of their customers. As technology advances, the development of new sand mixtures and binders continues to evolve, enhancing the capabilities of metal casting processes and ensuring high-quality products in various industrial applications.
Post time:നവം . 09, 2024 00:03
Next:Sustainable Solutions for Recycling Foundry Sand in Modern Manufacturing Processes