Lost Foam Sand Casting An Innovative Approach to Metal Casting
Lost foam sand casting is a modern and innovative method in the metal casting industry that offers several advantages over traditional casting techniques. This process combines the simplicity of traditional sand casting with the precision of more advanced methodologies, making it an attractive choice for many manufacturers. This article will elucidate the fundamentals of lost foam sand casting, its benefits, and its applications.
At its core, lost foam sand casting utilizes a foam pattern, typically made from expanded polystyrene, which is coated with a fine layer of sand. Unlike traditional sand casting where a solid mold is used, in lost foam casting, the foam pattern is placed directly into a sand mold. This sand mold is then compacted around the foam to achieve the desired shape and strength. Once the mold is prepared, molten metal is poured into it, which vaporizes the foam pattern and fills the cavity, resulting in a metal part that directly reflects the shape and features of the original foam pattern.
One of the primary advantages of lost foam sand casting is its ability to produce complex geometries with significant detail and high accuracy. The foam patterns can be designed using advanced CAD software, allowing for intricate designs that would be challenging to achieve with traditional methods. This capability reduces the need for extensive machining after the casting process, saving both time and resources.
Moreover, the lost foam process minimizes material waste. In traditional casting, adjusting the mold often requires additional materials, leading to higher waste levels. In lost foam casting, since the foam pattern is vaporized upon contact with molten metal, this leads to a more efficient use of raw materials. Additionally, the process allows for excellent surface finishes, which can further reduce the need for additional processing.
lost foam sand casting
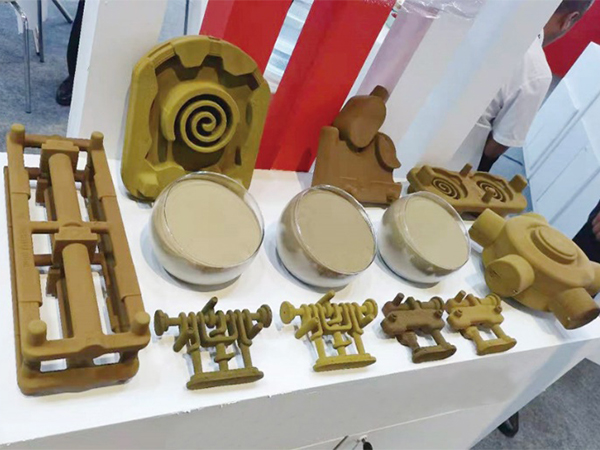
Another key benefit of lost foam sand casting is its versatility. The process can accommodate a wide variety of metals, including iron, aluminum, and zinc alloys. This flexibility makes it suitable for a range of industries, from automotive to aerospace, where components often demand precise tolerances and complex structures. This versatility is further enhanced by the ability to quickly adapt designs without significant delays in production time.
In terms of economic advantages, lost foam sand casting can prove to be cost-effective, especially for low to medium production runs. The elimination of manufacturing several hard molds can significantly reduce initial setup costs. Furthermore, the rapid prototyping capability inherent to this method allows companies to test and iterate designs quickly, bringing products to market faster.
However, the lost foam sand casting process is not without its challenges. Controlling the parameters of the casting operation is crucial, as factors such as temperature and pour rate can significantly impact the quality of the final product. Additionally, the availability and compatibility of foam patterns must be considered, as these can influence both the cost and feasibility of producing certain intricate designs.
In conclusion, lost foam sand casting represents a significant advancement in casting technology. By harnessing the advantages of foam patterns and combining them with traditional sand casting methods, manufacturers can achieve high-quality, complex metal parts with reduced waste and cost. As industries continue to seek innovative solutions for manufacturing challenges, lost foam sand casting stands out as a versatile and efficient approach that is likely to gain more prominence in the future.
Post time:ഡിസം . 11, 2024 05:15
Next:Best Places to Purchase Foundry Sand for Your Projects