Lost Foam Castings An Innovative Technique in Metalworking
Lost foam casting is a highly innovative and versatile metal casting process that has gained popularity in various industries due to its unique advantages over traditional methods. This technique, which allows for the production of complex shapes and high-precision components, involves the use of foam patterns that are vaporized during the casting process. This article delves into the intricacies of lost foam castings, its advantages, applications, and the underlying principles that make it a preferred choice in modern manufacturing.
The Process of Lost Foam Casting
The lost foam casting process begins with the creation of a pattern from polystyrene foam, which is intricately designed to match the final product's specifications. This foam pattern is then coated with a fine layer of refractory material to enhance its durability and create a mold-like structure. After being coated, the pattern is placed in a flask or mold, where it is surrounded by sand to help retain its shape during the casting process.
Once the flask is prepared, molten metal is poured directly onto the foam pattern. The heat from the molten metal causes the foam to vaporize, leaving behind a cavity that takes the exact shape of the foam pattern. This vaporization occurs almost instantaneously, leading to minimal disturbance of the sand mold. The result is a mold that can accurately replicate the intricate details of the foam pattern, allowing for precise and complex castings.
Advantages of Lost Foam Casting
One of the most significant advantages of lost foam casting is its ability to produce complex geometries that would be difficult or impossible to achieve with traditional casting methods. The foam patterns can be made in any shape, allowing for greater design flexibility and the potential for innovative product designs. This is particularly beneficial in industries such as automotive, aerospace, and art, where design complexity is often a critical factor.
lost foam castings
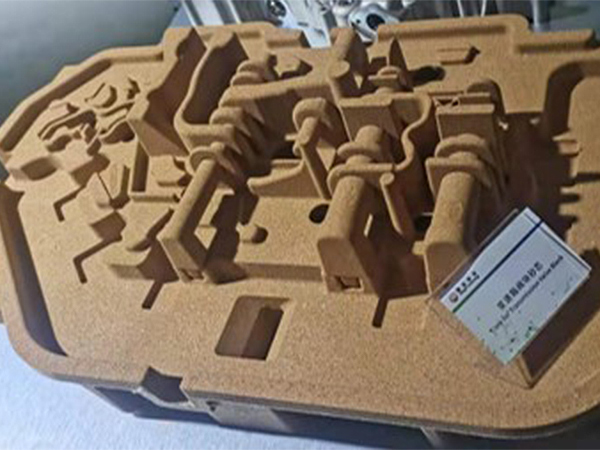
Another notable benefit of lost foam casting is the reduction of machining time and material waste. Traditional machining processes often require additional cutting and finishing to achieve the desired specifications. However, because lost foam castings can be produced with high accuracy, the need for extensive secondary operations is significantly diminished. This leads to cost savings and a more efficient manufacturing process.
Furthermore, lost foam casting is compatible with a wide range of metals, including aluminum, copper, and iron, making it a versatile option for various applications. The process also allows for the casting of thin-walled components, which is a vital requirement in industries that prioritize weight reduction without compromising structural integrity.
Applications of Lost Foam Casting
The applications of lost foam casting are vast and varied. In the automotive industry, lost foam casting is used to manufacture engine blocks, cylinder heads, and complex components that require high precision and durability. The aerospace sector also benefits from this technique, utilizing it to produce lightweight and intricate parts that are essential for aircraft performance.
Moreover, lost foam casting is gaining traction in the creation of artistic sculptures and intricate designs, allowing artists to bring their visions to life with precision. Additionally, this process is employed in manufacturing prototypes and small production runs, as it facilitates rapid development and iteration.
Conclusion
In conclusion, lost foam casting presents a remarkable advancement in metalworking that offers numerous benefits, including design flexibility, cost-effective production, and compatibility with various metals. Its ability to produce complex, high-precision components has made it a favored technique in multiple industries, from automotive to aerospace and beyond. As technology continues to evolve, lost foam casting is poised to play an increasingly significant role in the future of manufacturing, leading to further innovations and possibilities in metal casting. By embracing this technique, industries can meet the growing demands for more efficient, precise, and creatively designed products, making lost foam casting an essential part of the modern manufacturing landscape.
Post time:നവം . 09, 2024 08:14
Next:Creating Unique Designs with Super Sand G2 for Your Next Project