Lost Foam Casting Manufacturers A Comprehensive Overview
Lost foam casting is an advanced manufacturing process that offers unique advantages in producing complex metal parts with high precision. This innovative technique has gained traction across various industries, including automotive, aerospace, and industrial equipment, due to its capabilities to create intricate shapes and reduce waste. Understanding the landscape of lost foam casting manufacturers is crucial for businesses looking to leverage this technology.
What is Lost Foam Casting?
Lost foam casting (LFC) is a method where a foam pattern is used to create a mold for metal casting. The foam pattern, typically made from polystyrene, is coated with a fine layer of sand to create a shell. Once the sand mold is fabricated, the foam is vaporized by molten metal poured into the mold. This process allows for the production of parts with complex geometries and fine details that may be difficult to achieve through traditional casting methods.
Key Advantages of Lost Foam Casting
1. Complex Designs One of the most significant advantages of lost foam casting is its ability to produce parts with complex geometries. The foam patterns can be designed to have intricate details, allowing for better design flexibility.
2. Reduced Waste Traditional metal casting methods generate a considerable amount of waste due to the need for additional machining. In contrast, lost foam casting minimizes waste since the foam pattern is directly vaporized. The process also reduces the need for extra material, leading to more efficient production.
3. High Precision LFC provides superior dimensional accuracy compared to other casting methods. The process allows for tighter tolerances, which are critical for applications in the aerospace and automotive sectors.
4. Cost-Effective Although the initial investment in lost foam casting technology may be higher, the long-term cost efficiency is notable. The reduced waste, minimal tooling requirements, and quick production times contribute to lower overall costs.
5. Diverse Material Compatibility Lost foam casting can be used with a variety of metals, including aluminum, iron, and bronze. This versatility enables manufacturers to select the right material for specific applications.
The Role of Lost Foam Casting Manufacturers
Lost foam casting manufacturers are specialized companies that design and produce components using the LFC process. Their expertise spans several key areas
1. Pattern Design Manufacturers employ advanced software systems to develop intricate foam patterns tailored to the specific requirements of clients. This design phase is critical for ensuring the final product meets required specifications.
lost foam casting manufacturers
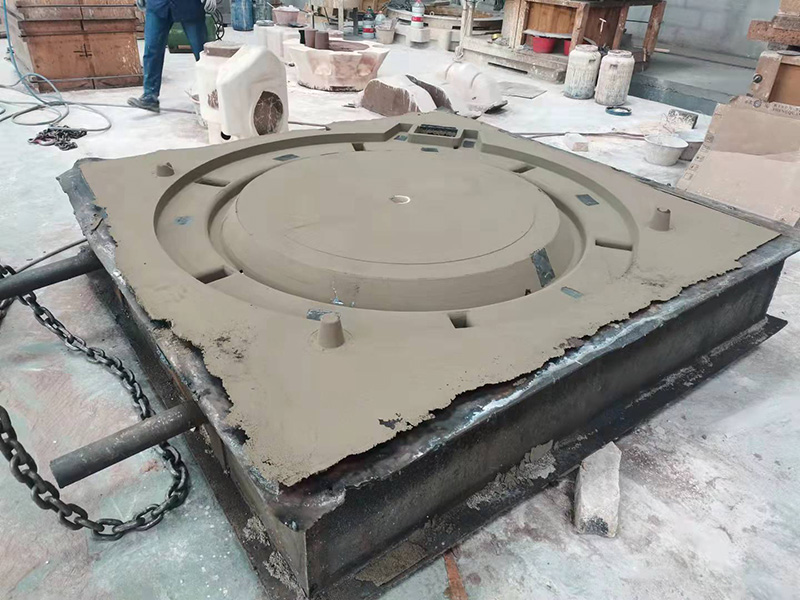
2. Mold Production Once the foam pattern is ready, manufacturers create sand molds. This step involves careful consideration of the mold design and material selection to ensure optimal results.
3. Casting Process The actual casting involves pouring molten metal into the mold and allowing it to solidify. Manufacturers monitor this stage closely to maintain quality control.
4. Finishing Often, parts require additional finishing processes, such as machining or coating, to meet industry standards and customer expectations.
5. Quality Control Leading manufacturers implement stringent quality control measures to ensure that every component meets the required tolerances and performance standards. This process often includes advanced testing and inspection techniques.
Choosing the Right Manufacturer
When selecting a lost foam casting manufacturer, several factors should be considered
1. Experience and Expertise Look for manufacturers with a proven track record in lost foam casting and experience in your specific industry.
2. Technology and Equipment Ensure the manufacturer employs advanced technology and equipment to achieve high precision and quality in their casting processes.
3. Custom Solutions Choose manufacturers that offer customized solutions tailored to your specific needs, demonstrating their ability to handle diverse projects.
4. Sustainability Practices With a growing focus on sustainability, it’s essential to consider manufacturers that prioritize eco-friendly practices and materials.
5. Customer Support A responsive and knowledgeable customer service team can help facilitate smooth communication and project management.
Conclusion
As industries continue to evolve, the importance of advanced manufacturing techniques like lost foam casting cannot be overstated. Manufacturers specializing in this process play a critical role in ensuring high-quality production of complex components. By understanding the advantages of lost foam casting and selecting the right manufacturer, businesses can harness this innovative technology to improve their production capabilities and meet the demands of the modern marketplace.
Post time:നവം . 21, 2024 00:02
Next:buy sand casting