Is Sand Casting Sustainable?
Sand casting has long been a foundational manufacturing process used for producing metal components. Its versatility, cost-effectiveness, and ability to create complex shapes make it a popular choice across various industries, including automotive, aerospace, and artistic applications. However, in an era where sustainability is a major focus, it's essential to evaluate the environmental implications of sand casting and whether it can be considered a sustainable manufacturing technique.
Understanding Sand Casting
Sand casting involves creating a mold from a sand mixture, into which molten metal is poured. The sand is typically combined with a binding agent, and once the metal solidifies, the mold is broken away to reveal the finished component. While the sand used in this process is often silica-based, the materials can be recycled and reused, which is one aspect of its sustainability profile.
Environmental Impact
One of the key factors influencing the sustainability of sand casting is its environmental impact. Traditional sand casting relies significantly on natural resources, including silica sand, which is mined from the earth. The extraction and processing of silica sand can lead to habitat destruction and increase carbon emissions. Moreover, the use of energy-intensive processes for melting metal and the release of pollutants during these operations raise additional concerns.
However, there are positive developments in the sand casting industry that contribute to its sustainability. Many foundries are adopting more eco-friendly practices, such as using reclaimed sand, which diminishes the need for new raw materials. The recycling of sand can significantly reduce the volume of waste produced and minimize the environmental footprint associated with mining activities.
Innovations and Alternatives
is sand casting sustainable
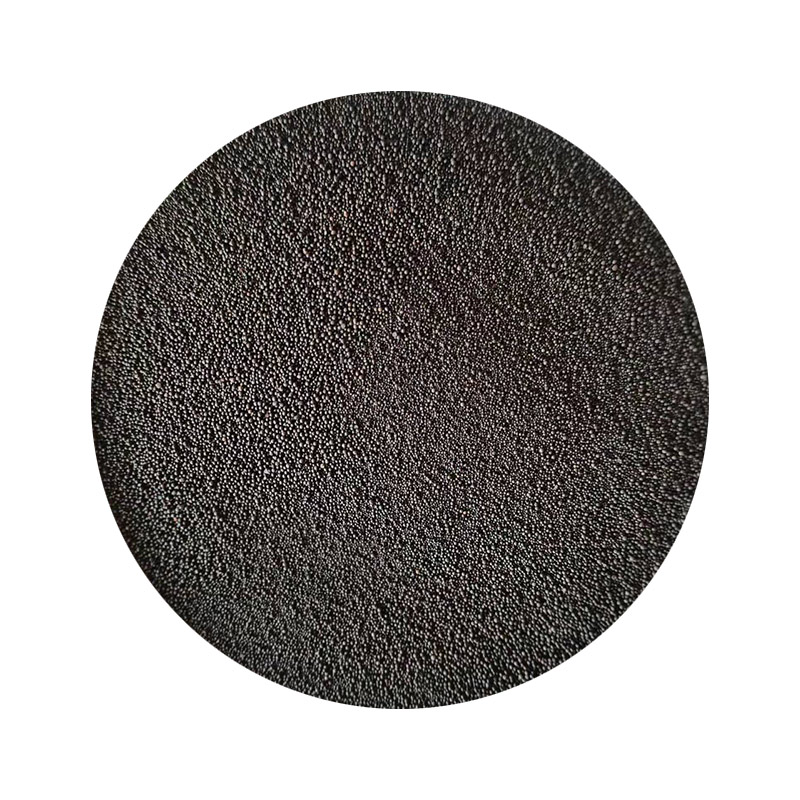
In recent years, innovations in materials and processes have further enhanced the sustainability of sand casting. The introduction of polymer-bonded sands as alternatives to traditional clay-bonded sands offers a much lower environmental impact. These polymers can be more easily recycled and reused, leading to less waste and decreased resource consumption.
Moreover, emerging technologies such as 3D printing are beginning to intersect with sand casting. 3D printing can create complex mold geometries with greater precision, reducing material waste and energy consumption. This synergy between traditional sand casting and modern technologies presents an exciting avenue for improving sustainability.
Life Cycle Assessment
A comprehensive analysis of sand casting's sustainability necessitates a life cycle assessment (LCA) approach. This involves examining each stage of the product’s life, from raw material extraction through production, use, and disposal. Many foundries are now beginning to implement LCAs to evaluate and optimize their processes, focusing on reducing life cycle emissions and material usage. The LCA approach helps identify areas where sand casting can become more efficient and environmentally friendly.
Conclusion
While traditional sand casting has a range of sustainability challenges, ongoing advancements and shifts in practices present opportunities for improvement. The ability to recycle materials, the use of innovative alternatives, and the integration of modern technologies are all contributing to a more sustainable approach to sand casting.
The industry is in a phase of transformation, continually seeking to balance the demand for quality products with the necessity of environmental stewardship. As consumers and businesses alike continue to prioritize sustainability, it is crucial for the sand casting industry to adapt and evolve, ensuring that its practices meet modern standards of environmental responsibility.
Ultimately, while sand casting is not without its environmental challenges, through innovation, recycling, and improved practices, it can move towards a more sustainable future. The key lies in harnessing these advancements to minimize the ecological footprint while meeting the demand for quality metal components in an ever-evolving marketplace.
Post time:നവം . 09, 2024 09:02
Next:Different Types and Techniques of Sand Casting Processes Explained