How to Sand Cast A Step-by-Step Guide
Sand casting is one of the oldest and most widely used metal casting processes. This technique is favored for its versatility, cost-effectiveness, and ability to produce complex shapes. Whether you’re a hobbyist looking to create a simple casting or a professional looking to make high-quality parts, understanding the sand casting process is crucial. In this article, we will guide you through the essential steps of sand casting, ensuring you have a clear understanding of how to execute this method.
Step 1 Prepare the Pattern
The first step in the sand casting process is to create a pattern, which is a replica of the object you want to cast. Patterns can be made from various materials, including wood, metal, or plastic. The choice of material largely depends on factors such as the complexity of the shape and the number of casts required. The pattern should include some allowances for shrinkage and finishing. Typically, a 10% allowance for shrinkage is common as metals contract upon cooling.
Step 2 Create the Sand Mold
The next step is to make the mold using sand mixture. The ideal sand for casting is usually a combination of silica sand, clay, and water. The mixture promotes good packing and allows for the fine detail of the pattern to be captured. To create the mold, place the pattern in a mold box and pack the sand around it. It’s important to firmly pack the sand to prevent any defects during pouring. Once the pattern is embedded, the mold can be split to remove the pattern, creating an impression.
Step 3 Prepare for Pouring
Once your mold is ready, the next step is to prepare for pouring the molten metal. Ensure that the mold is clean and free of debris. If necessary, a release agent can be applied to minimize molding sand sticking to the cast. The pouring basin and sprue (the channel that allows metal to flow into the mold) should be created at the top of the mold to facilitate an easy and controlled pour of molten metal.
Step 4 Melt the Metal
how to sand cast
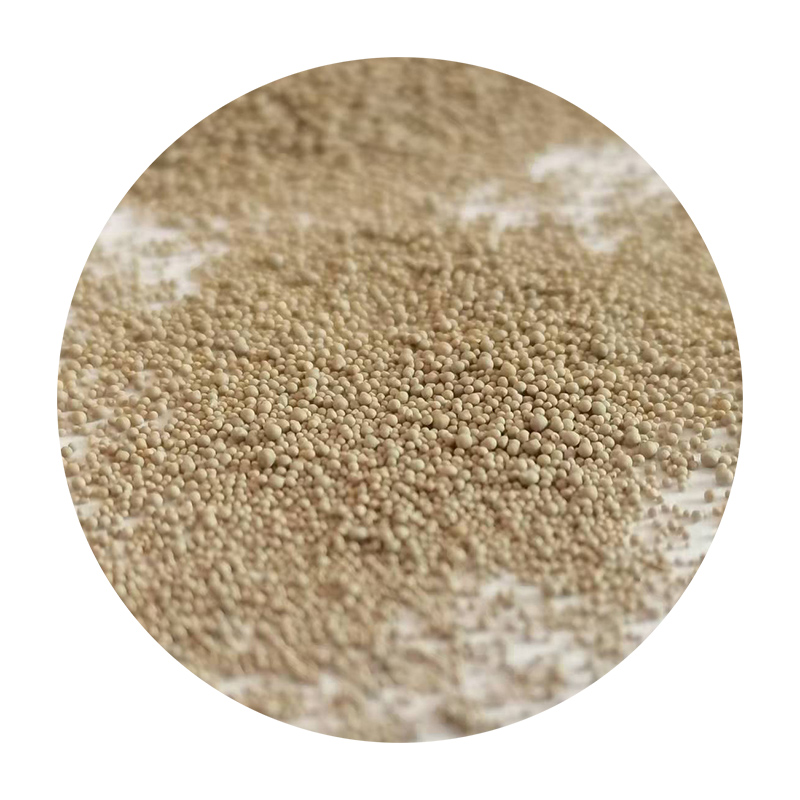
With the mold prepared, it’s time to melt the metal. This can be done using a furnace, a forge, or other suitable equipment, depending on the type and quantity of metal being used. Common metals for sand casting include aluminum, bronze, and iron. The metal should be heated until it reaches a liquid state and poured into the pouring basin.
Step 5 Pour the Metal
With the metal melted, carefully pour it into the mold through the pouring basin. It’s important to maintain a steady, controlled pour to prevent air entrapment and ensure that the mold fills completely. Allow the metal to fill the mold cavity, filling all corners and ensuring a complete cast.
Step 6 Cool and Remove the Casting
Once the metal has been poured, it needs time to cool and solidify. Cooling times will vary based on the type of metal and the thickness of the cast. After cooling, carefully break open the sand mold to remove the casting. Be gentle to avoid damaging the finished product.
Step 7 Finishing Touches
Finally, after removing the casting from the mold, you may need to perform some finishing processes, such as sanding, grinding, or machining, to achieve the desired surface finish and dimensions.
With these steps, you now have a basic understanding of how to sand cast. This ancient technique remains popular in modern manufacturing and can yield impressive results with practice and attention to detail. Whether you are creating artistic pieces or functional components, sand casting is a rewarding process that allows for creativity and craftsmanship. Happy casting!
Post time:സെപ് . 04, 2024 04:27
Next:foundry sands