Understanding Foundry Sand Types An Essential Guide for Foundry Operations
Foundry sand is a crucial component in metal casting processes, serving as a mold material to shape molten metal into desired forms. The right type of foundry sand can significantly influence the quality of the final product, production efficiency, and operational costs. In this article, we will explore various types of foundry sand, their characteristics, and their applications in different foundry operations.
1. Silica Sand
Silica sand, predominantly composed of quartz, is the most commonly used foundry sand. Its high melting point, durability, and excellent flowability make it suitable for a wide range of casting processes. Silica sand can withstand the thermal and mechanical stresses encountered during the casting process, ensuring a high-quality mold. It is typically used in green sand casting, where moisture is added to the sand to help it retain shape and form.
One of the key advantages of silica sand is its availability and cost-effectiveness. However, its primary drawback is the health risk associated with inhaling silica dust, which can lead to respiratory issues. As a result, many foundries have started to incorporate safety measures and explore alternative materials.
2. Resin-Coated Sand
Resin-coated sand, also known as chemically bonded sand, is silica sand that has been coated with a resin binder. This type of sand provides improved strength and resistance to thermal degradation compared to traditional silica sand. The resin binds the sand grains together, allowing for finer molds that can capture intricate details in the casting process.
Resin-coated sand is often used in precision casting applications, such as aerospace and automotive industries, where high dimensional tolerance and surface finish are critical. However, this type of sand tends to be more expensive and may require additional handling and curing processes.
foundry sand types
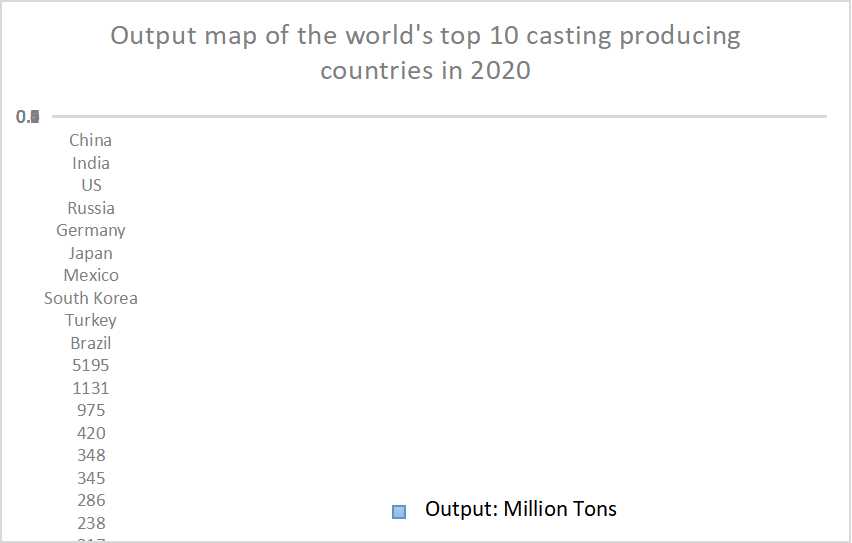
Clay-based sand, particularly green sand, is a mixture of sand, clay, and water. The clay present in the sand acts as a binder, providing the necessary cohesion and plasticity to form molds. This type of sand is favored for its ability to retain moisture and shape, making it ideal for large-scale casting operations.
Green sand is relatively inexpensive and easy to work with, making it popular for production foundries. However, it does have limitations in terms of surface finish and precision compared to resin-coated or investment casting methods.
4. Chromite Sand
Chromite sand is a premium type of foundry sand derived from chromite ore. It is known for its high thermal conductivity, excellent strength, and resistance to thermal shock. These properties make chromite sand particularly suitable for demanding casting applications, such as those involving ferrous and non-ferrous metals.
Additionally, chromite sand is less prone to fusion and allows for cleaner cast surfaces, reducing the need for extensive finishing processes. However, the cost of chromite sand is significantly higher, which can impact the overall production budget.
5. Other Specialty Sands
In addition to the commonly used sands mentioned above, there are various specialty sands that serve specific purposes. For instance, zircon sand is utilized for its high refractoriness and low thermal expansion, making it ideal for precision castings. Olivine sand, known for its green color, offers good flowability and is used in both ferrous and non-ferrous casting.
Conclusion
Choosing the right type of foundry sand is essential for achieving optimal casting results. Each sand type has its unique characteristics, advantages, and applications, which can influence the efficiency and quality of the foundry operations. As foundry technology advances and environmental concerns mount, foundry operators must remain informed about the various sand options available and consider factors such as cost, health impacts, and performance to make informed decisions. By selecting the appropriate foundry sand, manufacturers can enhance their production capabilities and ensure high-quality castings meet industry standards.
Post time:ഡിസം . 22, 2024 14:46
Next:super sand bond