Understanding Foundry Sand Definition and Importance
Foundry sand plays a crucial role in the metal casting process, serving as a primary medium for creating molds and cores that shape molten metal into desired forms. It is a high-purity, high-quality sand primarily composed of silica, with a fine granular texture that enables it to be easily shaped and compacted. This article will delve into the definition of foundry sand, its key characteristics, types, applications, and its significance in the manufacturing sector.
Definition of Foundry Sand
Foundry sand is defined as a suitable material used in the metal casting industry to form molds and cores. It is typically derived from high-quality silica sand and is characterized by its ability to withstand high temperatures, provide excellent collapsibility after casting, and enable fine detailing in molds. The primary function of foundry sand is to provide a strong, stable support for the molten metal while allowing it to be shaped as per the specifications of the desired product.
Characteristics of Foundry Sand
The qualities of foundry sand are what set it apart from other types of sand used in construction and landscaping. Some of the critical characteristics include
1. High Purity Foundry sand is expected to have a low clay content. The presence of impurities or contaminants can affect mold integrity and ultimately the quality of the cast product. 2. Grain Shape The shape of sand grains can significantly influence the mold’s mechanical properties. Foundry sand is usually sub-angular to rounded, allowing easy compaction and minimal void space.
3. Thermal Stability It must withstand elevated temperatures without degrading, which is vital during the pouring of molten metal.
4. Cohesion and Adhesion Foundry sand's ability to hold together (cohesion) and adhere to the surface of the mold (adhesion) is essential for creating accurate and precise cast shapes.
5. Reusability After the casting process, many types of foundry sand can be reclaimed and reused, making it a cost-effective and environmentally friendly choice.
Types of Foundry Sand
foundry sand definition
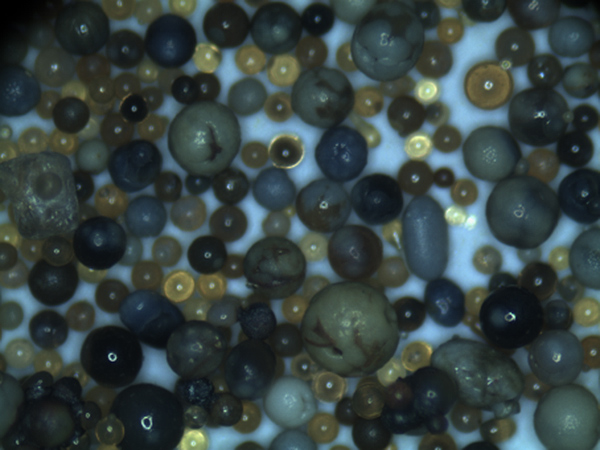
There are several types of foundry sand, each suited to specific applications
1. Silica Sand This is the most common type of foundry sand, particularly used for ferrous and non-ferrous metals owing to its availability and excellent thermal properties.
2. Chromite Sand Used mainly for high-performance applications, chromite sand has a higher melting point and is typically used in steel casting.
3. Zircon Sand It is utilized for producing high-quality castings, particularly for non-ferrous materials, and has excellent thermal stability and resistance to thermal shock.
4. Olive Sand While less common, it has excellent casting properties and can be used in specific applications where its unique qualities are beneficial.
Applications of Foundry Sand
The applications of foundry sand span across various industries primarily focused on metal casting. Key sectors include automotive, aerospace, construction, and machinery manufacturing. It is widely used to produce engine blocks, transmission cases, and other intricate components that require high precision and durability.
Significance of Foundry Sand in Manufacturing
The importance of foundry sand in the manufacturing process cannot be overstated. It not only contributes to the quality of the cast products but also impacts the efficiency of the casting operations. High-quality foundry sand minimizes defects such as gas porosity or inclusions, reducing material waste and enhancing product quality. Additionally, its reusability aligns with sustainable manufacturing practices, making it a vital component in both traditional and innovative metal casting technologies.
In conclusion, foundry sand is an indispensable material in the metal casting industry, defined by its unique characteristics and essential roles in the manufacturing process. As industries continue to advance, the demand for high-quality foundry sand will likely remain significant, ensuring that it will play a critical role in producing precision metal components for various applications.
Post time:ഡിസം . 02, 2024 04:07
Next:Sabbiatura per fusione Guida ai materiali e tecniche migliori