Difference Between Sand Casting and Die Casting
When it comes to metal casting processes, two of the most common methods are sand casting and die casting. Both techniques have their unique advantages and disadvantages, making them suitable for different applications. Understanding the fundamental differences between these two processes can help manufacturers choose the right method for their specific needs.
Overview of Sand Casting
Sand casting is one of the oldest and most widely used metal casting processes. In this method, a mold is created using a mixture of sand, clay, and water. The sand is packed around a pattern of the desired object, creating a cavity. Once the mold is formed, the pattern is removed, and molten metal is poured into the cavity. After the metal cools and solidifies, the mold is broken away to reveal the finished part.
Overview of Die Casting
Die casting, on the other hand, involves forcing molten metal into a steel mold (or die) under high pressure. The molds are typically made from two halves that form the desired shape once joined. This method is mainly used for non-ferrous metals such as aluminum, zinc, and magnesium. After the metal is injected, the mold is cooled quickly, allowing for fast production cycles and precise component dimensions.
Key Differences
1. Material Used One of the primary differences between sand casting and die casting is the type of metals that can be utilized. Sand casting can accommodate a wide variety of metals including cast iron, aluminum, and bronze. In contrast, die casting is usually limited to non-ferrous metals like aluminum and zinc.
difference between sand casting and die casting
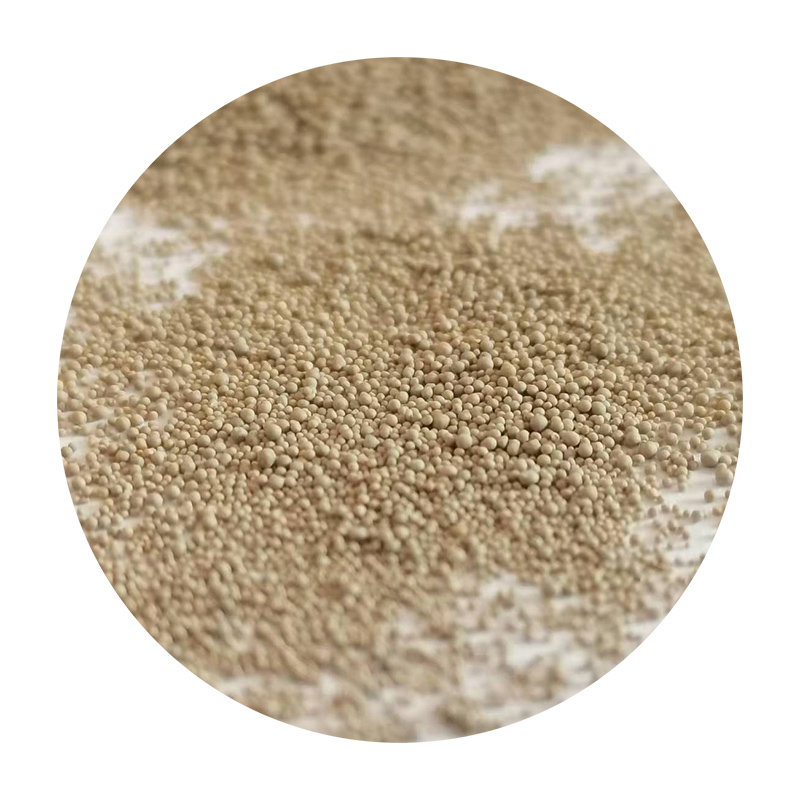
2. Mold Composition The molds used in these casting methods vary significantly. Sand casting molds are made from sand, while die casting relies on steel molds that are very durable and can withstand high pressures. This difference in material affects the cost and longevity of the molds; sand molds are cheaper but have a limited lifespan, while die cast molds are more expensive but can produce thousands of parts before they wear out.
3. Production Volume Die casting is ideal for high-volume production runs due to its efficiency and speed. Once the die is created, parts can be produced rapidly, making this method suitable for items that require precision and consistency. Sand casting, however, is better suited for low to medium production volumes, especially when large and complex shapes are involved.
4. Surface Finish and Tolerances Die casting generally provides superior surface finishes and tighter tolerances compared to sand casting. The high pressure used in die casting allows for finer details to be captured, whereas sand casting may result in a rougher finish and less precise dimensions due to the inherent nature of the mold material.
5. Cost Considerations The initial setup cost for die casting is significantly higher than that of sand casting due to the expense of creating metal dies. However, the overall cost per unit decreases with higher production volumes because of the efficiency of the process. Conversely, sand casting may result in lower upfront costs but is less economical for mass production.
6. Flexibility Sand casting offers greater design flexibility, especially for larger and more complex parts. Changes to the part design can often be made by creating a new pattern without the need for new molds. In contrast, altering a die casting mold can be more complicated and costly, making die casting less adaptable to changes in design.
Conclusion
Both sand casting and die casting have distinct characteristics that make them ideal for different applications. Sand casting is more flexible and versatile for a range of metals and part complexities, while die casting excels in high-speed production with tighter tolerances and better surface finishes. When choosing between these two methods, manufacturers must consider factors such as production volume, material type, cost implications, and specific project requirements to select the most appropriate casting process for their needs.
Post time:ഡിസം . 05, 2024 17:54
Next:Innovative Techniques in 3D Printing with Sand for Construction and Design Applications