The Sand Casting Process An Overview
Sand casting, one of the oldest and most versatile manufacturing processes, has been widely employed to produce a variety of metal components. Its simplicity, cost-effectiveness, and ability to cater to complex geometries make it a favored choice in industries such as automotive, aerospace, and general engineering. This article delves into the intricacies of the sand casting process, highlighting its steps, materials, advantages, and applications.
The Basics of Sand Casting
At its core, sand casting involves creating a mold for metal pouring using sand and a binder. The process begins with the preparation of a pattern, which is a replica of the desired final product. Patterns can be made from various materials, including metal, plastic, or wood, depending on the requirements of the component and the casting process.
Once the pattern is prepared, a mold is created from a mixture of sand and a binding agent. This mixture, known as sand mold, is packed tightly around the pattern. The key to a successful mold lies in the quality of the sand and the binder, which ensure that the mold retains its shape and can withstand the molten metal's heat.
Steps in the Sand Casting Process
1. Pattern Making The first step involves designing and making a pattern that reflects the final part’s geometry. A pattern may require allowances for shrinkage and machining.
2. Mold Preparation The chosen sand is mixed with a binder, like clay or resin, to form a mold that can be shaped around the pattern. The mixture is packed around the pattern and then carefully removed to leave a cavity.
3. Core Making If the part design includes internal cavities or complex geometries, cores made from sand are created. These cores are placed in the mold before pouring.
4. Mold Assembly Once the mold halves are prepared, they are assembled, and the cores are positioned inside as necessary. Care is taken to ensure proper alignment and sealing to avoid leaks during pouring.
5. Metal Pouring The mold is then heated to remove moisture before molten metal is poured in. The temperature of the molten metal must be controlled carefully to ensure optimal flow and to prevent defects.
6. Cooling After pouring, the metal is allowed to cool and solidify while remaining in the mold. Cooling times can vary depending on the metal type and the complexity of the design.
describe sand casting process
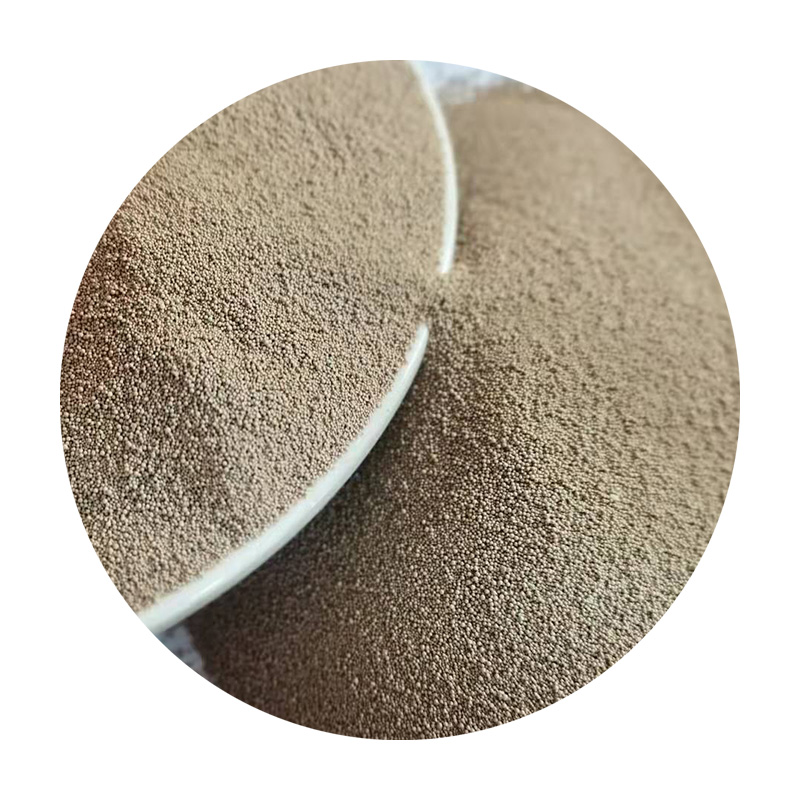
7. Mold Removal Once solidified and cooled, the mold is broken away to reveal the cast part. This is often done mechanically or manually, depending on the design and size of the component.
8. Finishing The final step involves cleaning the cast part to remove any sand, sharp edges, or irregularities, followed by any necessary machining processes to achieve the final specifications.
Advantages of Sand Casting
The sand casting process offers several advantages that make it appealing across various sectors
- Cost-Effective The materials used, primarily sand and binders, are relatively inexpensive, making sand casting a cost-effective choice for both large and small production runs. - Versatility Sand casting can accommodate a range of metal types, including aluminum, iron, and bronze, making it suitable for various applications.
- Complex Geometries The process allows for intricate designs and complex shapes that might be challenging to achieve with other manufacturing methods.
- Scalability From one-off prototypes to high-volume production, sand casting can scale according to demand without significant investment in tooling.
Applications
Sand casting is utilized in numerous industries. It produces components like engine blocks, housings, and intricate parts for machinery. In the automotive industry, it plays a crucial role in the manufacture of critical engine parts due to its ability to produce durable and lightweight components. In aerospace, sand casting is used for both structural and engine parts, highlighting its adaptability and importance.
Conclusion
In summary, sand casting is a vital manufacturing process that combines simplicity with versatility. Understanding its steps, advantages, and applications can provide valuable insights into its role in modern manufacturing. As technology evolves, sand casting continues to innovate, reinforcing its place in the industry as a reliable method for producing high-quality metal components.
Post time:നവം . 12, 2024 12:46
Next:gold sands