Components of Sand Casting An In-Depth Look
Sand casting, also known as sand molded casting, is one of the oldest and most versatile casting processes in metalworking. It involves creating a mold out of sand, into which molten metal is poured to form a specific shape once it cools and solidifies. This method is popular for producing intricate designs and large parts, making it a preferred choice in various industries, including automotive, aerospace, and art.
1. The Sand Mixture
The primary component of sand casting is the sand itself, which is typically composed of silica (silicon dioxide) due to its high melting point and excellent thermal properties. The sand must possess certain characteristics to be effective in the casting process
- Grain Size The size of the sand grains affects the mold's surface finish. Finer grain sands produce a smoother surface but may have lower strength, while coarser sands provide greater strength but can lead to a rougher finish.
- Composition In addition to silica, other materials like clay, water, and additives are often mixed with sand to enhance its binding properties. Clay serves as a binder, helping the sand grains stick together, while water acts as a lubricant to facilitate shaping and compaction.
2. Mold Creation
Once the sand mixture is ready, the next step involves creating the mold. This process typically includes the following components
- Pattern A pattern is a replica of the final product that will be cast. Patterns are usually made from metals, plastic, or wood. The choice of material often depends on the required precision, durability, and the number of castings needed. Patterns can be split into two halves to create a core, necessary for hollow parts.
- Molding Box The pattern is placed in a molding box, which is a frame that holds the sand mixture. The molding box is filled with the sand mixture, and special techniques are applied to compact the sand around the pattern.
- Vent and pour holes During the mold-making process, vents are created to allow gases escape when the molten metal is poured and starts to fill the mold. Pouring holes are also incorporated, enabling the metal to enter the mold cavity without obstruction.
components of sand casting
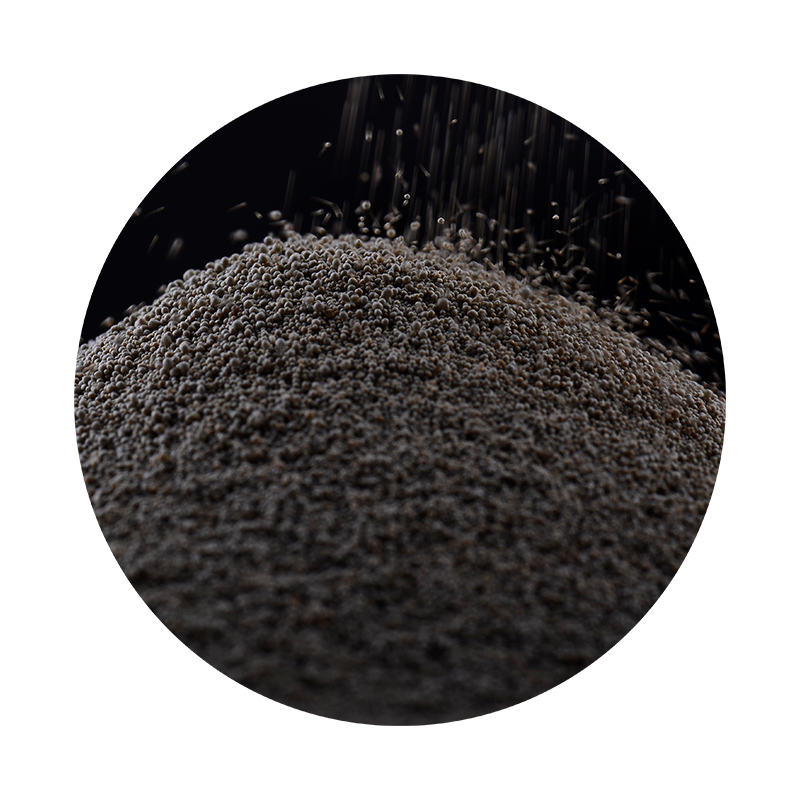
3. Core Making
For complex shapes that have internal cavities, cores are used. Cores are additional sand forms placed inside the mold. They are made separately and typically use similar materials to those used for creating the molds themselves. Cores can be made of sand mixed with binders, and they are crucial in casting components like engine blocks, where internal channels need to be formed.
4. Melting and Pouring
Following the preparation of the mold and cores, the next step is melting the metal. The type of metal used often determines the melting process. Common metals in sand casting include aluminum, brass, and iron. The molten metal is poured into the mold through the pouring hole, filling the cavity and the space surrounding the core if applicable.
5. Cooling and Solidification
Once the molten metal is poured, it requires time to cool and solidify. The cooling time varies depending on the size and thickness of the casting. Cooling too quickly can induce stress and lead to defects, so careful monitoring is essential to ensure the structural integrity of the final product.
6. Finishing and Quality Control
After the metal has solidified, the mold is broken apart, and the casting is removed. The casting often requires some finishing processes to achieve the desired dimensions and surface quality. Techniques may include grinding, sandblasting, or machining.
Quality control plays a vital role throughout the sand casting process. Regular inspections ensure that the molds are correctly formed, the metal is clean and free of impurities, and the final product meets the required specifications.
Conclusion
In summary, the components of sand casting play a crucial role in the overall success of the casting process. From the careful selection of the sand mixture to the meticulous design of the mold, each step is essential in achieving a high-quality final product. Sand casting is a blend of art and science, where the understanding of materials and processes leads to the creation of durable and complex metal parts that serve various industrial applications. As technology progresses, innovations in materials and processes continue to enhance the capabilities and efficiency of sand casting, ensuring its relevance in modern manufacturing.
Post time:നവം . 12, 2024 11:18
Next:what to sand resin with