3D Printing in Sand Casting Revolutionizing Manufacturing
The manufacturing industry has always been at the forefront of innovation, and the advent of 3D printing has redefined traditional processes across various sectors. Among these, sand casting—a time-honored method for creating metal parts—has seen remarkable transformations through the integration of 3D printing technology. This fusion not only optimizes manufacturing efficiency but also enhances the precision and capabilities of sand casting.
Sand casting is a process that involves creating a mold by compacting sand around a pattern, usually made from metal, wood, or plastic. Once the mold is formed, molten metal is poured into it to create the desired shape. Traditionally, this method has been labor-intensive and time-consuming, often requiring multiple steps of mold creation, pattern making, and finishing. However, the introduction of 3D printing into the sand casting process has streamlined these steps, leading to a more efficient manufacturing workflow.
3D Printing in Sand Casting Revolutionizing Manufacturing
Moreover, the process of 3D printing sand molds or cores presents benefits in terms of lead time reduction. Traditional mold-making can take weeks, as it involves manual labor and several iterations. In contrast, using 3D printing technology can cut this time down to a matter of days, significantly speeding up the process from design to finished product. This rapid prototyping is particularly advantageous in industries where time-to-market is crucial, such as aerospace and automotive sectors.
3d printing sand casting
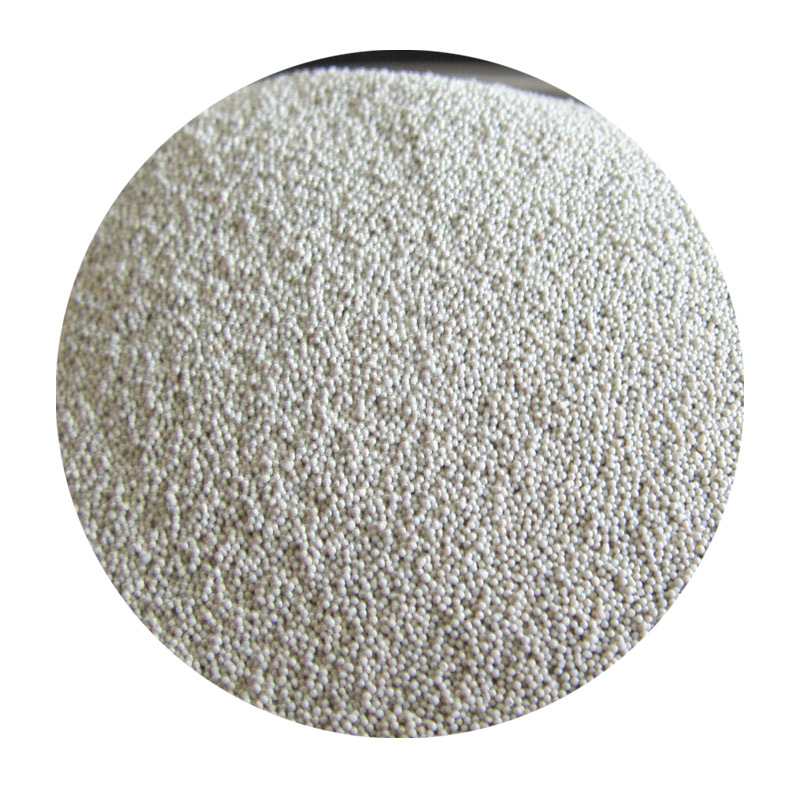
The accuracy of 3D printed sand molds also plays a pivotal role in enhancing the overall quality of cast parts. Conventional sand casting often faces issues related to dimensional tolerances and surface finishes. However, 3D printing can achieve tighter tolerances and smoother surfaces, which results in fewer defects and reduced needs for post-processing work. This high level of precision not only minimizes material waste but also lowers production costs, further improving the economic viability of using 3D printing in sand casting.
Additionally, the environmental impact of manufacturing processes is becoming increasingly important in today’s world. The use of 3D printing in sand casting can contribute to sustainability efforts. For instance, 3D printed molds typically require less material compared to traditional molds, and many 3D printing processes utilize recyclable and environmentally friendly materials. This reduction in material consumption can lead to lower energy usage and a smaller carbon footprint, aligning with global efforts to decrease environmental degradation.
However, while the benefits of integrating 3D printing with sand casting are considerable, there are challenges to overcome. One such challenge is the need for advanced materials that can withstand the high temperatures of molten metal while maintaining structural integrity during the casting process. Additionally, manufacturers must invest in training and adapting their workforce to work with new technologies, which can be a barrier for some companies.
In conclusion, the integration of 3D printing into sand casting offers compelling advantages, including increased design freedom, reduced lead times, improved accuracy, and enhanced sustainability. As technology continues to advance, the manufacturing landscape will undoubtedly continue to evolve, making traditional methods more efficient and environmentally friendly. The future of sand casting, powered by 3D printing, promises to reshape the way manufacturers approach production, paving the way for innovative solutions in a wide range of industries.
Post time:ഡിസം . 05, 2024 02:13
Next:foundry sand specifications