What is Sand Casting?
Sand casting is one of the oldest and most widely used metal casting processes that plays a pivotal role in various manufacturing industries today. Its popularity stems from its versatility, cost-effectiveness, and suitability for both large-scale production and custom parts. Understanding the sand casting process involves reviewing its definition, components, methodology, advantages, and applications.
At its core, sand casting is a method of creating metal parts by pouring molten metal into a mold made from sand. This process allows for the production of complex shapes and intricate designs that would be difficult or impossible to achieve with other methods. The sand used in the process is typically a mixture of silica sand, clay, and water, which provides the necessary strength and cohesion to hold the mold's shape.
Components of Sand Casting
The key components of sand casting include the pattern, mold, core, and the metal being cast. The pattern is a replica of the object to be produced and can be made from various materials, including wood, metal, or plastic. Patterns are often designed with slight allowances for shrinkage and to facilitate easier removal from the mold.
The mold, made from the sand mixture, is formed around the pattern. Once the pattern is placed in the molding box, sand is packed around it, and then the pattern is removed, leaving a mold cavity. In some cases, a core is inserted into the mold to form internal cavities or features within the final product.
Once the mold is prepared, molten metal, typically aluminum, iron, or bronze, is poured into the cavity of the mold. The liquid metal fills the space, taking the shape of the mold as it cools and solidifies.
what is a sand casting
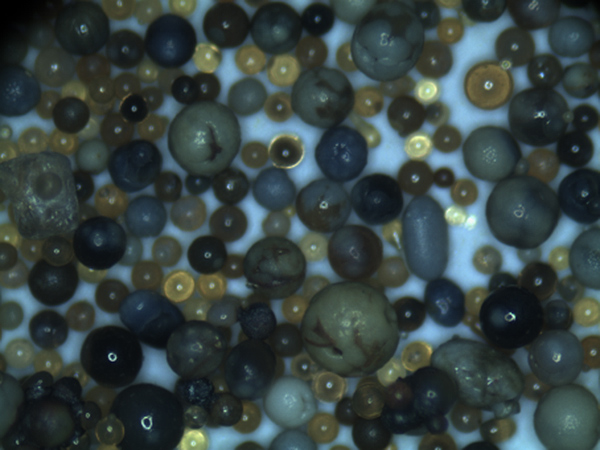
Advantages of Sand Casting
One of the primary reasons for the widespread use of sand casting is its flexibility. It can accommodate a variety of metals and alloy compositions, making it suitable for producing parts in different industries, such as automotive, aerospace, and heavy machinery. The process is also relatively inexpensive, as the materials required—sand, binders, and metal—are commonly available.
Furthermore, sand casting allows for high production volumes and can produce very large parts when traditional methods may not be feasible. Another significant advantage is the ease of creating complex shapes and features, providing designers with more creative freedom.
Applications of Sand Casting
Sand casting is utilized in numerous applications across multiple industries. In the automotive sector, components such as engine blocks, cylinder heads, and transmission cases are often produced using this method. The aerospace industry also benefits from sand casting for producing lightweight, durable parts that can withstand extreme conditions. Other applications can be found in the manufacturing of construction equipment, agricultural machinery, and art sculptures.
In summary, sand casting is a fundamental process in the realm of manufacturing that combines artistic design with engineering precision. Its versatility, cost-effectiveness, and capability to produce complex parts have ensured its continued relevance in modern production techniques. Whether it is for a unique custom project or mass production, sand casting remains a vital tool in the creation of metal components.
Post time:Окт . 02, 2024 03:15
Next:Exploring the Art and Techniques of Sand Casting in Metalworking