Wet Sanding Resin A Comprehensive Guide for a Flawless Finish
Wet sanding resin is a crucial technique in the world of woodworking, automotive refinishing, and epoxy resin applications. This method enhances the finish quality of resin products, ensuring a smooth, glossy surface free of imperfections. While it might seem overwhelming at first, understanding the basics of wet sanding resin and mastering the technique can yield stunning results. In this article, we will delve into what wet sanding is, why it’s beneficial, and how to effectively execute the process.
What is Wet Sanding?
Wet sanding involves using water as a lubricant while sanding a surface. This technique is particularly beneficial when working with resin because it minimizes dust production, reduces heat, and helps prevent the sandpaper from clogging. Wet sanding is often used on freshly cured resin surfaces to achieve a glass-like finish.
Benefits of Wet Sanding
1. Dust Reduction One of the most significant advantages of wet sanding is the substantial reduction of dust. Traditional dry sanding creates a considerable amount of dust, which can be harmful when inhaled and can create a messy workspace. Wet sanding contains the dust within the water, making the process cleaner and safer.
2. Heat Control Friction from sanding generates heat, which can lead to resin warping or damage. The use of water cools the surface, allowing for a more controlled sanding process and avoiding overheating.
3. Smoother Finish Wet sanding produces a finer finish than dry sanding. The water helps to fill in the tiny scratches created by the sandpaper, resulting in a smoother surface that reflects light beautifully.
4. Reduced Clogging Wet sanding significantly minimizes the clogging of sandpaper. By keeping the surface damp, debris is washed away, allowing the sandpaper to work more efficiently.
The Wet Sanding Process
wet sanding resin
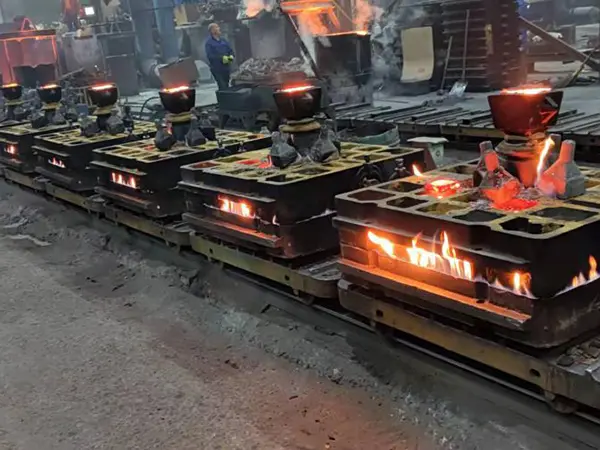
To achieve the best results with wet sanding, follow these steps
1. Preparation Before you begin sanding, ensure that your resin surface is fully cured. This process typically takes several days, depending on the type of resin used and environmental factors. Once cured, clean the surface to remove any debris or dust.
2. Choose the Right Sandpaper Start with a finer grit sandpaper for the initial sanding. A range from 400 to 600 grit is generally recommended. For deeper scratches or imperfections, you may need to start with a coarser grit (around 320 grit) before moving to finer grits.
3. Set Up Your Workspace Prepare a workspace that can accommodate water. Use a plastic basin or a sink to catch the runoff and make the process less messy. Make sure you have enough water to keep the surface continuously wet during the sanding.
4. Sanding Technique Dip the sandpaper in water and begin sanding in a circular motion or back and forth in a consistent direction. Keep the surface moist to reduce friction. Regularly rinse the sandpaper to clean off any debris and to ensure an even sanding process.
5. Inspect Your Work Periodically check the surface to gauge your progress. You’re looking for an even matte finish, which indicates that the sanding has been effective. If you notice any imperfections, take the time to address them before moving to finer grits.
6. Final Steps Once you’ve achieved the desired smoothness, rinse the surface thoroughly to remove any remaining dust and resin particles. You may choose to polish the surface after sanding for an additional glossy finish, using products specifically designed for resin.
Conclusion
Wet sanding resin is an essential technique for anyone looking to achieve a professional finish on their projects. By utilizing this method, you can enhance the beauty and durability of resin products while minimizing mess and increasing efficiency. With patience and practice, you will master wet sanding and elevate your craftsmanship to new heights. So gather your materials, set up your workspace, and get ready to unveil a flawless resin finish. Happy sanding!
Post time:Окт . 16, 2024 09:02
Next:High-Performance Ceramic Sanding Discs for Efficient Surface Finishing