Types of Sand Casting An Overview
Sand casting is one of the oldest and most widely used metal casting processes. Its popularity stems from its versatility, cost-effectiveness, and ability to produce complex shapes with high precision. The process involves creating a mold from sand, which is then filled with molten metal to form the desired product once cooled. There are several types of sand casting techniques, each with its unique characteristics and applications. In this article, we will explore the different types of sand casting, their advantages, and their typical uses.
1. Green Sand Casting
Green sand casting is the most common method of sand casting. In this technique, a mixture of sand, clay, and water is used to create the mold. The term green refers to the moisture content in the sand. Green sand molds are easy to form and have good thermal properties, which allows them to withstand the heat of molten metal. Typically, this method is used for producing large and intricate components, such as engine blocks, frames, and machinery parts.
Advantages - Cost-effective and readily available materials - Good dimensional accuracy - Capable of producing complex shapes
Applications - Automotive parts - Industrial machinery components - Pipeline systems
2. Dry Sand Casting
Unlike green sand casting, dry sand casting involves the use of a sand mixture that has been heated to remove moisture. The mold is assembled and then baked to harden the sand, leading to a more rigid and stable structure. This method is particularly suitable for high-temperature applications where strength is essential.
Advantages - Enhanced mold strength and stability - Better surface finish compared to green sand - Reduced risk of defects caused by moisture
Applications - Aerospace components - High-performance automotive parts - Gearboxes and housings
3. Shell Molding
Shell molding is a type of sand casting process that uses a thin layer of sand mixed with a thermosetting resin to create the mold. This method provides high dimensional accuracy and an excellent surface finish due to the smooth inner surface of the shell. The molds are typically formed around heated patterns, promoting the curing of the resin.
types of sand casting
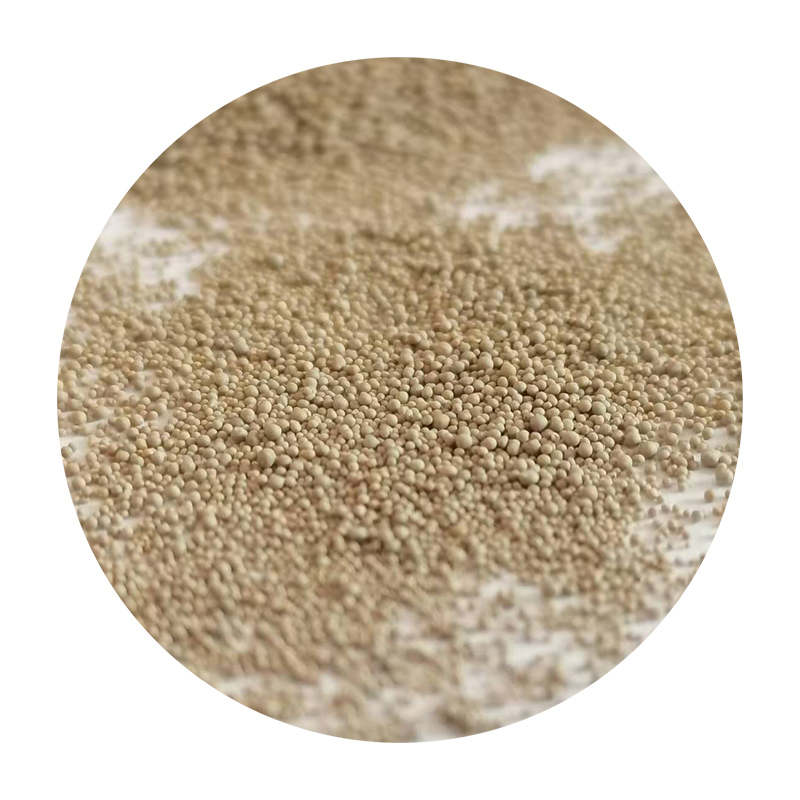
Advantages - High dimensional precision - Excellent surface finish - Reduced machining requirements
Applications - Small to medium-sized parts - Precision-engineered components - Artistic sculptures and complex shapes
4. CO2 Sand Casting
CO2 sand casting utilizes a mixture of sand and sodium silicate, which is activated through a gas (carbon dioxide) to harden the mixture into a mold. This method significantly reduces the moisture content, allowing for improved dimensional stability. CO2 molds can be produced rapidly, making them suitable for low to medium production runs.
Advantages - Quick mold production - Excellent dimensional control - Good surface finish
Applications - Military and defense components - Electrical enclosures - General industrial parts
5. Lost Foam Casting
Lost foam casting is an innovative approach that involves creating a mold from a foam pattern coated with a thin layer of sand. When molten metal is poured into the mold, it evaporates the foam, forming the final product. This method allows for the production of complex shapes with minimal machining.
Advantages - Minimal waste and high casting yield - Exceptional complexity and detail - Reduced need for subsequent machining
Applications - Automotive engine parts - Marine components - Custom and artistic metal objects
Conclusion
Sand casting remains a versatile and widely-used method for producing metal components across various industries. Each type of sand casting technique offers distinct advantages to meet specific manufacturing needs. Understanding these methods allows manufacturers to select the best approach for their projects, ensuring the right balance between quality, cost, and production efficiency. As technology advances, the sand casting process continues to evolve, delivering better precision, reduced environmental impact, and enhanced production capabilities.
Post time:Ное . 27, 2024 08:28
Next:Understanding the Sand Casting Process in Metal Manufacturing Techniques