Types of Sand Casting
Sand casting is one of the most prevalent methods of metal casting, characterized by its versatility, cost-effectiveness, and ability to produce intricate shapes and designs. It involves creating a mold from sand and employing it to shape liquid metal as it cools and solidifies. Different types of sand casting methods are tailored to specific needs of the foundry industry, and understanding these variations can enhance the efficiency and quality of metal production. In this article, we will explore several types of sand casting processes, including green sand casting, dry sand casting, and lost foam casting.
Green Sand Casting
Green sand casting is the most common type of sand casting. The term green refers to the moisture content of the sand mixture, which typically consists of silica sand, clay, and water. This combination allows for sufficient cohesion and gives the mold strength while providing the necessary flexibility to handle metal pours. The green sand molds are created by compacting the sand mixture around a pattern, which is then removed to leave a cavity in the shape of the desired final product.
Green sand casting is popular for its simplicity and effectiveness, making it ideal for creating large quantities of castings in various industries, including automotive and aerospace. Its advantages include the ability to use recycled sand, excellent surface finish, and high precision. However, the moisture content can also lead to defects in casting if not properly managed, necessitating skilled operators during the molding process.
Dry Sand Casting
Unlike green sand casting, dry sand casting employs a mixture that is cured or dried to create stronger molds. The dry sand mixture typically consists of silica sand and a bonding agent, such as sodium silicate, which hardens when exposed to heat. This process results in a more rigid mold that can withstand higher pouring temperatures, making it suitable for casting alloys with a higher melting point, such as aluminum and bronze.
types of sand casting
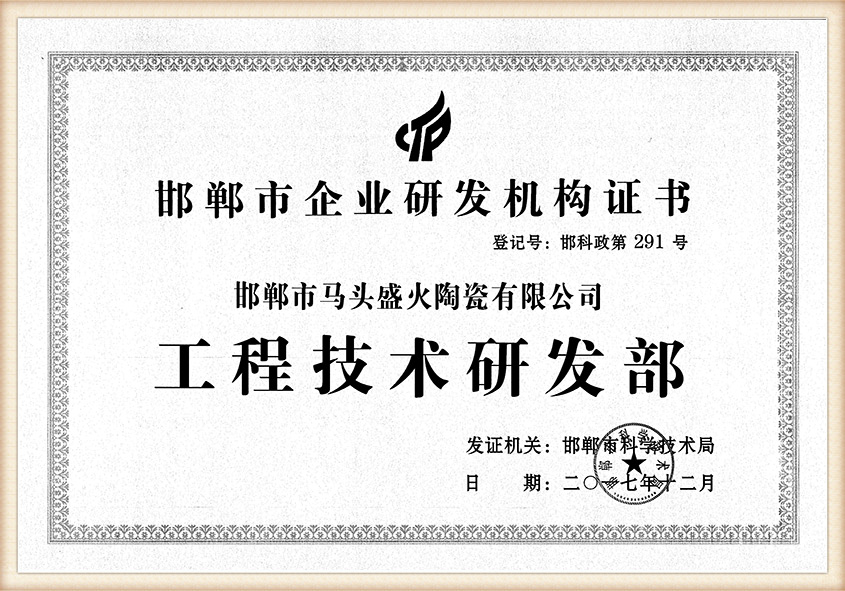
One notable advantage of dry sand casting is its superior surface finish and dimensional accuracy, allowing for the production of complex shapes with finer details. Furthermore, dry sand molds can be reused multiple times, making this method more economical in the long run. However, the setup for dry sand casting may be more labor-intensive, and the drying process can lengthen production time.
Lost Foam Casting
Lost foam casting, also known as evaporative pattern casting, is a more advanced and less conventional method of sand casting. In this process, a foam pattern made from expanded polystyrene is coated with a thin layer of sand, and then the whole assembly is heated. The heat causes the foam to vaporize, leaving a cavity that is then filled with molten metal.
This method provides numerous benefits, including a smooth surface finish with minimal draft required, allowing for more complex geometries. The lost foam process can reduce the need for machining operations on the finished casting, which saves time and costs. While it may offer remarkable advantages for intricate designs, it is not as widely used as green and dry sand casting due to its higher initial costs and specialized equipment requirements.
Conclusion
In summary, the world of sand casting encompasses a variety of techniques, each serving distinct advantages and applications. Green sand casting remains the most widely used due to its efficiency and ease of use. Dry sand casting offers enhanced durability and surface finish, while lost foam casting provides innovative solutions for more complex designs. An understanding of these different types of sand casting methods enables foundries to tailor their processes to meet industry demands, enhance product quality, and improve overall production efficiency. As technology advances, the sand casting industry continues to evolve, embracing new materials and techniques to push the boundaries of metal casting capabilities.
Post time:Ное . 27, 2024 06:30
Next:Understanding the Sand Casting Manufacturing Process for Efficient Production and Quality Control