The Role of Sand in Sand Casting An In-Depth Analysis
Sand casting is one of the oldest and most versatile manufacturing processes in the metallurgical industry. It involves creating a sand mold to form metal parts, which are then poured into the cavity made by the mold. While the selection of metal and the design of the mold are crucial, the type of sand used plays a significant role in determining the quality of the final product. This article explores the types of sand used in sand casting, their properties, and the implications of these materials on the casting process.
Types of Sand Used in Sand Casting
The most commonly used sand for sand casting is silica sand. Silica sand comprises nearly pure quartz and has high melting points, making it suitable for casting metals at high temperatures. However, silica sand can be blended with other materials to enhance its properties. For instance, the addition of clay improves the sand's ability to hold its shape, which is crucial for producing intricate designs and detailed features. Bentonite clay, in particular, is favored for its plasticity and bonding capabilities.
Another type of sand used in the casting process is olivine sand. Olivine is a naturally occurring mineral that can withstand high temperatures and offers better thermal stability than silica sand. This makes olivine an excellent choice for casting ferrous alloys prone to oxidation. Additionally, olivine sand is less abrasive than silica sand, which can prolong the life of molds and reduce wear on casting equipment.
Properties of Casting Sand
The success of a sand casting operation heavily depends on the properties of the sand used. Key characteristics include grain size, shape, and distribution, as well as moisture content. Fine-grained sands allow for better surface finish and detail, while coarser sands provide better strength and airflow. Round grains generally improve flowability, while angular grains enhance mold strength.
sand used for sand casting
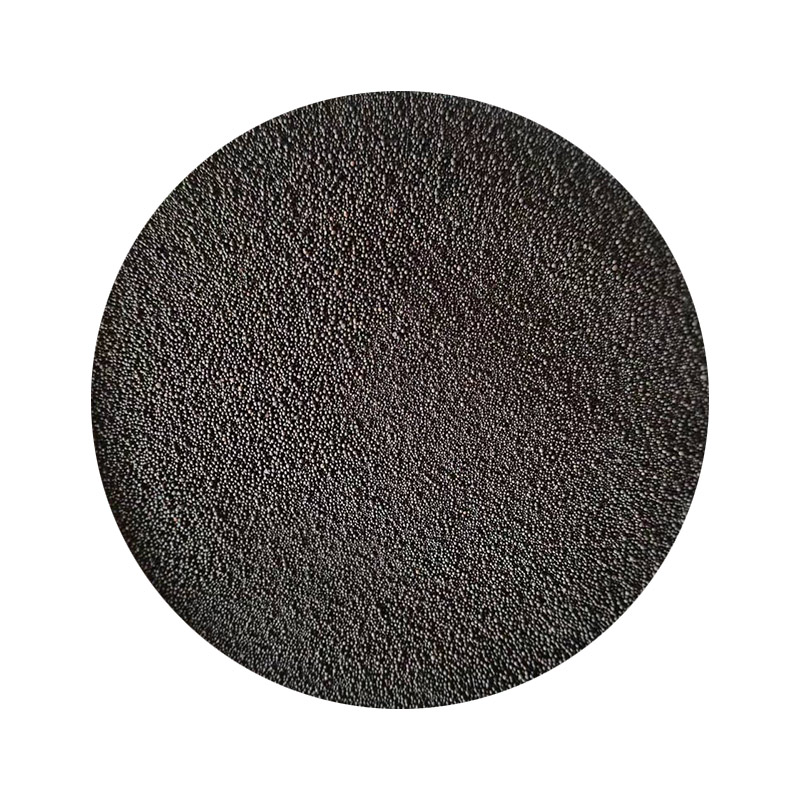
Moisture content is another critical factor. Properly conditioned sand requires a specific moisture level to ensure adequate bonding and strength without leading to excessive evaporation during the metal pouring process. Too little moisture can result in a weak mold, while excess moisture may cause defects, such as blowholes, in the final casting.
Recycling and Sustainability
One of the significant advantages of sand casting is the ability to recycle used sand. After a casting operation, the sand can be cleaned and reused, significantly reducing material waste and cost. The recycling process involves removing the residual binder and impurities, allowing the sand to be employed in future molds without a substantial loss in quality.
This sustainability aspect contributes to the growing interest in sand casting, particularly in industries aiming to reduce their carbon footprint. Moreover, the development of eco-friendly binders and additives has become prominent, with an emphasis on minimizing the environmental impact of sand casting processes.
Conclusion
Sand casting remains a fundamental process in metal fabrication, and the type of sand used is paramount in determining the efficacy and quality of the final product. Silica sand continues to be the most prevalent material, bolstered by innovations in recycling and sustainable practices, helping to meet the demands of a modern, environmentally-conscious market. Additionally, the exploration of alternative sands, such as olivine, demonstrates the industry's adaptability in optimizing material properties for specific applications. As technology progresses, the future of sand casting will likely involve enhanced techniques and materials, ensuring its relevance in contemporary manufacturing.
Thus, understanding the intricacies of sand casting and the importance of selecting the right sand cannot be overstated. It is this knowledge that underpins many successful manufacturing operations, bridging traditional methods with the future of production technology.
Post time:Ное . 08, 2024 22:39
Next:Creative Sand Casting Techniques for Unique Artistry and Functional Designs