Sand Casting Technology An Overview
Sand casting, one of the oldest and most versatile metal casting processes, is widely used in the manufacturing industry for producing metal parts and components. This technique involves pouring molten metal into a sand mold, which hardens to form the final product. The process is popular for its simplicity, cost-effectiveness, and ability to create intricate shapes, making it suitable for both small-scale and large-scale production.
History and Evolution
The roots of sand casting can be traced back to ancient civilizations, where artisans used natural sand mixed with clay to create molds. Over the centuries, the process has evolved significantly, incorporating modern materials and technologies. Today, advancements in simulation software and mold-making techniques have enhanced the precision and efficiency of sand casting, allowing for more complex designs and improved quality of the castings.
Process Overview
The sand casting process begins with the creation of a pattern, which is typically made of metal, plastic, or wood. This pattern serves as a replica of the final component and is used to form the mold. The mold is created by compacting a mixture of sand, clay, and water around the pattern. Once the mold is prepared, the pattern is removed, leaving a cavity in the shape of the desired part.
Molten metal is then poured into the mold cavity. This metal can be a variety of alloys, including aluminum, iron, or copper, depending on the application and required properties of the final product. After the metal solidifies and cools, the mold is broken apart to reveal the cast part, which often requires further finishing processes such as machining, sanding, or polishing to achieve the desired surface quality and dimensions.
Advantages of Sand Casting
sand casting technology
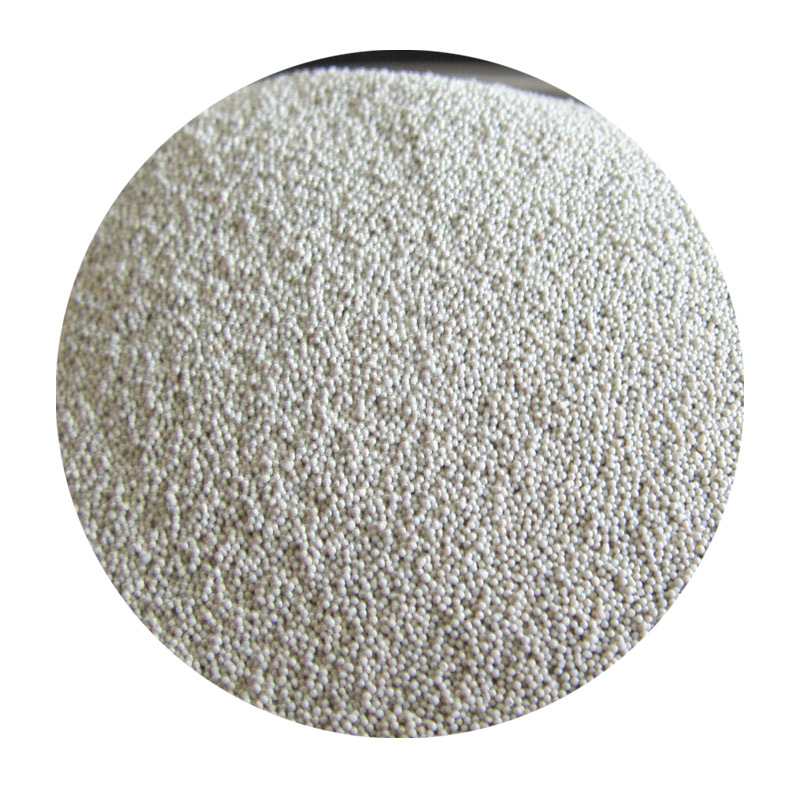
One of the primary advantages of sand casting is its flexibility. It can accommodate a wide range of sizes and complex geometries, enabling manufacturers to produce anything from small components to large engine blocks. The materials used in the molds are not only cost-effective but also readily available, making it an economical choice for various applications.
Moreover, sand casting allows for the use of diverse metal alloys, which can be tailored to meet specific mechanical properties and functionalities. This versatility is crucial in industries such as automotive, aerospace, and construction, where different parts require unique material characteristics.
Challenges and Considerations
Despite its many benefits, sand casting also poses challenges. The surface finish of cast parts can sometimes be rough, requiring additional machining to achieve a smooth finish. Additionally, while the process is effective for low to medium production runs, it may not be the most efficient method for high-volume production, where processes like die casting might be more suitable.
Control over the casting process is another challenge. Factors such as sand composition, moisture content, and temperature of the molten metal can significantly affect the quality of the final product. As such, manufacturers must carefully monitor these variables to minimize defects such as porosity, shrinkage, and misalignment.
Conclusion
In conclusion, sand casting technology remains a foundational technique in the manufacturing industry due to its adaptability, cost-effectiveness, and capability to produce complex shapes. As technology continues to advance, the methods and materials used in sand casting are likely to become even more refined, increasing its potential for precision and efficiency. With its rich history and ongoing innovation, sand casting will undoubtedly continue to play a crucial role in the production of metal components across various industries for years to come.
Post time:Сеп . 28, 2024 14:19
Next:ceramsite foundry sand