The Advantages of Sand Casting
Sand casting, one of the oldest and most versatile casting methods, is a manufacturing process widely employed in various industries for producing metal parts and components. Known for its adaptability and cost-effectiveness, sand casting offers several advantages that make it a preferred choice for both large and small-scale production. This article delves into the benefits of sand casting and why it remains a valuable process in metal fabrication today.
1. Cost-Effectiveness
One of the most significant advantages of sand casting is its cost-effectiveness. The materials needed for sand casting, primarily sand and metal, are relatively inexpensive compared to other casting methods. The molds used in sand casting are made of sand mixed with a binding agent, often clay, which can be reused multiple times. This reduces the overall costs associated with producing molds, making it an economically viable option for businesses of all sizes.
Another aspect that contributes to its cost-effectiveness is the simplicity of the setup. Unlike more complex processes that require expensive machinery and equipment, sand casting primarily depends on manual labor and basic tools. This makes it a suitable option for small foundries and startups looking to minimize their initial investment.
2. Design Flexibility
Sand casting offers remarkable design flexibility, allowing for the production of complex shapes and geometries that would be challenging or impossible to achieve using other casting methods. The malleability of sand allows for intricate designs, including undercuts and thin-walled features, without the need for extensive tooling.
This flexibility extends to various materials as well, enabling manufacturers to cast parts from ferrous and non-ferrous metals, including aluminum, brass, and iron. As a result, sand casting is ideal for a broad range of applications, from automotive components to aerospace parts.
sand casting advantages
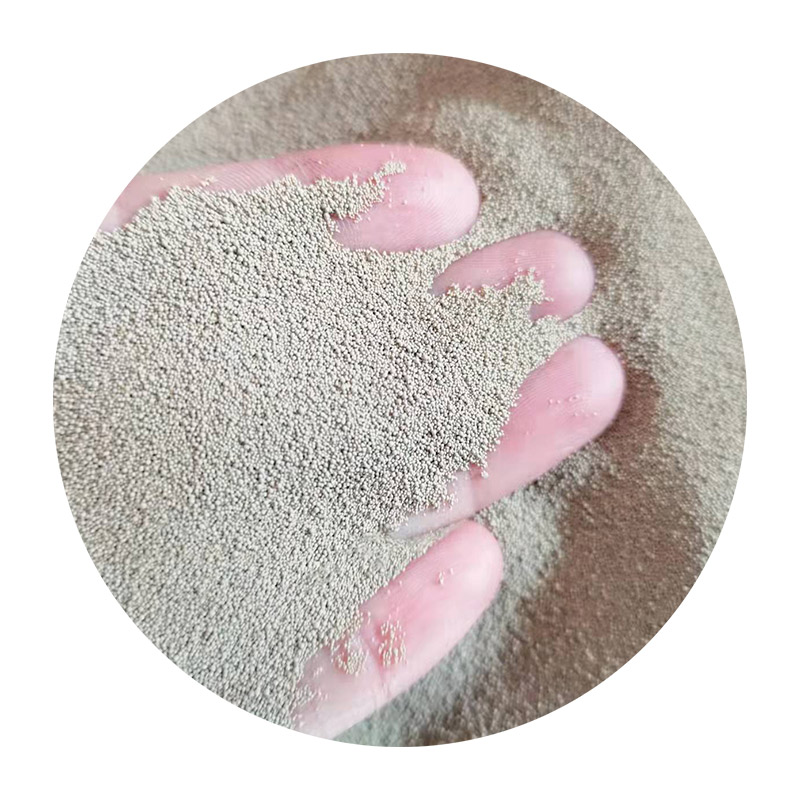
Another major advantage of sand casting is its ability to accommodate a wide range of part sizes. Whether producing small components or large industrial pieces, sand casting can be adapted to meet the requirements of the project. The process is not limited by size constraints, making it an excellent choice for industries that require both small-batch and large-batch production.
The scalability of sand casting means that it can cater to various production needs. For instance, it is frequently used in prototyping, allowing manufacturers to create a small number of parts for testing before committing to larger production runs. This ability to transition smoothly between small and large-scale production enhances its value as a manufacturing technique.
4. Good Surface Finish and Large Tolerances
While sand casting may not always achieve the same level of surface finish as other casting processes, it often provides acceptable results for many applications. The surface finish can be improved through various post-casting treatments, such as machining and grinding, making it suitable for components that have specific surface finish requirements.
Additionally, sand casting provides reasonable tolerance levels, which means that the dimensions of the finished product can be closely controlled. This is crucial for ensuring that parts fit together correctly in assemblies and meet the specifications required for their intended use.
5. Easy Modification and Repair
The sand casting process is relatively easy to modify, allowing for quick adjustments to the mold if design changes are necessary. This adaptability bends well to the needs of modern manufacturing, where rapid changes in design are commonplace. If a defect occurs during casting, repairs can often be made without the need for extensive rework, which saves time and resources.
Conclusion
In summary, sand casting remains a highly advantageous manufacturing process due to its cost-effectiveness, design flexibility, versatility in size and scale, adequate surface finishes, and ease of modification. These benefits make it a valuable option for a wide range of industries, including automotive, aerospace, and general manufacturing. As technology continues to evolve, the principles of sand casting remain relevant, proving that traditional methods can still hold their ground in a rapidly advancing manufacturing landscape. Whether for prototyping or large-scale production, sand casting offers an efficient and reliable solution to meet diverse metalworking needs.
Post time:Окт . 11, 2024 15:54
Next:g2 super sand