Understanding Sand Casting 101 An Introduction to the Basics
Sand casting is one of the oldest and most versatile metal casting processes. It involves creating a mold from sand, into which molten metal is poured to create a desired shape. This method has been used for centuries and remains popular today due to its low cost, simplicity, and ability to produce complex geometries. In this article, we will delve into the fundamentals of sand casting, exploring its components, processes, and applications.
What is Sand Casting?
At its core, sand casting is a method of manufacturing parts by pouring liquid metal into a mold made of sand. The sand used is typically mixed with a binding agent (like clay) to help it hold its shape. The molds are formed in two halves, known as the cope (top half) and the drag (bottom half), which come together to create a hollow cavity in the shape of the desired part.
Equipment and Materials
The primary materials used in sand casting are sand, a binder, and the metal itself.
1. Sand The most commonly used sand in casting is silica sand, valued for its grain size, shape, and consistency. It usually makes up about 90% of the mold material's composition. 2. Binder Clay is the most common binder, providing cohesion to the sand grains. Other binders like resin or synthetic materials are also used, especially in modern applications where finer detail and improved surface finish are required. 3. Metal Various metals, including aluminum, bronze, and iron, can be used in sand casting, depending on the desired properties of the finished product.
The Sand Casting Process
The sand casting process can be broken down into several key steps
1. Pattern Making A pattern is created, typically from wood or metal, which reflects the shape of the final product. The pattern is slightly larger than the finished piece to account for shrinkage during cooling.
2. Making the Mold The pattern is pressed into a mixture of sand and binder to create two halves of the mold. The sand is compacted around the pattern to ensure it retains the shape, and the two halves are then joined.
3. Pouring Once the mold is prepared, molten metal is poured into the cavity. The metal needs to be heated above its melting point and poured quickly to avoid premature solidification.
sand casting 101
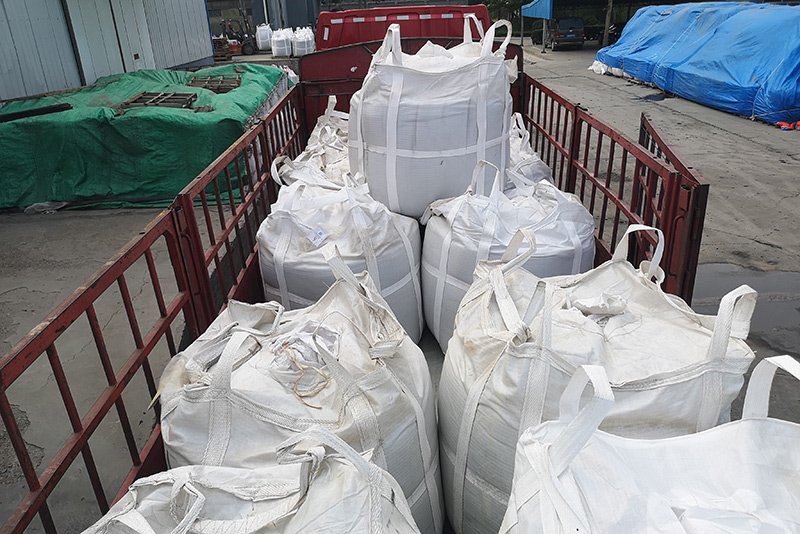
4. Cooling and Solidifying After the metal has filled the mold, it is left to cool and solidify. This process can take several hours, depending on the size of the part and the type of metal used.
5. Removing the Casting Once cool, the sand mold is broken away to reveal the casting. Any rough edges or irregularities are cleaned up using grinding or machining.
6. Finishing The casting may undergo additional finishing processes to enhance its surface quality or to add specific features.
Advantages of Sand Casting
Sand casting offers several advantages
- Cost-Effective The materials used are generally inexpensive, making it a cost-effective option for both small batch production and large-scale manufacturing. - Versatile It can accommodate a wide range of metals and is suitable for complex geometries and large sizes.
- Flexible It allows for the production of custom parts, making it ideal for prototype development and specialty applications.
Applications
Sand casting is widely used across various industries, including automotive, aerospace, and art metalwork. Common products made using this process range from engine blocks and valve bodies to intricate sculptures and tools.
Conclusion
In conclusion, sand casting is a fundamental manufacturing technique that has stood the test of time. Its simplicity, cost-effectiveness, and versatility make it an essential process in the production of metal parts. Whether creating large components for industrial machinery or crafting delicate decorative items, sand casting remains a vital skill in the world of metalworking. Understanding its principles and processes can provide valuable insights into its applications, ensuring more efficient production and innovation in this age-old craft.
Post time:Дек . 03, 2024 12:21
Next:where to buy foundry sand