Understanding Resin Sand Its Composition and Applications in Modern Casting
Resin sand, a composite material used in the field of foundry and metal casting, has gained significant popularity due to its superior properties compared to traditional sand casting methods. This innovative material is composed of a mixture of sand and a thermosetting resin binder, which is activated by heat or chemical reactions. The resultant mixture forms a strong, durable mold that can produce highly detailed and accurate castings.
One of the primary advantages of resin sand is its excellent dimensional stability. Traditional sand molds often suffer from deformation during the casting process, which can lead to dimensional inaccuracies and defects in the final product. In contrast, resin sand molds maintain their shape under thermal stress, allowing for the production of intricate designs with high precision. This characteristic makes resin sand particularly appealing in industries where fine detail is critical, such as aerospace, automotive, and artistic metalwork.
Additionally, resin sand offers improved surface finish in castings. The smoother surface of the resins reduces the need for extensive post-processing, thereby saving time and costs in production. This is especially beneficial in applications where visual aesthetic and surface integrity are paramount. With reduced defects like sand inclusions and surface roughness, manufacturers can produce high-quality components that meet stringent industry standards.
resin sand
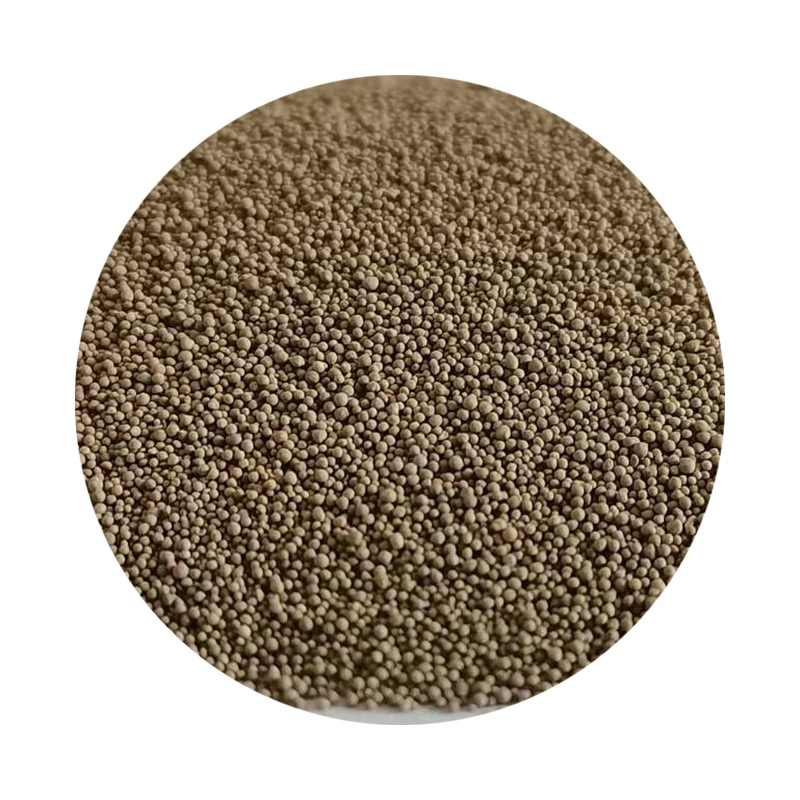
Another notable feature of resin sand is its versatility. It can be tailored to meet specific requirements by adjusting the resin type, curing methods, and sand grain size. This flexibility allows foundries to optimize the material properties based on the demands of their casting processes. Moreover, the ability to reuse resin sand after proper treatment contributes to sustainable practices within the industry, as it minimizes waste and promotes resource conservation.
Safety is also a key consideration in the use of resin sand. Unlike conventional sand, which can release harmful crystalline silica dust, resin sand formulations are often designed to minimize dust generation, enhancing workplace safety for operators. This improvement aligns with health regulations and promotes a safer working environment.
Despite its advantages, there are challenges associated with resin sand that stakeholders must be aware of. The initial investment in equipment and materials can be higher than traditional methods, and the disposal of used resin sand requires careful management to mitigate environmental impacts.
In conclusion, resin sand represents a significant advancement in the foundry industry, offering enhanced dimensional accuracy, improved surface quality, and versatility in applications. As technology continues to evolve, the adoption of resin sand in various casting operations is likely to increase, driven by the demand for high-quality, complex components across numerous sectors. The ongoing development of eco-friendly resins and efficient disposal methods will further bolster its position as a preferred choice in modern metal casting practices.
Post time:Сеп . 23, 2024 07:10
Next:custom sand casting