The Application of Resin Sand in Modern Casting Processes
Resin sand has emerged as a pivotal material in modern foundry practices, revolutionizing the casting industry with its superior properties and versatility. This advanced sand mixture, typically consisting of silica sand, a resin binder, and a catalyst, offers numerous advantages over traditional molding sands, making it a preferred choice for casting intricate shapes and components.
One of the most significant benefits of resin sand is its excellent dimensional accuracy. The resin binder hardens rapidly when exposed to heat, allowing for precise replication of molds. This accuracy is crucial in industries where tolerances are stringent, such as aerospace and automotive manufacturing. The ability to produce highly detailed parts reduces the need for extensive post-casting machining, thereby saving time and costs.
Additionally, resin sand exhibits remarkable strength and durability. The hardened sand mold can withstand the high temperatures and pressures associated with metal pouring, reducing the risk of mold deformation during the casting process. This characteristic is especially beneficial for heavy castings, where traditional sand molds might falter, leading to defects and wasted materials. The enhanced strength also translates to fewer casting failures, ensuring a more efficient production cycle.
resin sand
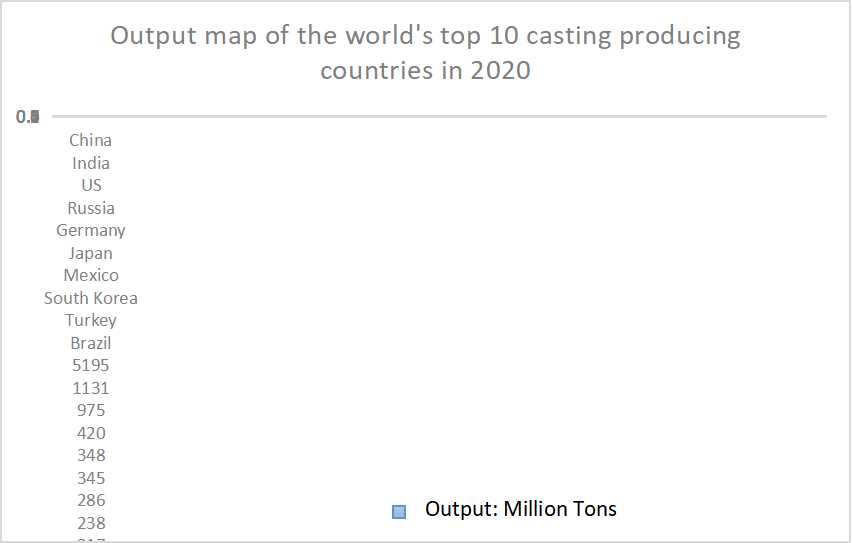
Another significant advantage of resin sand is its flexibility in design
. Foundries can create complex shapes and patterns that would be challenging, if not impossible, to achieve with conventional sand molds. This flexibility allows engineers and designers to push the boundaries of innovation, developing products that meet modern performance requirements without being constrained by traditional manufacturing techniques.Environmental concerns have also prompted the casting industry to innovate, and resin sand contributes positively in this area. Unlike some traditional molding sands that can generate airborne silica dust, resin sand minimizes dust emissions, enhancing workplace safety. Moreover, advancements in eco-friendly resin formulations have emerged, allowing foundries to use sustainable materials, which align with the industry's increasing focus on reducing its environmental footprint.
The versatility of resin sand extends beyond its casting applications. It can be utilized in various industries, including art, sculpture, and even architectural models, showcasing its adaptability. As foundries continue to embrace technology and automation, the use of resin sand will likely become even more widespread, helping to meet the growing demands for precise and complex components.
In conclusion, resin sand has transformed the casting landscape by offering solutions that balance performance, efficiency, and environmental responsibility. Its ability to produce high-quality, intricate castings with reduced waste positions it as a key material for future innovations in manufacturing. As technology advances, it will be exciting to see how resin sand continues to evolve and shape the future of the casting industry.
Post time:Ное . 19, 2024 07:24
Next:steps in sand casting