The Manufacturing Process of Resin Coated Sand
Resin coated sand (RCS) is a crucial material in the foundry industry, primarily used for making molds and cores in metal casting processes. The adoption of resin coated sand has transformed traditional casting techniques by offering superior quality, enhanced surface finishes, and improved mechanical properties. This article delves into the manufacturing process of resin coated sand, highlighting its components, stages, and advantages.
Understanding Resin Coated Sand
Resin coated sand consists of high-quality silica sand coated with a thermosetting resin. The typical resins used include phenolic, furan, and epoxy resins, which, when heated, harden and bind the sand grains together. The final product exhibits excellent dimensional accuracy, lower gas porosity, and superior strength, making it ideal for high-precision applications.
Manufacturing Process Overview
The manufacturing process of resin coated sand encompasses several key steps sand selection, mixing, coating, heating/catalyzation, cooling, and screening. Let's take a closer look at each of these stages.
1. Sand Selection The process begins with selecting high-quality silica sand. The characteristics of the sand — such as grain size, shape, and purity — significantly affect the performance of the final product. Coarse grains with uniform particles are preferred, as they contribute to better flowability and strength.
2. Mixing Selected silica sand is then mixed with resin and a catalyst. The mixing equipment must ensure a homogeneous blend, as this uniformity is crucial for consistent coating. Usually, the mixing process is carried out in a batch mixer, where the resin is introduced in a controlled manner to prevent clumping and ensure even distribution.
resin coated sand manufacturing process
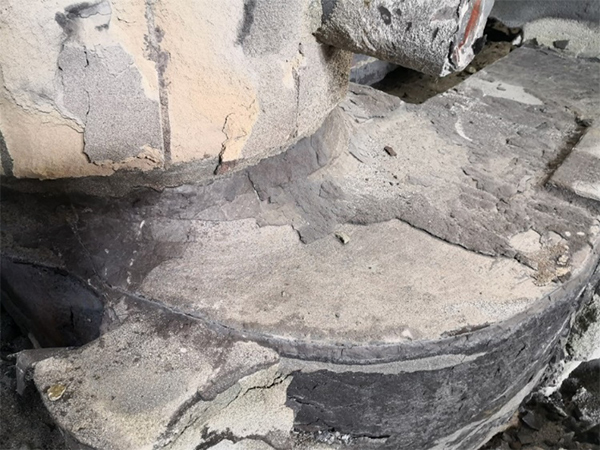
3. Coating After achieving a uniform mixture, the next step is coating the sand with resin. This is typically performed in a rotating drum or a fluidized bed system, allowing the sand grains to be evenly coated with the resin. The quantity of resin used is carefully calculated to ensure that each grain is adequately coated without becoming overly sticky.
4. Heating and Catalyzation Subsequently, the coated sand is subjected to a heat treatment, which activates the resin and initiates the curing process. Heating can be done using hot air or infrared heaters, and the temperature and duration are meticulously controlled to ensure optimal curing. The heat causes the resin to harden, binding the sand grains together and providing the necessary strength.
5. Cooling After the curing process, the sand must be cooled to avoid thermal shock or damage to the structure. This stage is critical as it ensures the integrity of the resin-coated sand before it is moved to the next phase.
6. Screening Finally, the cooled resin coated sand undergoes screening to eliminate any oversized or agglomerated particles. This step ensures the consistency of the grain size and quality of the final product, making it ready for use in molding operations.
Advantages of Resin Coated Sand
Resin coated sand presents several compelling advantages over traditional molding materials. First and foremost, it enables the production of highly detailed and intricate shapes due to its ability to flow into complex mold geometries. Additionally, RCS provides a smoother surface finish on castings, reducing the need for post-casting treatments.
Furthermore, resin coated sand exhibits enhanced dimensional stability and strength, allowing for high-temperature applications and reducing defects associated with traditional sand molds, such as shelling and casting distortion. Its superior resistance to thermal shock and oxidation contributes to longer mold life, thus reducing overall production costs.
In conclusion, the manufacturing process of resin coated sand is a sophisticated and highly controlled series of steps designed to produce high-quality molding materials for the foundry industry. With its numerous benefits including improved surface finishes, dimensional accuracy, and operational efficiency, resin coated sand has become increasingly popular in modern metal casting practices. As the industry evolves, continued innovation in RCS technology will likely lead to even greater enhancements in casting quality and production efficiency.
Post time:Сеп . 25, 2024 19:17
Next:metal casting sand