Understanding Parting Sand in Foundry Processes
In the world of metal casting, foundries play a crucial role in manufacturing components used in a wide array of industries, including automotive, aerospace, and construction. Among the many techniques and materials employed within foundries, parting sand holds significant importance. Understanding its role, properties, and applications can enhance our grasp of the overall casting process.
Parting sand, also known as parting powder or parting agent, is a material used in the foundry to separate different components of a mold during the casting process. It serves as a barrier between the cope (the top half of a mold) and the drag (the bottom half), preventing the two parts from sticking together once the mold has been formed. This separation is vital for ensuring that the mold can be opened easily without damaging it or the casting itself.
Composition and Characteristics of Parting Sand
Typically made from finely ground silica sand, parting sand may also include various additives to improve its performance. The primary characteristics that make parting sand effective include its fine texture, light weight, and thermal resistance. When applied to the surfaces of the mold, it creates a thin, even layer that minimizes friction. This allows for the smooth release of the casting after it has cooled and solidified.
In addition to these physical properties, parting sand must possess chemical stability so that it does not adversely react with the molten metal during the casting process. The choice of parting sand can influence the surface finish of the casted products. A high-quality parting sand will yield a smoother surface finish whereas inferior quality may lead to surface defects and increased machining costs.
Applications of Parting Sand
parting sand in foundry
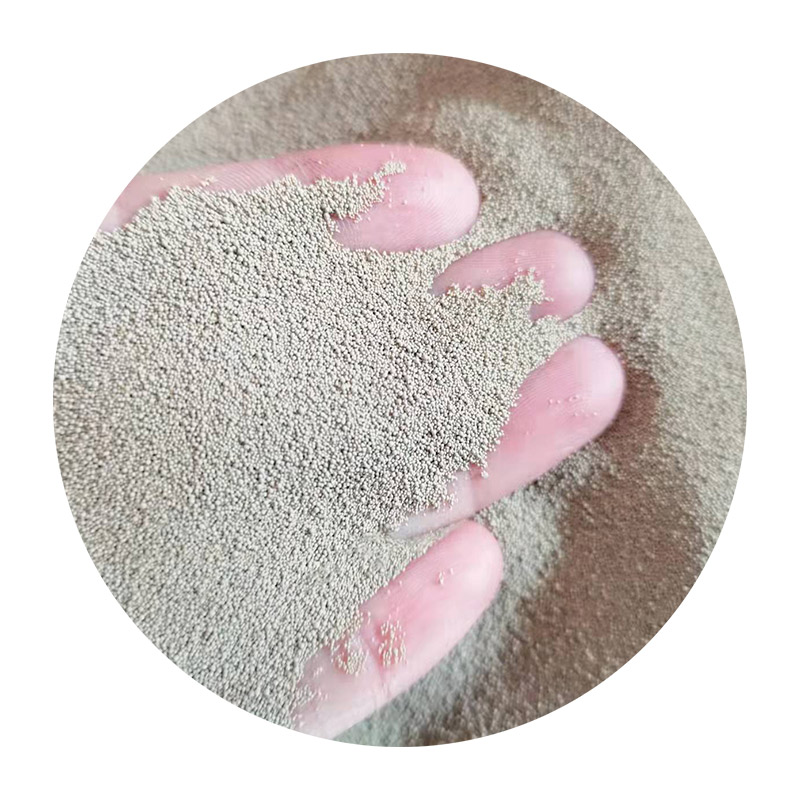
Parting sand is essential in various casting techniques, including sand casting, investment casting, and shell casting. In sand casting, which is one of the most common techniques used in foundries, parting sand is applied directly to the mold surfaces. In investment casting, where precision is paramount, a thin layer of parting sand ensures that the wax patterns can be easily released from the mold after the metal is poured.
Moreover, in shell casting, parting sand helps to create a fine finish on the shell molds. The proper application of parting sand not only facilitates the easy removal of the molds but also aids in achieving intricate designs and detailed specifications which are critical for precision components.
Importance of Parting Sand in Quality Control
The use of parting sand is also an integral component of quality control within foundries. During the casting process, if parting sand is not applied correctly, it can lead to defects such as misalignment, casting defects, or even complete mold failure. Therefore, foundries must adhere to strict guidelines in its application. Consistent monitoring of the sand's grain size and cleanliness is required to ensure optimal performance.
Additionally, with advances in technology, some modern foundries have started using synthetic parting agents which offer enhanced properties compared to traditional silica sand. These agents provide better release characteristics and reduce the amount of dust produced during the casting process, improving working conditions for foundry personnel.
Conclusion
In conclusion, parting sand is a vital component of the foundry industry, playing a critical role in the casting process. Its ability to prevent molds from sticking together ensures smooth operations and high-quality output. By understanding the properties, applications, and importance of parting sand, foundries can not only improve their manufacturing processes but also enhance the quality and precision of the final products. As the industry continues to evolve, innovations in parting agents may further transform how foundries approach casting, underscoring the ongoing importance of this fundamental material in the world of manufacturing.
Post time:Ное . 19, 2024 22:47
Next:sand casting sand types