Lost foam casting is an innovative casting process widely used in various industries due to its unique advantages and versatility. This technique, which can produce intricate shapes and complex geometries, has found applications across many sectors, including automotive, aerospace, and general manufacturing. By utilizing a foam pattern that is vaporized during the metal pouring process, lost foam casting allows for the creation of objects with minimal machining and reduced material waste.
One of the primary applications of lost foam casting is in the automotive industry, where precision and efficiency are critical. The process enables manufacturers to create complex engine components, transmission cases, and brackets with high accuracy and a smooth surface finish. The ability to produce lighter components without compromising strength is particularly valuable in the modern push for fuel efficiency and reduced emissions. By minimizing the weight of parts, lost foam casting contributes directly to the overall efficiency of vehicles.
In the aerospace sector, the demand for lightweight and strong materials is even more pronounced. Lost foam casting is used to manufacture components such as turbine housings and heat exchangers, which require high-performance materials that can withstand extreme conditions. The fine details achievable with this method help in optimizing performance, leading to improved fuel efficiency and operational reliability. Additionally, the reduction in machining requirements associated with lost foam casting can translate to cost savings—an essential factor in aerospace manufacturing.
Beyond automotive and aerospace, lost foam casting also finds application in the production of artistic and architectural pieces, where creative designs often defy conventional manufacturing methods. Artists and designers can leverage the flexibility of foam patterns to create unique sculptures and features in buildings. The ability to replicate intricate details ensures that the final products maintain the intended aesthetic while benefiting from the durability of metal.
lost foam casting applications
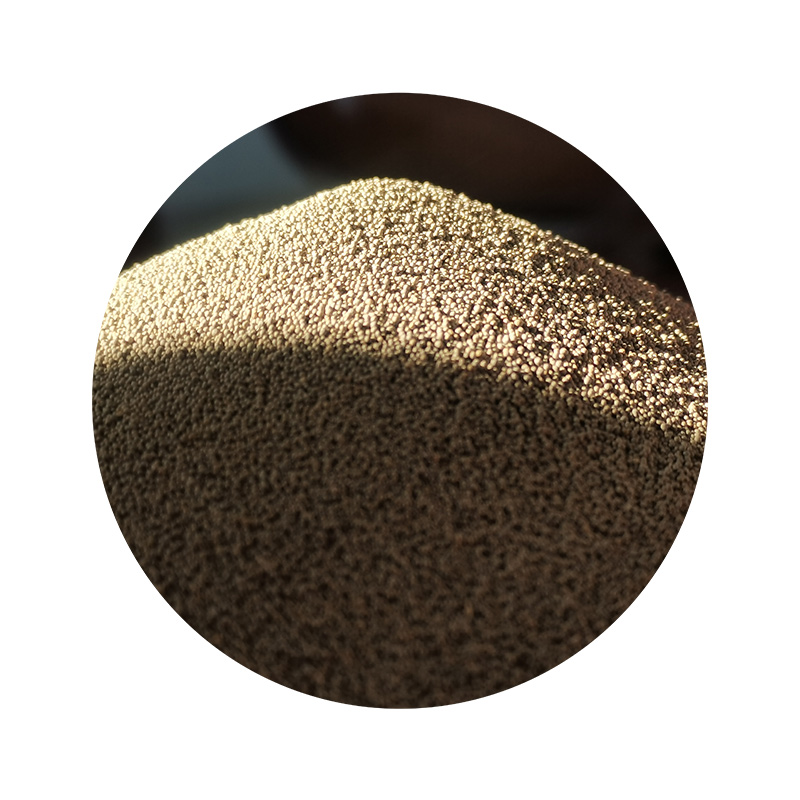
The foundry industry has embraced lost foam casting for its advantages in producing complex parts with fewer defects. The elimination of molds and cores reduces the chance of errors associated with traditional casting processes. Moreover, the foam pattern vaporizes during the metal pouring, allowing for an excellent match of the internal and external surfaces of the final product. This aspect is particularly beneficial when producing parts that require tight tolerances.
As technology advances, the lost foam casting process itself has also improved
. Enhanced foam materials and better control over the pouring and cooling processes have increased the viability of this casting technique for a broader range of materials, including aluminum, iron, and even specialized alloys.In conclusion, lost foam casting stands out as a highly efficient method for producing intricate and lightweight components across diverse industries. Its applications in automotive, aerospace, and artistic fields highlight its versatility and capability to meet modern manufacturing demands. With ongoing advancements in casting technology, lost foam casting is likely to see continued growth and innovation, further solidifying its role in the future of manufacturing.
Post time:Сеп . 24, 2024 09:44
Next:Understanding the Density of Foundry Sand and Its Impact on Casting Processes