Understanding Sand Casting A Fundamental Manufacturing Process
Sand casting is one of the oldest and most versatile manufacturing processes used to create metal parts and components. This process involves pouring molten metal into a sand mold, which is formed to create a desired shape. With roots in ancient civilizations, sand casting has evolved significantly over the years and continues to be a fundamental technique in modern manufacturing.
The Basics of Sand Casting
The sand casting process begins with creating a pattern, which is a replica of the object to be cast. Patterns are usually made from materials like wood, metal, or plastic. The pattern is then placed in a mold box, and sand mixed with a binding agent (usually clay) is packed around it, forming a mold cavity. Once the sand is compacted, the pattern is removed, leaving a cavity that mirrors the shape of the original object.
After preparing the mold, the next step is to melt the metal, typically aluminum, iron, or bronze. The molten metal is poured into the mold cavity through channels created in the sand. Once the molten metal solidifies, the mold is broken away to reveal the casting.
Advantages of Sand Casting
One of the main advantages of sand casting is its remarkable flexibility. It can accommodate a wide range of metal alloys and is capable of producing large, complex geometries. Unlike other casting methods, sand casting does not have a limit on the size of the part produced, making it suitable for both small and large components.
Additionally, sand casting is relatively low in cost compared to other production methods. The materials used (sand, metal, and binders) are inexpensive, and the process does not require sophisticated machinery. This makes it an attractive option for both prototype development and low to medium production runs.
Applications of Sand Casting
Sand casting is widely used across various industries. The automotive sector, for example, relies on sand casting to produce engine blocks, transmission cases, and exhaust manifolds. The marine industry also utilizes this technique for creating components like propellers and hull fittings.
describe sand casting
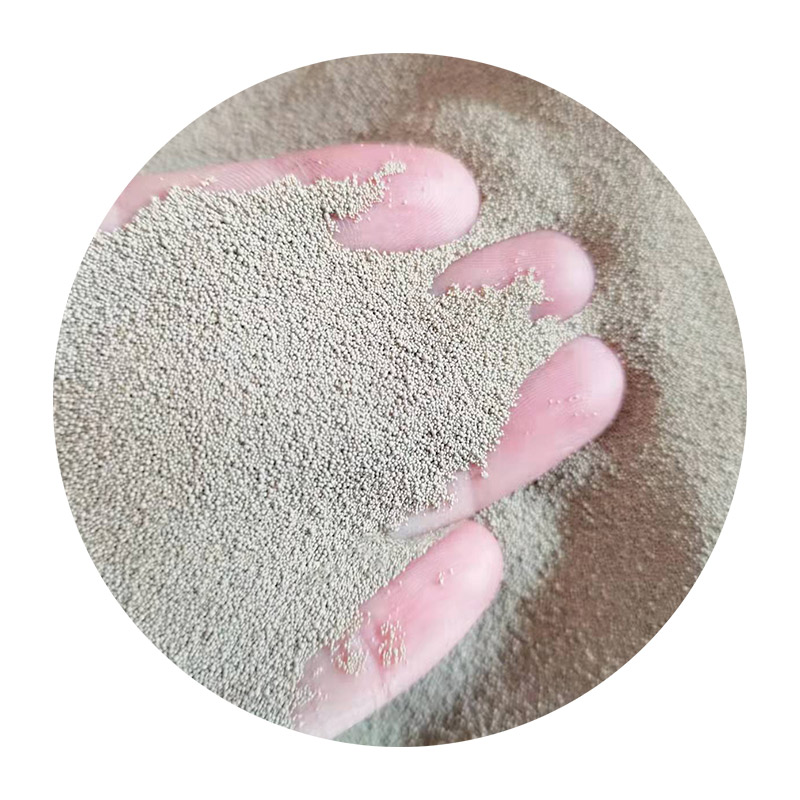
Moreover, sand casting is not limited to industrial applications; it is also found in the manufacturing of artistic pieces, such as sculptures and decorative items. Artists and sculptors often use sand casting to create intricate designs that would be difficult to achieve through other means.
Environmental Considerations
While sand casting has many advantages, it is essential to consider its environmental impact. The process generates waste materials, particularly spent sand. However, advancements in technology have allowed some foundries to recycle sand, minimizing the waste produced. Additionally, modern practices are increasingly focusing on using environmentally friendly binders and reducing emissions during metal melting.
Challenges in Sand Casting
Despite its advantages, sand casting does face challenges. One of the primary issues is achieving a high level of dimensional accuracy, as the process can lead to defects such as shrinkage, porosity, and surface imperfections. Skilled craftsmanship and careful attention to detail during the mold-making process can help mitigate these concerns.
Furthermore, the quality of the sand used and the consistency of the mixture play crucial roles in the final product's quality. Variations in sand quality can lead to fluctuations in mold strength, affecting the precision of the casting.
Future of Sand Casting
Looking ahead, sand casting is poised to benefit from technological advancements, including automation and computer-aided design (CAD). These innovations are enhancing the precision and efficiency of the casting process, making it more competitive with other manufacturing techniques.
In conclusion, sand casting remains a critical manufacturing process with a rich history and a promising future. Its versatility, cost-effectiveness, and capability to produce complex shapes make it an invaluable technique in various industries. As technology continues to advance, sand casting is likely to evolve, further solidifying its place in modern manufacturing. Whether it is for industrial applications or artistic creations, the legacy of sand casting endures, showcasing the ingenuity of this timeless technique.
Post time:Дек . 19, 2024 19:39
Next:components of sand casting