The Importance of Casting Sand Suppliers in the Foundry Industry
In the world of manufacturing, the foundry industry plays a pivotal role, particularly in the production of metal components used in various sectors, including automotive, aerospace, and machinery. One of the essential materials in this process is casting sand, a crucial element that significantly influences the quality of the final product. Casting sand suppliers are vital to ensuring that foundries have access to high-quality materials that meet their specific needs.
Understanding Casting Sand
Casting sand, also known as foundry sand, is a granular material used in the metal casting process. It serves as a mold material, allowing molten metal to be poured into a specific shape that will solidify into a desired component. The most common type of casting sand is silica sand due to its unique properties, which include high thermal stability, permeability, and a low coefficient of thermal expansion. These features make it ideal for withstanding the high temperatures of molten metal and allowing gases to escape during the cooling process.
Types of Casting Sand
There are several types of casting sands available, each suited for different applications. The most popular types include
1. Silica Sand This is the most widely used type of casting sand due to its availability and cost-effectiveness. It is primarily composed of silicon dioxide and can be found in various grain sizes, which can be tailored to the needs of the foundry.
2. Clay-Bonded Sand This type of sand is mixed with clay to improve its binding properties. It is used in various casting processes and provides a good strength-to-weight ratio, making it ideal for complex molds.
3. Resin-Bonded Sand This specialized type of sand is combined with a resin to offer better binding and durability. It is particularly useful for producing highly detailed, intricate molds as it allows for finer detail than traditional methods.
4. Zircon Sand Known for its high melting point and thermal stability, zircon sand is often used when a high degree of surface quality is required.
casting sand suppliers
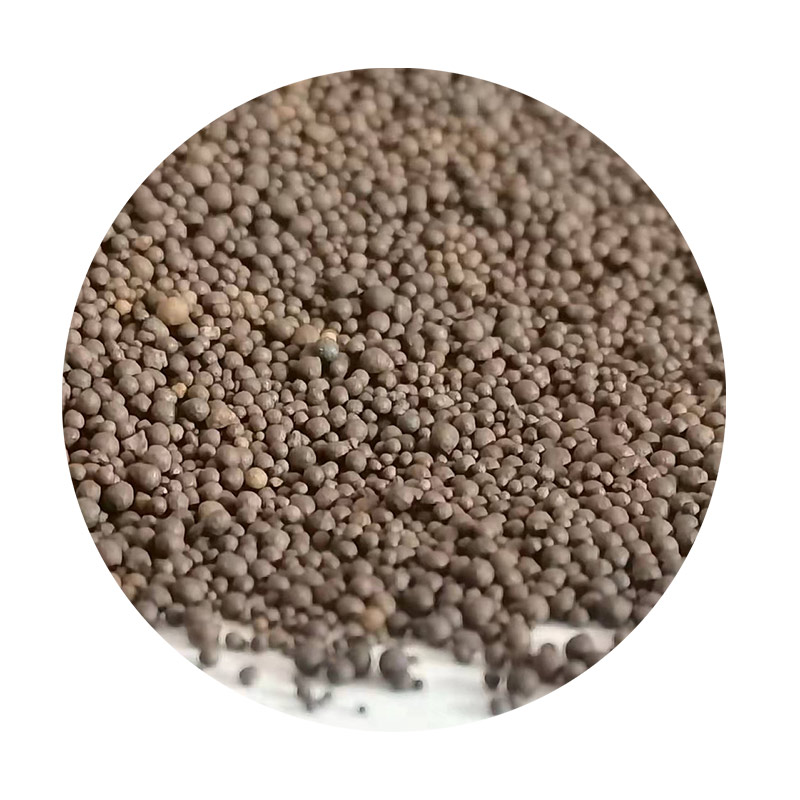
By understanding the different types of casting sand, foundries can make informed choices about which materials will best meet their production needs
.The Role of Casting Sand Suppliers
Casting sand suppliers play a critical role in the supply chain of the foundry industry. They are responsible for sourcing, processing, and distributing various types of casting sand. The quality of sand supplied can significantly influence the efficiency of production processes, the performance of the molds, and ultimately, the quality of the finished products.
Suppliers must not only provide high-quality materials but also ensure that they understand their clients' specific requirements. This includes offering technical support, advice on the best types of sand for various applications, and assistance with supply chain logistics. A responsive and knowledgeable supplier can help foundries optimize their production processes, leading to better yield and reduced costs.
Challenges in the Supply of Casting Sand
Despite the importance of casting sand suppliers, the industry faces several challenges. Environmental regulations, fluctuations in raw material availability, and changes in market demand can significantly impact the supply of casting sand. For example, increased awareness and concern over environmental issues have led to stricter regulations on mining and production processes, influencing the availability of high-quality silica sand.
Additionally, suppliers must also navigate the economic landscape, which can affect the pricing of raw materials. Global trade tensions, supply chain disruptions, and competition among suppliers can lead to instability in the market. To remain competitive, casting sand suppliers must adopt innovative approaches and technologies, such as investing in sustainable sourcing practices and process optimization.
Conclusion
Casting sand suppliers are a vital link in the foundry industry chain, providing the essential materials that enable the manufacturing of high-quality metal components. As the industry evolves, suppliers must adapt to new challenges while ensuring they maintain high standards of quality and service. By doing so, they can continue to support foundries in meeting the ever-increasing demands for efficient and effective manufacturing processes, ultimately contributing to the growth and development of the broader manufacturing sector. As foundries increasingly seek out tailored solutions, the collaboration between suppliers and manufacturers will become ever more critical in driving innovation and maintaining competitiveness in this dynamic industry.
Post time:Ное . 15, 2024 18:06
Next:steel sand casting