Sand Casting A Comprehensive Overview
Sand casting, also known as sand mold casting, is one of the oldest and most widely used manufacturing processes for producing metal parts. This method has been utilized for centuries and continues to be highly relevant in modern manufacturing due to its versatility, cost-effectiveness, and ability to produce complex geometries. This article aims to define sand casting, describe its process, outline its advantages and disadvantages, and explore its applications in various industries.
What is Sand Casting?
At its core, sand casting is a metal casting process that involves creating a mold from sand, into which molten metal is poured to form a specific shape. The term sand casting is derived from the use of sand as the primary molding material, which is typically mixed with a binder to provide strength and cohesiveness. This process can be used with a range of metals, including aluminum, copper, iron, and others, making it an incredibly versatile manufacturing technique.
The Sand Casting Process
The sand casting process involves several key steps
1. Pattern Making A pattern is created, typically from wood, metal, or plastic. This pattern replicates the final product's shape and is used to form the mold. Patterns can be single-piece or multipart, depending on the complexity of the desired shape.
2. Mold Preparation Fine sand is mixed with a binder (usually clay) and water to form a moldable mixture. This mixture is packed around the pattern in a two-part mold, which is then removed to create a cavity in the shape of the pattern.
3. Cavity Creation The mold halves are assembled, and any additional features, such as gates (for pouring the metal) and vents (for releasing gases), are incorporated.
4. Melting and Pouring The chosen metal is melted in a furnace and poured into the mold cavity. The molten metal fills the space and takes on the shape of the pattern.
5. Cooling and Solidification After pouring, the metal is allowed to cool and solidify. The cooling time depends on the type of metal and the thickness of the casting.
6. Mold Removal and Finishing Once solidified, the mold is broken open to remove the casting. This is followed by finishing operations, such as grinding or machining, to achieve the desired surface finish and dimensions.
Advantages of Sand Casting
Sand casting offers several advantages that have contributed to its enduring popularity
sand casting definition
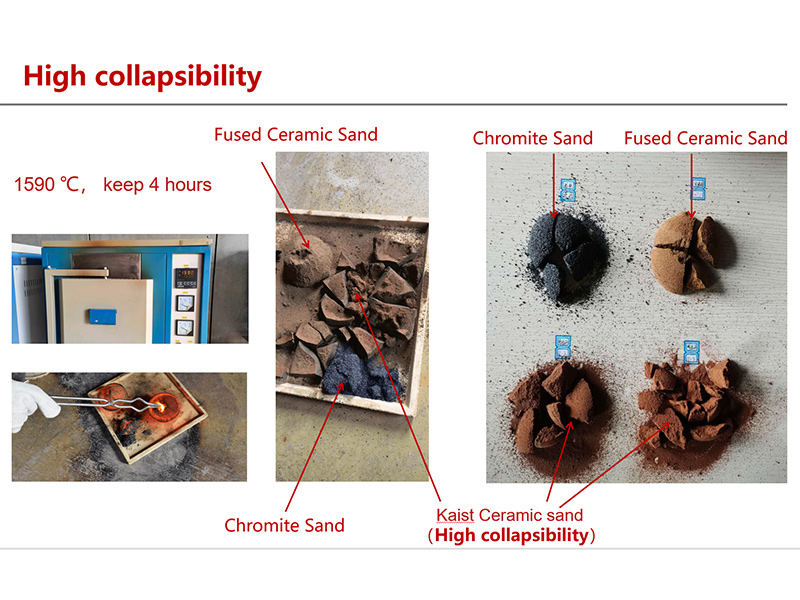
- Cost-Effectiveness The materials required for sand casting are relatively inexpensive compared to other casting methods. Sand can be reused many times, reducing material costs.
- Versatility Sand casting can accommodate a wide range of metals and allows for the production of complex shapes, making it suitable for various applications
.- Scalability This method is capable of producing both small quantities of unique parts and large-scale production runs, making it suitable for a wide array of manufacturing needs.
- Tolerance and Surface Finish Depending on the level of expertise and finishing processes employed, sand casting can achieve relatively good dimensional tolerance and surface finishes.
Disadvantages of Sand Casting
Despite its benefits, sand casting does have some limitations
- Labor-Intensive The process requires skilled labor for pattern making, mold preparation, and finishing, which can increase production time.
- Surface Finish While improvements can be made, the surface finish of sand-cast parts is generally not as smooth as that produced by other casting methods, such as investment casting.
- Dimensional Precision Sand casting may not achieve the tight tolerances required for certain applications, making it less suitable for highly precise components.
Applications of Sand Casting
Sand casting can be found in various industries, including
- Automotive Used to produce engine blocks, cylinder heads, and other critical components. - Aerospace Employed for creating complex parts that require lightweight yet strong materials. - Manufacturing Implemented for producing machinery components and tools. - Art and Sculpture Craftsmen and artists use sand casting for creating unique artistic pieces.
In conclusion, sand casting remains a fundamental and widely used method in the metalworking industry. Its affordability, adaptability to different materials, and capability of creating intricate designs ensure that it will continue to play a significant role in manufacturing for years to come. Whether for industrial applications or artistic endeavors, the importance of sand casting is undeniable.
Post time:Okt . 11, 2024 20:58
Next:types of sand casting process