The Difference Between Sand Casting and Investment Casting
When it comes to metal casting processes, two of the most commonly used methods are sand casting and investment casting. Each of these techniques serves specific purposes and has distinct advantages and disadvantages, making them suitable for different applications. Understanding the differences between sand casting and investment casting is crucial for manufacturers seeking to optimize their production processes.
Overview of Sand Casting
Sand casting is one of the oldest and simplest metal casting processes, employing a mixture of sand, clay, and water to form a mold. This method is highly versatile and can accommodate a variety of metals, including aluminum, iron, and bronze. The sand mold is created by compacting the sand mixture around a pattern, which is a replica of the final product. Once the mold is prepared, molten metal is poured into it, left to cool, and then removed to reveal the final cast part.
Advantages of Sand Casting
1. Cost-Effective Sand casting is relatively inexpensive due to the low cost of materials (sand and clay) and the straightforward equipment used. 2. Flexibility in Size and Shape This method can produce large parts and complex shapes, making it suitable for a wide range of applications, from automotive components to large industrial parts. 3. High Throughput Sand casting can be performed quickly, allowing for mass production of components.
Disadvantages of Sand Casting
1. Surface Finish The surface finish of sand cast components is generally rough, which may require additional machining or finishing processes. 2. Dimensional Tolerances Sand casting typically has lower dimensional accuracy compared to investment casting, which can lead to challenges in achieving precise specifications.
Overview of Investment Casting
difference between sand casting and investment casting
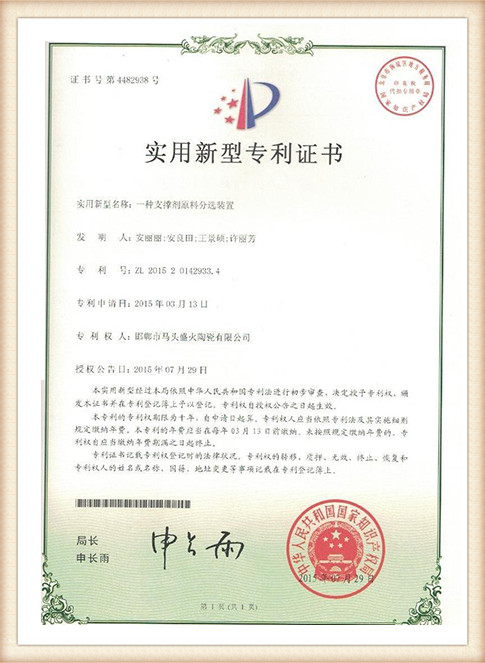
Investment casting, also known as lost-wax casting, is a more intricate process that involves creating a wax pattern coated with a ceramic shell. The wax is melted away, leaving a mold that can capture finer details and maintain more precise dimensions. Investment casting is particularly well-suited for complex geometries and is often used for producing parts in the aerospace, medical, and jewelry industries.
Advantages of Investment Casting
1. Precision and Detail Investment casting can achieve very tight tolerances and intricate designs, making it ideal for applications where accuracy is paramount. 2. Superior Surface Finish The ceramic shell mold provides a smoother finish compared to sand casting, often reducing or eliminating the need for additional finishing operations. 3. Material Versatility Investment casting allows for a broader range of materials, including high-performance alloys that may not be suitable for sand casting.
Disadvantages of Investment Casting
1. High Cost The initial setup and production costs for investment casting are generally higher due to the complex molds and materials used. 2. Production Time While investment casting produces high-quality parts, the process can be slower than sand casting, especially for larger production runs.
Key Differences
1. Mold Creation In sand casting, molds are made of sand, while in investment casting, a wax pattern is used to create a ceramic mold. 2. Surface Finish Investment casting provides a superior surface finish and higher accuracy compared to sand casting. 3. Cost and Time Sand casting is more cost-effective and quicker for larger parts, whereas investment casting is more suited for precision parts with complex designs, albeit at a higher cost. 4. Applications Sand casting is often used for producing larger and less intricate parts, while investment casting excels in applications requiring high precision and fine detail.
Conclusion
In summary, both sand casting and investment casting have their unique strengths and weaknesses, making them suitable for different manufacturing needs. Sand casting is an economical option for larger, simpler components, while investment casting is preferred for its ability to produce highly detailed and accurate parts. Manufacturers must carefully consider their specific requirements, including material, design complexity, and cost constraints, when choosing between these two casting methods. Understanding these differences enhances the ability to select the most appropriate casting process, ultimately contributing to improved product quality and efficiency in production.
Post time:Nov . 20, 2024 00:58
Next:advantage of sand casting