Why Sand Casting is Preferred
Sand casting, also known as sand molded casting, is a widely used manufacturing process for creating metal parts. It involves pouring molten metal into a cavity formed by sand molds. This method has been around for centuries and remains popular today for several reasons, including its versatility, cost-effectiveness, and the quality of the finished product. In this article, we will delve into the reasons why sand casting is often preferred for various applications.
1. Versatility in Materials
One of the primary advantages of sand casting is its ability to accommodate a wide range of metals and alloys. Whether it's ferrous metals like cast iron and steel or non-ferrous metals such as aluminum, copper, and magnesium, sand casting can handle them all. This versatility makes it an ideal choice for industries requiring different materials based on the specific demands of their applications. Moreover, the process can also produce complex shapes and large components that may be difficult or impractical to achieve with other casting methods.
2. Cost-Effectiveness
Cost considerations play a significant role in the manufacturing process, and sand casting helps keep costs low. The materials used for sand molds—primarily silica sand—are inexpensive and readily available. In comparison to other casting methods that require more intricate and expensive tooling, sand casting utilizes simpler patterns, which helps reduce initial investment costs. Additionally, sand molds can be reused several times, further lowering production expenses. This economical approach is especially beneficial for small to medium-sized production runs where budgets may be tight.
3. Large Scale Production Capability
Sand casting is particularly suited for large-scale production. The manufacturing process allows for quick setup and production of multiple parts in a relatively short time frame. Since the molds can be created rapidly, manufacturers can produce a high volume of components without incurring significant delays. This efficiency is particularly important for industries such as automotive, aerospace, and heavy machinery, where time and cost are critical factors.
why sand casting is preferred
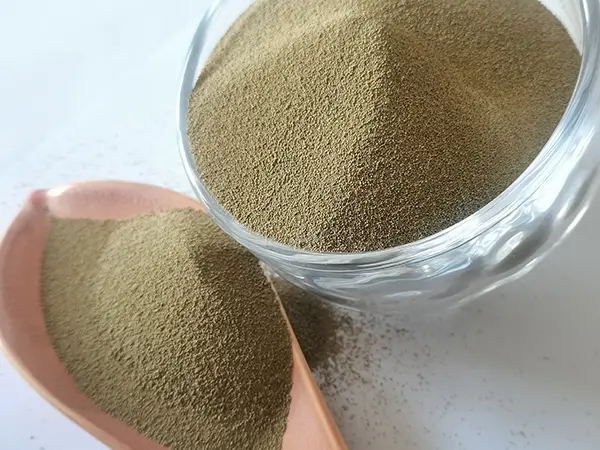
4. Ability to Create Complex Geometries
The flexibility of sand casting allows for the creation of intricate designs that may be challenging for other casting techniques. The process can easily form complex shapes, making it suitable for a variety of applications. This capability is vital in industries where hydraulic systems, engine components, and artistic pieces require detailed specifications. Sand casting also permits the incorporation of various features, such as ribs, bosses, and cooling channels, directly into the mold.
5. High Tolerance and Surface Finish
Advancements in sand casting technology have led to improved tolerances and surface finishes. Modern sand casting techniques allow for the production of precision castings with acceptable geometric tolerances. Coupled with surface treatments such as shot blasting or sanding, the final products can meet stringent quality standards. This high level of finish is essential in applications where appearance, as well as mechanical properties, is crucial.
6. Environmental Considerations
Sustainability has become a critical factor in manufacturing processes, and sand casting aligns well with environmentally friendly practices. The sand used in the molds can be recycled and reused, reducing waste material. Additionally, modern sand casting operations have implemented techniques to minimize energy consumption and emissions, further supporting eco-friendly initiatives.
Conclusion
Sand casting continues to be a favored method of metal fabrication due to its numerous advantages, including versatility, cost-effectiveness, production efficiency, and the ability to create complex shapes. It serves a variety of industries, from automotive to aerospace, where quality and precision are paramount. As technology evolves, the sand casting process is likely to see further enhancements, making it an even more attractive option for manufacturers seeking reliable and economical solutions for their metal casting needs. Whether for large production runs or custom applications, sand casting remains an invaluable technique in the landscape of modern manufacturing.
Post time:Gru . 31, 2024 07:55
Next:Sand Casting Services for Precision Parts and Custom Fabrication Solutions