The Importance of Sand Type in Sand Casting
Sand casting is one of the oldest and most versatile metal casting processes. It involves pouring molten metal into a mold made of sand, which forms the shape of the desired object after cooling. While many factors can influence the quality of a sand-cast product, the type of sand used is particularly crucial. This article explores the characteristics of various types of sand suitable for sand casting and their implications for the casting process.
Types of Sand Used in Sand Casting
1. Silica Sand The most common type of sand used in sand casting is silica sand, which is primarily composed of silicon dioxide (SiO2). Its popularity stems from its abundant availability and good thermal properties. Silica sand can withstand high temperatures, making it ideal for casting metals such as aluminum, iron, and steel. However, its ability to stick to the patterns can sometimes lead to difficulties in removing the mold.
2. Green Sand Often considered the “traditional” casting sand, green sand is a mixture of silica sand, clay, water, and other additives. The clay serves as a binder, giving the sand its strength and plasticity. Green sand is highly prized for its ability to retain moisture, ensuring that the mold holds its shape during the pouring of the molten metal. This type of sand is particularly useful for making intricate patterns, as it can easily fill small details. However, green sand can absorb moisture from the environment, which may affect casting quality if not properly managed.
3. Resin Sand This sand type is a mixture of silica sand and a phenolic resin binder that hardens when exposed to heat. Resin sand molds exhibit high strength and thermal stability, leading to better dimensional accuracy in the final castings. This makes resin sand an excellent choice for high-volume production runs and complex shapes. While it can produce superior surface finishes and detail, the cost of resin sand is typically higher than that of traditional green sand.
what type of sand is used in sand casting
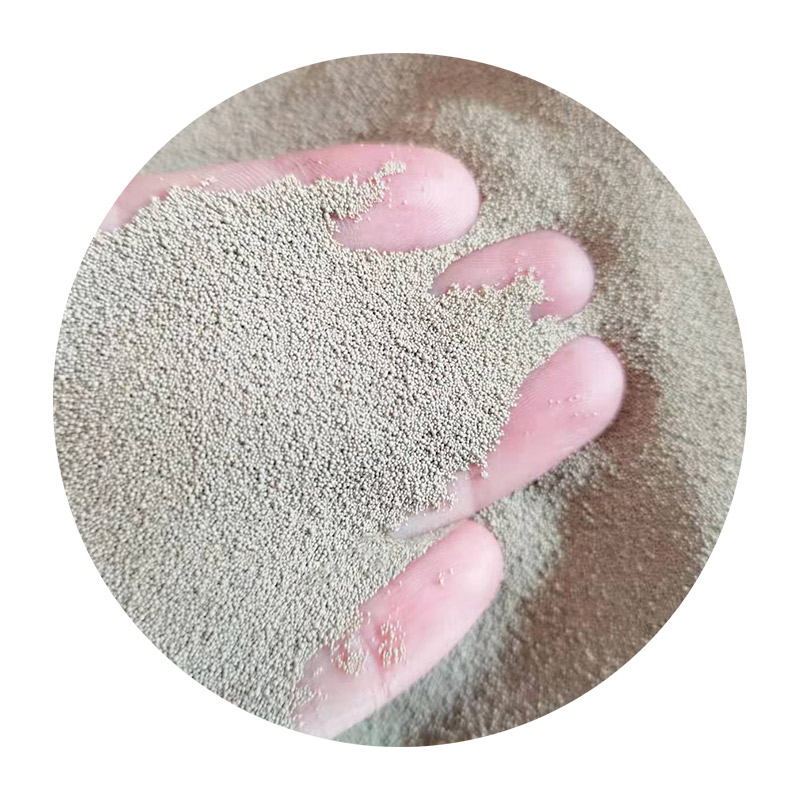
4. Ceramic Sand Used primarily in high-performance applications, ceramic sand is made from high-purity materials that provide excellent thermal and mechanical properties. This type of sand can withstand higher temperatures than traditional silica sand, making it ideal for casting high-temperature alloys. The smooth surface finish of ceramic sand also reduces the need for secondary machining processes, which can enhance productivity.
5. Shell Molding Sand Shell molding involves creating molds from a mixture of fine sand and thermosetting resin. This process results in very thin, strong, and high-precision molds. Shell molding is particularly beneficial for producing complex geometries and thin-walled castings. While shell molding sand is typically more expensive, the advantages in terms of casting quality often justify the investment.
Conclusion
The type of sand used in sand casting significantly impacts the resulting quality of the casted product. Each type of sand has its unique properties that make it suitable for specific applications in the casting process. Silica sand is widely used for its availability and thermal properties, while green sand provides a traditional approach with its moisture retention capabilities. On the other hand, resin sand and ceramic sand offer advancements in strength, durability, and surface finish desirable for modern manufacturing needs.
Understanding the characteristics of each type of sand allows foundries and manufacturers to select the most appropriate materials for their specific casting requirements, leading to enhanced quality, reduced defects, and overall improved efficiency in the casting process. As technology continues to advance, innovations in sand types and their respective binders will likely lead to further improvements in the sand casting industry.
Post time:Lap . 28, 2024 09:02
Next:Фасаванне пяску ў ліцьцях і яго ўплыў на якасць прадукцыі