What is Foundry Sand?
Foundry sand is a crucial material used in the metal casting industry. It plays a vital role in the manufacturing process of various metal products, providing the necessary properties to produce complex shapes with high precision. This article will delve into the characteristics, types, applications, and environmental considerations associated with foundry sand, highlighting its significance in modern manufacturing.
Characteristics of Foundry Sand
Foundry sand is typically comprised of silica, which is known for its excellent thermal stability, resistance to high temperatures, and ability to retain its shape during the casting process. The most common type of foundry sand is green sand, a mixture of sand, clay, and water. This sand is favored for its ability to form a strong mold that can withstand the pour of molten metal. The clay content helps to bind the sand grains together, leading to a cohesive mixture that is easy to work with.
Another key characteristic of foundry sand is its grain size. The grain size can influence the surface finish and dimensional accuracy of the final cast product. Fine sand is often preferred when intricate details are required, while coarser sands are used for larger, less detailed castings. Additionally, the shapes of the sand grains can vary, with angular grains providing better packing density, and rounded grains offering increased flowability.
Types of Foundry Sand
While silica sand is the most widely used type of foundry sand, there are other materials available, each offering unique properties that enhance the casting process. For example, chromite sand is used for its high resistance to thermal shock and its ability to resist metal penetration, making it particularly useful for casting high-alloy steels. Zircon sand is another alternative, known for its low thermal expansion and ability to provide a smooth surface finish.
Synthetic sands, made from processed materials, have also gained popularity in the foundry industry. These sands can be engineered to achieve specific properties, such as thermal conductivity and permeability, allowing for more tailored solutions for diverse casting applications.
what is foundry sand
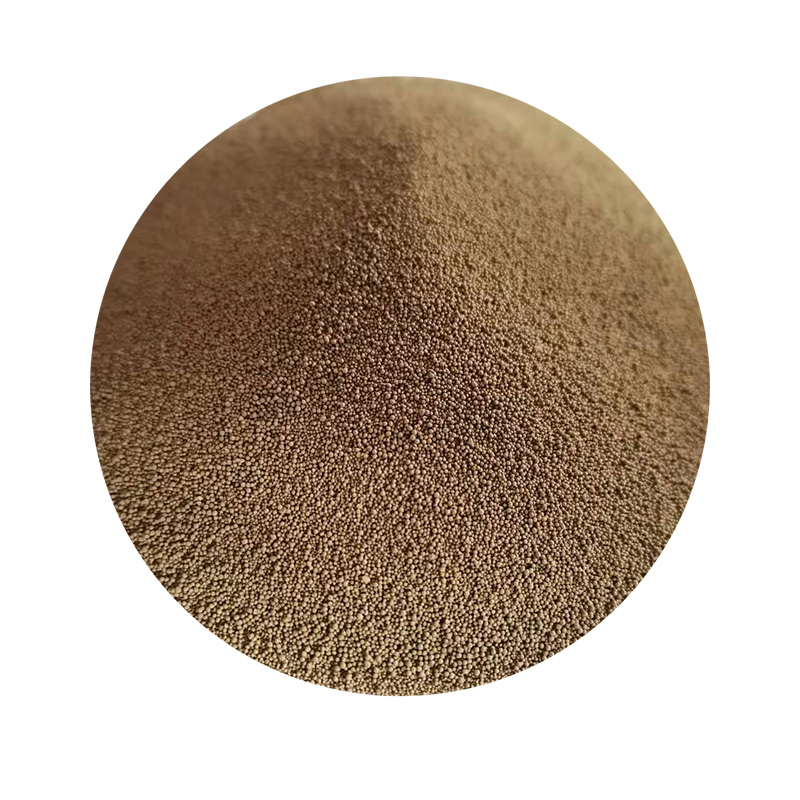
Applications of Foundry Sand
Foundry sand is primarily used in the production of metal castings for various industries, including automotive, aerospace, construction, and agriculture. The sand is used to create molds and cores, which shape the metal as it cools and solidifies. This process is essential for creating complex geometries that would be difficult or impossible to achieve through other manufacturing methods, such as machining or forging.
The automotive industry is one of the largest consumers of foundry sand, utilizing it to manufacture engine blocks, transmission cases, and other components. Similarly, the aerospace sector relies on foundry sand for producing lightweight yet strong components in aircraft engines and structural parts.
Environmental Considerations
The use of foundry sand does raise environmental concerns, primarily associated with the management of spent sand, which can accumulate after repeated use in the casting process. Proper disposal of spent foundry sand is crucial, as it may contain contaminants from the casting process, such as heavy metals or organic compounds.
However, many foundries are now adopting sustainable practices by reusing spent sand or recycling it for various applications, such as construction materials, land reclamation, or in the manufacturing of concrete. This not only minimizes waste but also reduces the environmental footprint of foundry operations.
Conclusion
In summary, foundry sand is an indispensable material in the metal casting industry, characterized by its versatility, thermal stability, and ability to produce high-quality castings. With various types of sand available, each offering unique properties, the foundry industry continues to evolve, adapting to new technologies and sustainability practices. As manufacturing processes become increasingly sophisticated and environmentally conscious, the role of foundry sand will undoubtedly remain pivotal in meeting the demands of modern production.
Post time:Gru . 21, 2024 01:30
Next:3d print sand