Steps in Sand Casting A Comprehensive Guide
Sand casting, also known as sand mold casting, is one of the oldest and most versatile manufacturing processes used for producing metal parts. This method utilizes sand as the primary mold material and offers various advantages, including the ability to create complex shapes and its efficiency in producing small to large quantities. The following sections outline the fundamental steps involved in the sand casting process, optimizing our understanding of this manufacturing technique.
Step 1 Designing the Pattern
The first step in sand casting is to create a pattern. A pattern is a replica of the final product and can be made from materials such as wood, plastic, or metal. The design of the pattern must consider the shrinkage of the metal as it cools, so it is typically made slightly larger than the desired final dimensions. Patterns can be single-use (for a single casting) or reusable (for multiple castings), depending on the production needs. Additionally, the pattern must include allowances for machining and surface finish.
Step 2 Preparing the Sand Mold
Once the pattern is completed, the next step is preparing the sand mold. This process involves mixing sand with a binding agent (usually clay) and water to form a cohesive mixture. The sand must be of high quality to ensure good mold strength and surface finish. The mixture is then packed around the pattern in a mold box, which can be made from metal or wood. Once the sand is tightly packed, the pattern is removed, leaving a cavity in the shape of the desired part.
Step 3 Assembling the Mold
After creating the sand molds, the next step is to assemble the two halves of the mold (cope and drag). It is essential to ensure that the two halves align properly to avoid any casting defects. The mold may also require additional features such as risers and gates. Risers provide extra molten metal for shrinkage, while gates serve as pathways for the metal to flow into the mold cavity. Proper design and placement of these components are critical for achieving a successful casting.
steps in sand casting
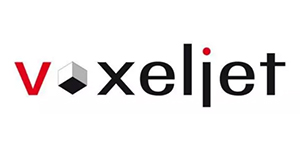
Step 4 Pouring the Molten Metal
With the mold assembled, it is now time to pour the molten metal. Before pouring, the mold is preheated to minimize temperature shock and improve the quality of the casting. Once the metal reaches the desired temperature, it is poured into the mold through the gates. It is crucial to control the pouring speed and temperature to prevent issues such as turbulence or premature solidification. Proper pouring techniques help ensure that the mold is filled evenly, producing a high-quality cast.
Step 5 Cooling and Solidification
After pouring, the molten metal must cool and solidify within the mold. The cooling time varies based on the thickness of the cast and the type of metal used. During solidification, the metal will shrink, which is why risers are critical to ensure that the mold remains filled throughout this phase. Once the metal has cooled sufficiently, the mold can be broken apart to reveal the casting.
Step 6 Cleaning and Finishing the Casting
After the casting has been removed from the mold, it typically requires cleaning to remove any residual sand and impurities. This can be done through processes like sand blasting or tumbling. Following the cleaning, the casting may undergo machining to achieve the desired tolerances and surface finish. Additional finishing processes such as painting, plating, or heat treatment might also be required depending on the specifications of the final product.
Conclusion
Sand casting is a time-tested method for producing complex metal parts with relatively low equipment costs. Understanding the steps involved in the sand casting process—from pattern design to the final finishing—can help manufacturers optimize their production processes and improve product quality. With advancements in technology, such as computer-aided design and 3D printing, the sand casting process continues to evolve, offering even greater flexibility and efficiency in metal manufacturing. Whether used for prototyping or mass production, sand casting remains a preferred choice in various industries due to its versatility and effectiveness.
Post time:Lap . 07, 2024 06:46
Next:Understanding the Sand Casting Foundry Method for Efficient Metal Production Processes