Sand Casting Applications An Overview
Sand casting, one of the oldest and most versatile manufacturing processes, has remained a cornerstone in the metal casting industry for centuries. This method involves pouring molten metal into a sand mold, which can be shaped and designed to produce a myriad of components used across various sectors. The applications of sand casting are extensive, making it a preferred choice for many manufacturing scenarios due to its cost-effectiveness, flexibility, and ability to create intricate designs.
1. Automotive Industry
One of the most significant applications of sand casting is found in the automotive industry. The production of engine blocks, cylinder heads, and transmission cases often relies on this technique. The automotive sector necessitates high-volume production of durable parts that can withstand harsh operational environments, and sand casting offers an efficient solution. Additionally, the ability to produce complex shapes with internal cooling passages and lightweight designs makes it ideal for the evolving demands of modern vehicles, especially with the rise of electric vehicles where lightweight components are crucial for efficiency.
2. Aerospace Applications
In the aerospace industry, sand casting plays a critical role in manufacturing components that require high precision and excellent strength-to-weight ratios. Parts such as turbine housings, engine brackets, and landing gear components are often produced using sand casting. The ability to create intricate geometries that can accommodate the stringent regulations set by aviation authorities is essential. Moreover, advancements in sand casting processes have improved the quality and consistency of the castings, ensuring that they meet the high safety standards required in aerospace applications.
sand casting applications
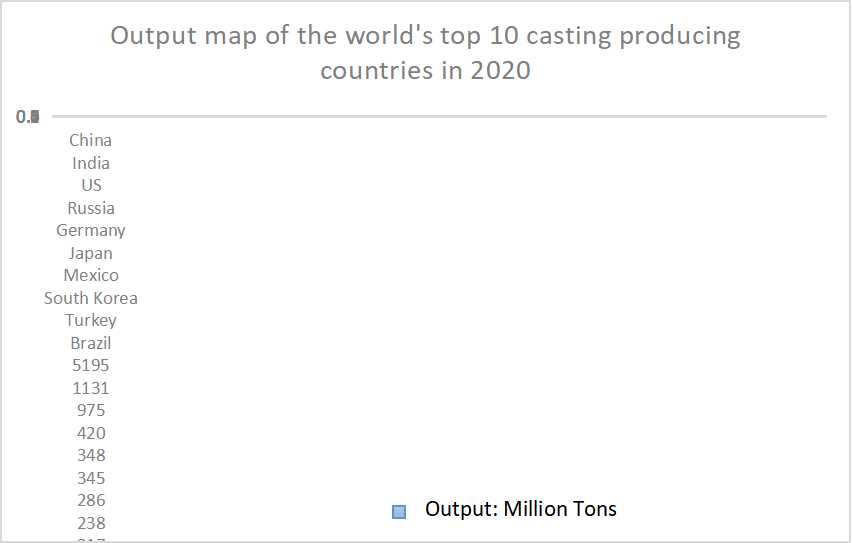
The industrial machinery sector relies heavily on sand casting for producing components such as gears, housings, and frames. These components typically demand high durability and resistance to wear and tear due to the nature of their applications in manufacturing equipment. The sand casting process allows manufacturers to produce large parts without significant tooling costs, making it economical for producing custom machinery components or low-volume runs. Additionally, the ability to use various metals and alloys in sand casting enhances the adaptability of this process to meet specific industrial needs.
4. Artistic and Architectural Applications
Beyond functional components, sand casting has significant applications in the artistic and architectural fields. Artists and designers use sand casting to create intricate sculptures, decorative pieces, and architectural elements. This method provides the flexibility to produce detailed designs that might be challenging to achieve through other manufacturing processes. Furthermore, the tactile and aesthetic qualities of cast metals enhance the artistic value of these creations, making them popular in both public installations and private art collections.
5. Marine Industry
The marine industry also benefits from sand casting, particularly in the production of components such as ship propellers, engine mounts, and valve bodies. These parts must exhibit excellent corrosion resistance and durability, given their exposure to harsh environmental conditions. Sand casting, with its ability to produce complex shapes and its compatibility with a variety of metal alloys, serves the marine sector well. Innovations in sand casting techniques also continue to improve the performance characteristics of these components, ensuring reliability and safety at sea.
Conclusion
Sand casting remains an essential manufacturing process across various industries. Its adaptability, cost-effectiveness, and ability to produce complex shapes make it a preferred choice for many applications. From automotive parts to aerospace components, industrial machinery, art, and marine applications, the versatility of sand casting knows no bounds. As technology advances, so too will the applications of sand casting, ensuring its relevance in the evolving landscape of manufacturing. Whether producing massive engine blocks or delicate artistic pieces, sand casting will continue to shape the materials that drive our industries forward.
Post time:Gru . 04, 2024 20:40
Next:Techniques for Effectively Wet Sanding Your 3D Printed Models for a Smooth Finish