Sand Casting Mass Production A Comprehensive Overview
Sand casting, also known as sand mold casting, is one of the oldest and most versatile methods of metal casting. This process involves creating a mold from sand, into which molten metal is poured to create a specific shape. The simplicity and effectiveness of sand casting make it an ideal choice for mass production in various industries, including automotive, aerospace, and construction.
The Sand Casting Process
The sand casting process begins with creating a pattern, which is a replica of the final product to be cast. This pattern is typically made from metal, plastic, or wood. The goal is to achieve high accuracy in the shape and dimensions of the final piece. Once the pattern is created, it is placed in a mold box, which is then filled with a mixture of sand and a bonding agent, commonly clay. The sand is compacted around the pattern to form a mold.
After the sand has set, the mold is carefully separated, and the pattern is removed. This leaves a negative impression in the sand, which serves as the cavity for the molten metal. The mold is then reassembled, and molten metal is poured into the cavity. After the metal has cooled and solidified, the sand mold is broken apart, and the casting is removed.
Advantages of Sand Casting for Mass Production
1. Cost-Effectiveness One of the primary benefits of sand casting is its low production cost, particularly for large parts. The materials needed for creating the sand molds are inexpensive compared to other casting methods, such as investment casting.
2. Flexibility Sand casting can accommodate a wide variety of shapes and sizes, from simple components to complex geometries. This flexibility is crucial in mass production, where specifications may change based on market demands.
sand casting mass production
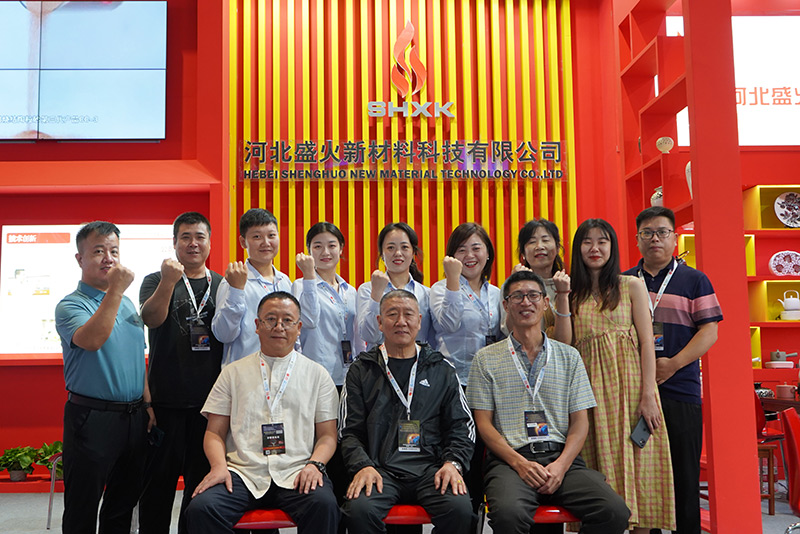
3. Material Versatility Sand casting can be used with various metals, including aluminum, iron, bronze, and steel. This versatility allows manufacturers to choose the most suitable material for the specific application, enhancing performance and cost-effectiveness.
4. Scalability Sand casting is highly scalable. Whether producing a few units or thousands, the process can be easily adapted to meet production requirements. Automated sand casting systems can significantly increase throughput, allowing for efficient mass production.
5. Reduced Lead Times The speed of the sand casting process means that lead times can be significantly reduced. With shorter product development cycles, manufacturers can respond quickly to customer demands and market changes.
Challenges and Solutions in Mass Production
While sand casting has numerous advantages, it also presents certain challenges, particularly in achieving surface finish and dimensional accuracy. The rough surface texture of sand-cast items might require subsequent machining processes, which can increase production time and costs. To address this, manufacturers often employ techniques such as using finer sand or refining the mold-making process.
Additionally, sand casting may have limitations in producing very small or intricate parts. In such cases, alternative methods like die casting or precision casting might be more suitable. However, with advances in technology, including 3D printing for creating complex molds, the capabilities of sand casting continue to expand.
Conclusion
In conclusion, sand casting remains a vital process in the realm of mass production. Its cost-effectiveness, flexibility, and material versatility make it an attractive choice for manufacturers across various industries. By acknowledging and addressing its challenges, the sand casting process can continue to evolve, meeting the demands of modern manufacturing with efficiency and precision. As industries advance, innovative solutions will ensure that sand casting retains its significance in mass production for years to come.
Post time:Rgp . 30, 2024 17:09
Next:how to make foundry sand