Understanding the Composition of Foundry Sand
Foundry sand is a crucial element in the metal casting industry, serving as a mold material for various types of metals and alloys. Its composition primarily comprises silica, but it can also include various other components and additives that enhance its performance. Understanding the composition of foundry sand is essential for producing high-quality castings and ensuring the efficiency of the casting process.
At its core, foundry sand consists of a high percentage of silica sand, typically around 90-95%. Silica sand is chosen for its excellent properties, such as high thermal resistance, low expansion, and the ability to hold shapes under heat. The size of the sand grains, as well as their shape and distribution, significantly influences the sand's performance. Fine grains provide greater surface area for heat transfer and help achieve smooth casting surfaces, while coarser grains offer better flowability and can reduce defects in casting.
In addition to silica, foundry sand may contain clay, which acts as a binder to hold the sand grains together. Clay improves the cohesiveness of the sand and increases its ability to withstand the pressure of molten metal. Bentonite is a commonly used clay in foundry sand preparation, known for its excellent binding properties. Generally, clay content ranges from 2% to 8%, depending on the specific requirements of the casting operation.
Moreover, various additives are often introduced to improve the performance of foundry sand. These can include chemical binders, which help create a firmer mold and improve the surface finish of the casting. Other additives may be used to enhance the sand's thermal stability or to modify its expansion properties. For example, some foundries incorporate resin-coated sands that allow for a hard shell mold, providing superior detail and strength.
foundry sand composition
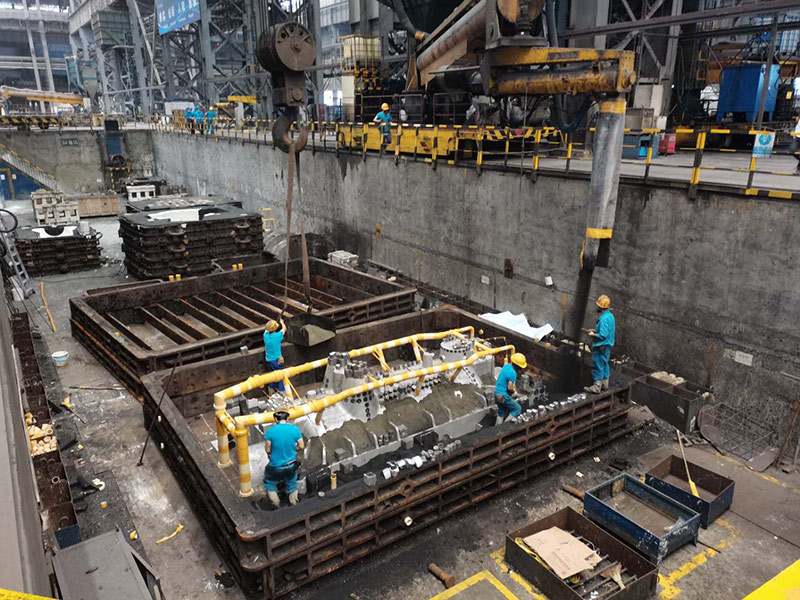
An important aspect of foundry sand composition is the moisture content, which can affect the sand's flowability and mold strength
. Properly controlling moisture levels is vital, as excess moisture can lead to casting defects, such as gas porosity or sand adhering to the casting. Generally, the moisture content is maintained at around 2-4%.Recycling used foundry sand is another critical consideration for the industry. Many foundries strive to minimize waste and improve sustainability by recovering and reusing foundry sand. However, to ensure that recycled sand meets quality standards, it must undergo thorough cleaning and processing. Recycling practices can significantly alter the composition of foundry sand, as they may introduce contaminants that were present in previous castings. Therefore, the evaluation of recycled foundry sand composition is essential before its reuse.
The choice of foundry sand composition often depends on the type of metal being cast and the specific requirements of the casting process. For instance, ferrous metals may require different sand properties compared to non-ferrous metals. Furthermore, the complexity of the casting design, along with the desired surface finish and dimensional tolerance, also influences the selection of the appropriate sand mix.
In conclusion, the composition of foundry sand is a multifaceted subject, playing a significant role in the overall success of the metal casting process. With silica as the primary component, along with clays, additives, and moisture control, foundry sand can be tailored to meet the diverse needs of various metal casting operations. A thorough understanding of the composition and performance characteristics of foundry sand is essential for foundries aiming to optimize their production processes and achieve high-quality castings.
Post time:Spa . 13, 2024 08:29
Next:Embedding Sand in Resin for Unique Art and Craft Creations