Understanding Foundry Molding Sand The Backbone of Metal Casting
Foundry molding sand is a crucial component in the metal casting process, playing a significant role in shaping and forming metal parts that are essential in various industries, including automotive, aerospace, and machinery. This article aims to provide an in-depth understanding of foundry molding sand, its types, properties, and its significance in casting processes.
What is Foundry Molding Sand?
Foundry molding sand is a specific type of sand used to create molds in which metal is poured and subsequently solidifies to form a certain shape. The primary function of this sand is to withstand the high temperatures associated with molten metal while providing a stable structure for the mold. Moreover, it should possess excellent permeability to allow gases generated during casting to escape without damaging the mold.
Types of Foundry Molding Sand
There are several types of foundry molding sands, each tailored to meet the unique requirements of different casting processes
1. Silica Sand The most commonly used type of molding sand, silica sand is favored for its high melting point and availability. Its grain shape and size can influence the mold's strength and its capacity to maintain fine details.
2. Clay-Bonded Sand Often mixed with water to create a mold, clay-bonded sand, commonly referred to as green sand, consists of silica sand, clay, and water. This mixture provides excellent adhesion and is easy to work with. It is widely used in ferrous and non-ferrous metal casting.
3. Oil-Bonded Sand This type of sand uses an oil binder, making it more suitable for high-temperature applications. Oil-bonded sands typically provide better surface finishes compared to green sand, making them ideal for intricate designs.
4. Resin-Bonded Sand This involves mixing sand with a resin binder that hardens upon heating. Resin-bonded sands offer high strength, excellent surface detail, and durability, making them popular for precision casting applications.
foundry molding sand
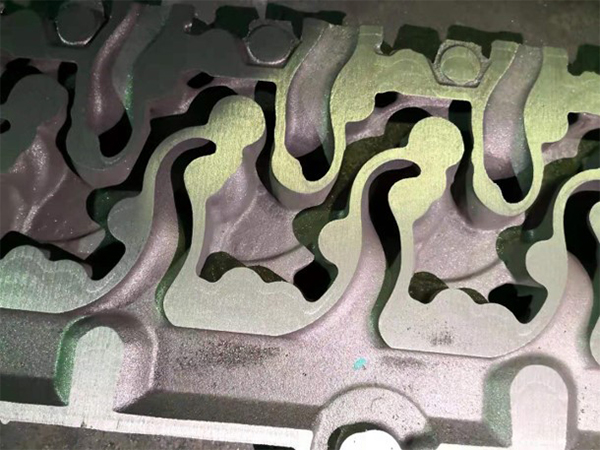
5. Specialty Sands Depending on specific casting requirements, specialized sands may be used, such as zircon sand, chromite sand, or olivine sand, which offer distinct thermal properties and advantages based on their chemical compositions.
Key Properties of Foundry Molding Sand
The performance of foundry molding sand is measured by several critical properties
- Grain Size and Shape These factors directly influence the mold's strength and ability to capture fine details. A well-graded sand will have a mix of different grain sizes to optimize packing density.
- Moisture Content The amount of water in the sand affects mold strength and thermal properties. A careful balance is required to maintain optimal moisture levels.
- Permeability This property allows gases to escape during the pouring of molten metal. Adequate permeability minimizes defects such as blowholes and ensures the integrity of the casting.
- Plasticity The ability of molding sand to be shaped and retain its form is crucial. Higher plasticity means better moldability and better handling during the casting process.
Importance of Foundry Molding Sand in Metal Casting
The use of high-quality foundry molding sand is critical for producing castings with minimal defects and high precision. The characteristics of the sand directly influence the final product's surface finish, dimensional accuracy, and mechanical properties. Conversely, using unsuitable or poor-quality sand can lead to casting defects like sand inclusion, poor surface finish, and reduced mechanical strength.
In conclusion, foundry molding sand serves as a vital element in the metal casting industry. Understanding the different types, properties, and roles of molding sand enables foundry engineers and metallurgists to choose the appropriate material for their specific casting needs, ensuring the production of high-quality metal components essential for various applications. As industries continue to evolve and demand precision-engineered parts, the importance of molding sand cannot be overstated, highlighting its role in the future of metal casting technology.
Post time:Gru . 14, 2024 03:48
Next:Affordable Gold Sand Available for Purchase Online