Understanding Foundry Molding Sand A Critical Component in Metal Casting
Foundry molding sand is an essential material used in the metal casting process, playing a significant role in shaping the final product. It serves as a medium to form molds, which hold molten metal and allow it to cool and solidify into a desired shape. The importance of foundry molding sand cannot be overstated, as it directly affects the quality, effectiveness, and efficiency of the casting process.
Composition and Types
Molding sand is primarily composed of silica grains, clay, and water. The silica serves as the primary component, providing the necessary strength and thermal stability. Clay, often bentonite, acts as a binding agent, giving the mold its cohesiveness and helping it retain its shape during the casting process. Water is added to facilitate the mold-making process and to activate the binding properties of the clay.
There are several types of foundry molding sands, each suited for specific applications. The most common types include
1. Green Sand This is a mixture of sand, clay, and water and is the most widely used molding material. It is called green because it is used in its moist state. Green sand molds are known for their excellent collapsibility, allowing for easy removal of the cast object.
2. Dry Sand Unlike green sand, dry sand molds are baked to remove moisture. This type of sand is used for more detailed patterns and offers better dimensional accuracy.
3. Shell Sand This is a thermosetting resin-coated sand that, when heated, forms a hard shell. Shell molds are used for producing high-quality castings with smooth surfaces and intricate details.
foundry molding sand
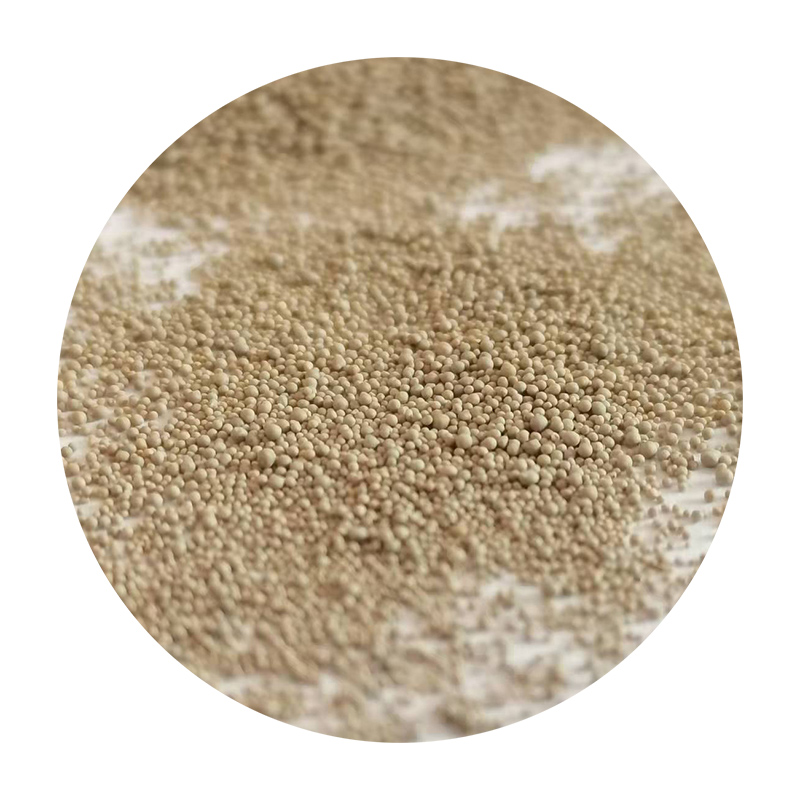
4. Investment Sand Often used for precision castings, investment sand molds are made from a fine, smooth material and are typically used in lost-wax casting processes.
Properties of Foundry Molding Sand
The effectiveness of molding sand is determined by several key properties
- Strength The ability to hold shape under mechanical stress is crucial, especially during pouring. - Permeability This allows gases produced during the solidification of the molten metal to escape, preventing defects like blowholes. - Refractoriness The sand's ability to withstand high temperatures without degrading is essential to avoid contamination and ensure the integrity of the final product. - Collapsibility Post-solidification, the sand should be easily removable without damaging the casting.
Recycling and Sustainability
One of the significant advantages of foundry molding sand is that it is highly recyclable. After use, sand can be reclaimed, cleaned, and reused in the molding process, reducing environmental impact and material costs. Many foundries adopt sustainable practices by recycling up to 90% of their sand, which not only contributes to sustainability but also enhances overall efficiency.
Conclusion
Foundry molding sand is a critical material in metal casting, with various types and properties that cater to different casting needs. The choice of molding sand influences the quality of castings, making it essential for foundries to select the right type based on the specific requirements of their projects. As the industry moves towards more sustainable practices, the recycling of molding sand has become increasingly important, highlighting the balance between effective production and environmental responsibility. By understanding the complexities of foundry molding sand, manufacturers can ensure high-quality castings while reducing waste and promoting sustainability in their operations.
Post time:Gru . 12, 2024 17:36
Next:sand cast metal